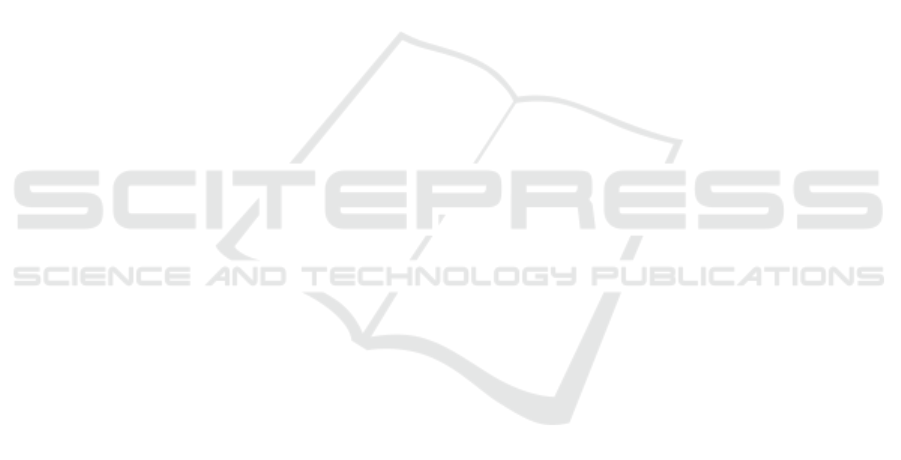
REFERENCES
ISO 25178: Geometric Product Specifications (GPS) Sur-
face texture: areal.
Alegre, E., Alaiz-Rodr
´
ıguez, R., Barreiro, J., Fidalgo,
E., and Fern
´
andez, L. (2010). Surface finish con-
trol in machining processes using haralick descrip-
tors and neuronal networks. In Computational Model-
ing of Objects Represented in Images, pages 231–241,
Berlin, Heidelberg. Springer Berlin Heidelberg.
Benardos, P. and Vosniakos, G.-C. (2003). Predicting sur-
face roughness in machining: a review. 43:833–844.
Brosius, F. (1998). SPSS 8. International Thomson Publish-
ing.
C. Gonzalez, R., E. Woods, R., and L. Eddins, S. (2004).
Digital Image Processing Using Matlab, volume 1.
Chandraratne, M., Samarasinghe, S., Kulasiri, D., and Bick-
erstaffe, R. (2006). Prediction of lamb tenderness us-
ing image surface texture features. 77:492–499.
Chen, Z., Zhang, Z., Shi, J., Chen, R., Huang, R., and
Zhang, C. (2008). A multivariate method for surface
roughness vision inspection in different ambient light.
In 2008 IEEE International Conference on Mecha-
tronics and Automation, pages 324–328.
Firestone, L., Cook, K., Culp, K., Talsania, N., and Jr., K. P.
(1991). Comparison of autofocus methods for auto-
mated microscopy.
Geusebroek, J.-M., Cornelissen, F., Smeulders, A. W.,
and Geerts, H. (2000). Robust autofocusing in mi-
croscopy. Cytometry: The Journal of the International
Society for Analytical Cytology, 39(1):1–9.
Haralick, R. M., Shanmugam, K., and Dinstein, I. (1973).
Textural Features for Image Classification. IEEE
Transactions on Systems, Man, and Cybernetics,
SMC-3(6):610–621.
Helmli, F. S. and Scherer, S. (2001). Adaptive shape from
focus with an error estimation in light microscopy. In
ISPA 2001. Proceedings of the 2nd International Sym-
posium on Image and Signal Processing and Analysis.
In conjunction with 23rd International Conference on
Information Technology Interfaces (IEEE Cat., pages
188–193.
Krotkov, E. and Martin, J.-P. (1986). Range from focus.
In Robotics and Automation. Proceedings. 1986 IEEE
International Conference on, volume 3, pages 1093–
1098. IEEE.
Lee, S.-Y., Yoo, J.-T., Kumar, Y., and Kim, S.-W. (2009).
Reduced energy-ratio measure for robust autofocus-
ing in digital camera. IEEE Signal Processing Letters,
16(2):133–136.
Liu, L., Zhao, L., Long, Y., Kuang, G., and Fieguth, P.
(2012). Extended local binary patterns for texture
classification. Image Vision Comput., 30(2):86–99.
Lu, C. (2008). Study on prediction of surface quality in
machining process. Journal of Materials Processing
Technology, 205(1):439 – 450.
M. Eskicioglu, A. and S. Fisher, P. (1996). Image quality
measures and their performance. 43:2959 – 2965.
Minhas, R., Mohammed, A. A., Wu, Q. J., and Sid-Ahmed,
M. A. (2009a). 3d shape from focus and depth map
computation using steerable filters. In International
Conference Image Analysis and Recognition, pages
573–583. Springer.
Minhas, R., Mohammed, A. A., Wu, Q. M. J., and Sid-
Ahmed, M. A. (2009b). 3d shape from focus and
depth map computation using steerable filters. In
Kamel, M. and Campilho, A., editors, Image Analysis
and Recognition, pages 573–583, Berlin, Heidelberg.
Springer Berlin Heidelberg.
Nanda, H. and Cutler, R. (2001). Practical calibrations for a
real-time digital omnidirectional camera. CVPR Tech-
nical Sketch, 20:2.
Nayar, S. K., Watanabe, M., and Noguchi, M. (1996). Real-
time focus range sensor. IEEE Transactions on Pat-
tern Analysis and Machine Intelligence, 18(12):1186–
1198.
Pech-Pacheco, J. L., Crist
´
obal, G., Chamorro-Martinez, J.,
and Fern
´
andez-Valdivia, J. (2000). Diatom autofocus-
ing in brightfield microscopy: a comparative study.
In Pattern Recognition, 2000. Proceedings. 15th In-
ternational Conference on, volume 3, pages 314–317.
IEEE.
Sabino, D. M. U., da Fontoura Costa, L., Gil Rizzatti,
E., and Antonio Zago, M. (2004). A texture ap-
proach to leukocyte recognition. Real-Time Imaging,
10(4):205–216.
Santos, A., Ortiz de Sol
´
orzano, C., Vaquero, J. J., Pena, J.,
Malpica, N., and Del Pozo, F. (1997). Evaluation of
autofocus functions in molecular cytogenetic analysis.
Journal of microscopy, 188(3):264–272.
Shen, C.-H. and Chen, H. H. (2006). Robust focus mea-
sure for low-contrast images. In Consumer Electron-
ics, 2006. ICCE’06. 2006 Digest of Technical Papers.
International Conference on, pages 69–70. IEEE.
Shirvaikar, M. V. (2004). An optimal measure for camera
focus and exposure. In System Theory, 2004. Proceed-
ings of the Thirty-Sixth Southeastern Symposium on,
pages 472–475. IEEE.
Stout, K., Sullivan, P., Dong, W., Mainsah, E., Luo, N.,
Mathia, T., and Zahouani, H. (1994). Development of
Methods for Characterisation of Roughness in Three
Dimensions. Publication No. EUR 15178 EN of the
Commission of the European Communities, Luxem-
bourg.
Subbarao, M., Choi, T.-S., and Nikzad, A. (1992). Focusing
techniques. In Machine Vision Applications, Architec-
tures, and Systems Integration, volume 1823, pages
163–175. International Society for Optics and Photon-
ics.
Thelen, A., Frey, S., Hirsch, S., and Hering, P.
(2009). Improvements in shape-from-focus for holo-
graphic reconstructions with regard to focus operators,
neighborhood-size, and height value interpolation.
IEEE Transactions on Image Processing, 18(1):151–
157.
Torabi, M., Ardekani, R., and Fatemizadeh, E. (2007). Dis-
crimination between alzheimer’s disease and control
group in mr-images based on texture analysis using
artificial neural network.
Estimation of Correlation between Texture Features and Surface Parameters for Milled Metal Parts
427