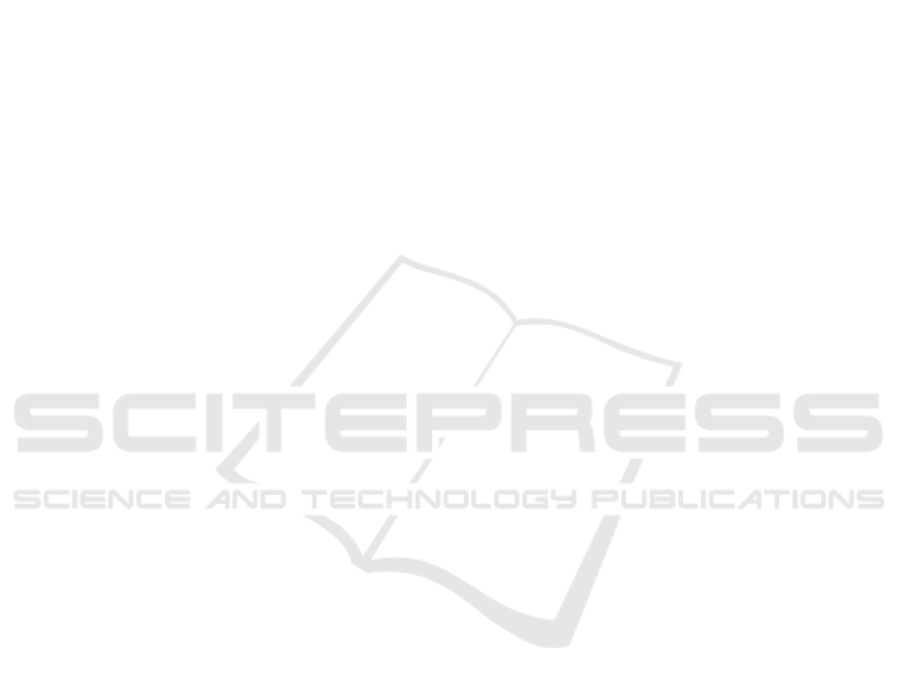
Two-dimensional Laser Scanner with Low Mechanical Cross
Coupling based on Piezoelectric Actuators
Chen Wei
1
, Luo Dong
2
, Liang Yuanbo
3
, Liu Peng
1
, Chen Liangpei
1
and Zhang Yizhou
1
1
Shenzhen Institutes of Advanced Technology, Chinese Academy of Sciences, 1068 Xueyuan Avenue, Shenzhen, China
2
Wuhan National Laboratory for Optoelectronics, Huazhong University of Science and Technology, Wuhan, China
3
School of Microelectronics, Xidian University, Xi’an, China
Keywords: Laser Scanner, Piezoelectric Actuators, Mechanical Cross Coupling, Hysteresis Compensation.
Abstract: Traditional two-dimensional laser scanners usually employ two-degree-of-freedom flexible hinges.
However, these flexible hinges suffer from mechanical cross coupling between axes, which will reduce the
scanning accuracy and stability. To overcome the above disadvantages, a compact novel laser scanner based
on piezoelectric actuators is presented. The scanner uses only three one-dimensional flexible hinges to
achieve two-axis feature. The mechanical structure and principle are detailed. Then the capabilities of the
scanner are tested by a performance test system. The test results show that the scanner has a tilt angle of
43.19 mrad for X-axis with resonance frequency at 149.21 Hz and 2.41 mrad for Y-axis with resonance
frequency at 232.59 Hz. Its scanning nonlinearity is reduced from 3% to 0.5% for X-axis and from 6% to
1% after compensation. The test results and the actual scanning images prove the low mechanical cross
coupling.
1 INTRODUCTION
Due to high precision, fast response, large force
output and low power-consumption, amplified
piezoelectric actuators (APAs) are widely applied in
biological engineering, nanofabrication, and robotics
and so on (Bouchilloux et al., 2004, Domke et al.,
2011, Park et al., 2012, Yang et al., 2010).
Especially for laser scanners which can precisely
control the directions of laser beams, APAs are one
of the main driving methods (Sweeney et al., 2002).
In addition to APAs, flexible hinges are also the key
structure for laser scanner. They can withstands
stress and offers deformation when the scanner
works.
Generally, to achieve two-dimensional (2-D)
adjustments of laser beams, two-degree-of-freedom
(2-DoF) flexible hinges have to be used.
Unfortunately, almost all 2-DoF flexible hinges
suffer from mechanical cross coupling between axes.
In other words, motion of one axis can be affected
by the other one, which will significantly reduce the
accuracy and stability of laser scanner (Chen et al.,
2015b, Jing et al., 2015, Shao et al., 2018). Some
scanners employ two 1-D laser scanners to obtain
2-D features (Chen et al., 2015a). However, these
designs increase system complexity and volume.
There are two methods to deal with cross coupling
effect. One is to use decoupling control algorithm,
which is generally difficult to design and implement.
The other one is to reduce the mechanical coupling
ratio. Therefore, a novel structure with small or even
zero interference between axes is strongly demanded.
In this paper, a new two-dimensional laser
scanner based on three APAs is proposed. Through
special mechanical design, the scanner employs only
three 1-DoF flexible hinges to achieve two-
dimensional laser deflection, which can effectively
reduce the cross coupling. The structure and
principle of the scanner are detailed. To investigate
its performance, a test system is built up based on
position sensitive detector (PSD). The test results
show that the scanner has different resonant
frequency in the two axes. The scanning images also
prove the low mechanical cross coupling.
2 STRUCTURE AND PRINCIPLE
Flexible hinges are widely used in precision
positioning. Various geometries of flexible hinges
have been reported and studied (Wu et al., 2018).
Wei, C., Dong, L., Yuanbo, L., Peng, L., Liangpei, C. and Yizhou, Z.
Two-dimensional Laser Scanner with Low Mechanical Cross Coupling based on Piezoelectric Actuators.
DOI: 10.5220/0007360301290133
In Proceedings of the 7th International Conference on Photonics, Optics and Laser Technology (PHOTOPTICS 2019), pages 129-133
ISBN: 978-989-758-364-3
Copyright
c
2019 by SCITEPRESS – Science and Technology Publications, Lda. All rights reserved
129