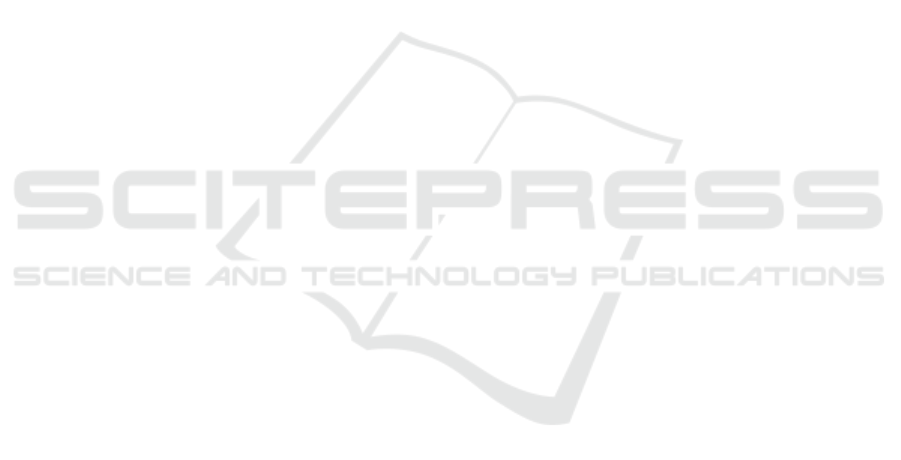
time in this work are acceptable by the typical store
manager, the abstract model created for simulation
still does not yet reflect the entire complexity of the
shop production dynamics. Further work will be un-
dertaken to improve the current model to enable even
better decision support. One aspect to be considered
is the inclusion of the food preparation process and
defrosting times, rather than just focusing on deter-
mining replenishment times and quantity. Also, an in-
depth study comparing the PSO to other optimisation
methods could also be an interesting future research
direction.
ACKNOWLEDGEMENTS
This research was supported by and PXtech Limited
and Innovate UK.
REFERENCES
Arisha, A. and Abo-Hamad, W. (2010). Simulation optimi-
sation methods in supply chain applications: a review.
Bakker, M., Riezebos, J., and Teunter, R. H. (2012). Re-
view of inventory systems with deterioration since
2001. European Journal of Operational Research,
221(2):275–284.
Bushuev, M. A., Guiffrida, A., Jaber, M., and Khan, M.
(2015). A review of inventory lot sizing review papers.
Management Research Review, 38(3):283–298.
De Meyer, A., Cattrysse, D., Rasinm
¨
aki, J., and Van Or-
shoven, J. (2014). Methods to optimise the design and
management of biomass-for-bioenergy supply chains:
A review. Renewable and sustainable energy reviews,
31:657–670.
Duong, L. N. K. and Wood, L. C. (2018). Discrete event
simulation in inventory management. In Encyclopedia
of Information Science and Technology, Fourth Edi-
tion, pages 5335–5344. IGI Global.
Ferguson, M., Jayaraman, V., and Souza, G. C. (2007).
Note: An application of the eoq model with nonlin-
ear holding cost to inventory management of perish-
ables. European Journal of Operational Research,
180(1):485–490.
Kennedy, R. (1995). J. and eberhart, particle swarm opti-
mization. In Proceedings of IEEE International Con-
ference on Neural Networks IV, pages, volume 1000.
Laskari, E. C., Parsopoulos, K. E., and Vrahatis, M. N.
(2002). Particle swarm optimization for integer pro-
gramming. In Evolutionary Computation, 2002.
CEC’02. Proceedings of the 2002 Congress on, vol-
ume 2, pages 1582–1587. IEEE.
L
´
opez-Ib
´
anez, M., Dubois-Lacoste, J., St
¨
utzle, T., and
Birattari, M. (2011). The irace package, iterated
race for automatic algorithm configuration. Tech-
nical report, Technical Report TR/IRIDIA/2011-004,
IRIDIA, Universit
´
e Libre de Bruxelles, Belgium.
Makui, A., Heydari, M., Aazami, A., and Dehghani, E.
(2016). Accelerating benders decomposition approach
for robust aggregate production planning of products
with a very limited expiration date. Computers & In-
dustrial Engineering, 100:34–51.
Park, K. and Kyung, G. (2014). Optimization of total in-
ventory cost and order fill rate in a supply chain using
pso. The International Journal of Advanced Manufac-
turing Technology, 70(9-12):1533–1541.
Ramezanian, R., Rahmani, D., and Barzinpour, F. (2012).
An aggregate production planning model for two
phase production systems: Solving with genetic algo-
rithm and tabu search. Expert Systems with Applica-
tions, 39(1):1256–1263.
Rini, D. P., Shamsuddin, S. M., and Yuhaniz, S. S. (2011).
Particle swarm optimization: technique, system and
challenges. International journal of computer appli-
cations, 14(1):19–26.
Shi, Y. and Eberhart, R. (1998). A modified particle swarm
optimizer. In Evolutionary Computation Proceedings,
1998. IEEE World Congress on Computational Intel-
ligence., The 1998 IEEE International Conference on,
pages 69–73. IEEE.
Soto-Silva, W. E., Nadal-Roig, E., Gonz
´
alez-Araya, M. C.,
and Pla-Aragones, L. M. (2016). Operational research
models applied to the fresh fruit supply chain. Euro-
pean Journal of Operational Research, 251(2):345–
355.
Tsai, C.-Y. and Yeh, S.-W. (2008). A multiple objective par-
ticle swarm optimization approach for inventory clas-
sification. International journal of production Eco-
nomics, 114(2):656–666.
Vila-Parrish, A. R., Ivy, J. S., and King, R. E. (2008).
A simulation-based approach for inventory modeling
of perishable pharmaceuticals. In Simulation Con-
ference, 2008. WSC 2008. Winter, pages 1532–1538.
IEEE.
Xu, J., Zeng, Z., Han, B., and Lei, X. (2013). A dynamic
programming-based particle swarm optimization al-
gorithm for an inventory management problem under
uncertainty. Engineering Optimization, 45(7):851–
880.
Yu, Y., Wang, Z., and Liang, L. (2012). A vendor managed
inventory supply chain with deteriorating raw materi-
als and products. International Journal of Production
Economics, 136(2):266–274.
A Simulation-based Optimisation Approach for Inventory Management of Highly Perishable Food
413