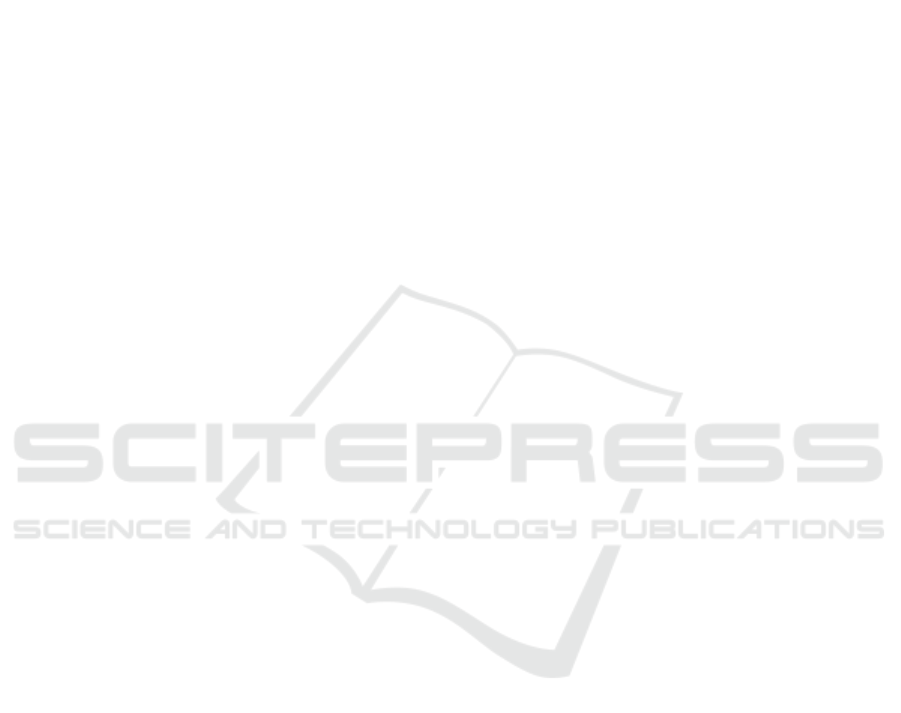
An Investigation on the Data Mining to Develop Smart Tire
Jae-Cheon Lee
1
, Hao Liu
1
, Young Gi Seo
2
, Seong Woo Kwak
2
, Ho Seung Lee
1
, Hae Jun Jo
1
and
Sangsu Park
2
1
Department of Mechanical and Automotive Engineering, Keimyung University, 1095 Dalgubeol-daero, Daegu, S. Korea
2
Department of Electronic and Electrical Engineering, Keimyung University, 1095 Dalgubeol-daero, Daegu, S. Korea
Keywords: Data Mining, Smart Tire, Tire Built-in Sensor, Strain Gage, Tire Deformation Value, Vehicle Load.
Abstract: A smart tire is required to improve driving safety for an intelligent vehicle especially for automated driving
electric vehicles. It is necessary to provide information of tire contact forces (vertical, longitudinal, and lateral
directions) to control velocity and steering angle of the autonomous vehicle so as to ensure driving stability.
This study presents a smart tire system with the data mining to estimate the vertical load by using the tire
deformation data in particular. Firstly, the hardware system construction of the smart tire in which tire
deformation on driving by using strain gauge is described. And then the test condition is set up and total 27
sets of experimental data are processed to perform correlation analysis for specifications of measured waves.
Next, the estimation algorithm of smart tire vertical load is derived by considering the area of tire-ground
contact patch and also by introducing compensate coefficient of transverse direction length of contact area.
The experimental results show the proposed estimation algorithm is feasible and precise. The advanced
adaptive and precise estimation algorithm with artificial neural network will be developed further.
1 INTRODUCTION
As the fourth industrial revolution approaches, the
development of automated driving vehicles has been
undertaken by major car manufactures with supplier
companies and various research institutes. While
electric powered complete autonomous car is final
goal, its safety and reliability issues must be solved
for commercialization.
Conventional vehicle motion control systems
estimate the grip force between the tire and the road
as well as the coefficient of road friction, the rigidity
and the slip angle based on the mathematical vehicle
dynamics model. However, the dynamic power
transfer rate from the power pack to the wheels of an
electric car is over 10ms faster than that of the internal
combustion engine’s vehicle. And the driving safety
of automated driving cars need immediate response
on the current road-vehicle situation. Therefore, in
order to reduce the time to calculate the grip force
between the tire and the road, sensors must be built
into the tire and be directly measured in real time. As
such, tires built-in sensors are referred to smart tires
(Park and Gerdes, 2015).
Measurement of the real-time deformation of a
tire has been a challenge in the field of smart tire
development (Matsuzaki and Todoroki, 2008). This
study used strain gauge sensor incorporated inside the
tire to measure the deformation of a tire. Then, a
unique algorithm was proposed to estimate the
vehicle load on each tire based on the time-varying
deformation data obtained by data mining technique
in real time. A method was also developed to
accurately calculate the ground area with the road
surface. To verify the proposed algorithm, a sensor-
driven electrical circuit was designed and a load
measurement experiment was conducted using the
vehicle tester. In addition, the measurement system
was implemented to detect the deformation of the tire
in real time.
The composition of this paper is as follows:
Section 2 describes the real-time instrumentation
system for detecting the deformation of a tire, and the
experimental conditions and data analysis are given
in Section 3. Section 4 proposes an algorithm to
obtain the vertical load using the measured
deformation data. It also describes how the
parameters needed for the proposed algorithm are
extracted. Section 4 shows the accuracy of proposed
algorithm by comparing the experimental actual load
and estimated load. Finally, Section 5 draws
conclusion.
480
Lee, J., Liu, H., Seo, Y., Kwak, S., Lee, H., Jo, H. and Park, S.
An Investigation on the Data Mining to Develop Smart Tire.
DOI: 10.5220/0007311104800487
In Proceedings of the 11th International Conference on Agents and Artificial Intelligence (ICAART 2019), pages 480-487
ISBN: 978-989-758-350-6
Copyright
c
2019 by SCITEPRESS – Science and Technology Publications, Lda. All rights reserved