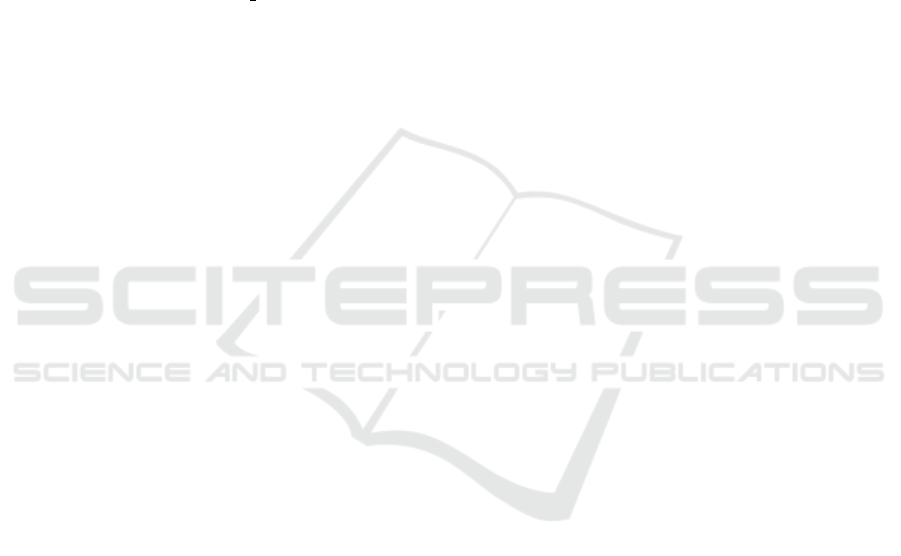
to be determined by the pair of machines where the
two consecutive setups are performed, which yields a
setup times matrix of size only O(m
2
), it could bring
the problem closer to real-life applications.
ACKNOWLEDGEMENTS
This work was supported by the Technology Agency
of the Czech Republic under the National Compe-
tence Center - Cybernetics and Artificial Intelligence
TN01000024, by the EU and the Ministry of Indus-
try and Trade of the Czech Republic under the Project
OP PIK CZ.01.1.02/0.0/0.0/15 019/0004688, and by
SVV project number 260 453.
REFERENCES
Allahverdi, A., Ng, C., Cheng, T. E., and Kovalyov, M. Y.
(2008). A survey of scheduling problems with setup
times or costs. European journal of operational re-
search, 187(3):985–1032.
Applegate, D. and Cook, W. (1991). A computational study
of the job-shop scheduling problem. ORSA Journal
on computing, 3(2):149–156.
Applegate, D. L., Bixby, R. E., Chv
´
atal, V., and Cook, W. J.
(2011). The Traveling Salesman Problem: A Compu-
tational Study. Princeton University Press.
Balas, E. (1968). Project scheduling with resource con-
straints. Technical report, Carnegie-Mellon Univ
Pittsburgh Pa Management Sciences Research Group.
Chen, D., Luh, P. B., Thakur, L. S., and Moreno Jr, J.
(2003). Optimization-based manufacturing schedul-
ing with multiple resources, setup requirements, and
transfer lots. IIE Transactions, 35(10):973–985.
Gurobi (2018). Constraints. http://www.gurobi.com/docu-
mentation/8.0/refman/constraints.html. Accessed
September 18, 2018.
Hentenryck, P. V. and Michel, L. (2009). Constraint-based
local search. The MIT press.
Laborie, P., Rogerie, J., Shaw, P., and Vil
´
ım, P. (2009). Rea-
soning with conditional time-intervals. part ii: An al-
gebraical model for resources. In FLAIRS conference,
pages 201–206.
Laborie, P., Rogerie, J., Shaw, P., and Vil
´
ım, P. (2018).
IBM ILOG CP optimizer for scheduling. Constraints,
23(2):210–250.
Lasserre, J. B. and Queyranne, M. (1992). Generic schedul-
ing polyhedra and a new mixed-integer formulation
for single-machine scheduling. Proceedings of the
2nd IPCO (Integer Programming and Combinatorial
Optimization) conference, pages 136–149.
Lee, Y. H. and Pinedo, M. (1997). Scheduling jobs
on parallel machines with sequence-dependent setup
times. European Journal of Operational Research,
100(3):464–474.
Pferschy, U. and Stan
ˇ
ek, R. (2017). Generating subtour
elimination constraints for the TSP from pure integer
solutions. Central European Journal of Operations
Research, 25(1):231–260.
Pisinger, D. and Ropke, S. (2010). Large neighborhood
search. In Handbook of metaheuristics, pages 399–
419. Springer.
Ruiz, R. and Andr
´
es-Romano, C. (2011). Scheduling
unrelated parallel machines with resource-assignable
sequence-dependent setup times. The International
Journal of Advanced Manufacturing Technology,
57(5-8):777–794.
Tempelmeier, H. and Buschk
¨
uhl, L. (2008). Dynamic multi-
machine lotsizing and sequencing with simultaneous
scheduling of a common setup resource. International
Journal of Production Economics, 113(1):401–412.
Vallada, E. and Ruiz, R. (2011). A genetic algorithm for the
unrelated parallel machine scheduling problem with
sequence dependent setup times. European Journal of
Operational Research, 211(3):612–622.
Vil
´
ım, P., Bart
´
ak, R., and
ˇ
Cepek, O. (2005). Extension
of O(n log n) filtering algorithms for the unary re-
source constraint to optional activities. Constraints,
10(4):403–425.
Zhao, X., Luh, P. B., and Wang, J. (1999). Surrogate gradi-
ent algorithm for lagrangian relaxation. Journal of op-
timization Theory and Applications, 100(3):699–712.
Makespan Minimization with Sequence-dependent Non-overlapping Setups
101