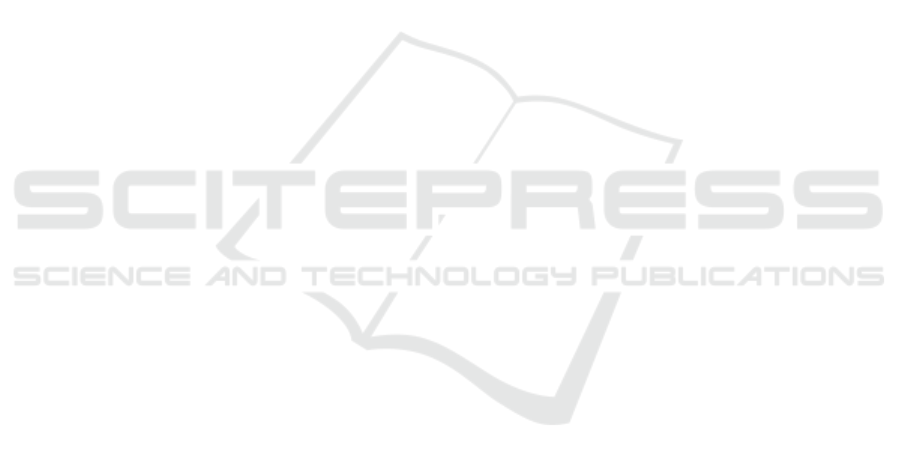
REFERENCES
Buecherl, D., Bertram, C., Thanheiser, A., and Herzog,
H.-G. (2010). Scalability as a degree of freedom in
electric drive train simulation. In 2010 IEEE Vehicle
Power and Propulsion Conference. IEEE.
Domingues, G., Reinap, A., and Alakula, M. (2016). De-
sign and cost optimization of electrified automotive
powertrain. In 2016 International Conference on
Electrical Systems for Aircraft, Railway, Ship Propul-
sion and Road Vehicles & International Transporta-
tion Electrification Conference (ESARS-ITEC). IEEE.
Drago, G. and Ridella, S. (1992). Statistically controlled ac-
tivation weight initialization (SCAWI). IEEE Trans-
actions on Neural Networks, 3(4):627–631.
Gao, W. and Porandla, S. (2005). Design optimization of
a parallel hybrid electric powertrain. In 2005 IEEE
Vehicle Power and Propulsion Conference. IEEE.
Hagan, M. and Menhaj, M. (1994). Training feedforward
networks with the marquardt algorithm. IEEE Trans-
actions on Neural Networks, 5(6):989–993.
Hofman, T., Ebbesen, S., and Guzzella, L. (2012). Topol-
ogy optimization for hybrid electric vehicles with au-
tomated transmissions. IEEE Transactions on Vehicu-
lar Technology, 61(6):2442–2451.
Hornik, K., Stinchcombe, M., and White, H. (1989). Multi-
layer feedforward networks are universal approxima-
tors. Neural Networks, 2(5):359–366.
Magee, L. (1990). R2measures based on wald and like-
lihood ratio joint significance tests. The American
Statistician, 44(3):250–253.
Marquardt, D. W. (1963). An algorithm for least-squares
estimation of nonlinear parameters. Journal of
the Society for Industrial and Applied Mathematics,
11(2):431–441.
Nelles, O. (2001). Nonlinear System Identification.
Springer Berlin Heidelberg.
Rumelhart, D. E., Hinton, G. E., and Williams, R. J. (1986).
Learning representations by back-propagating errors.
Nature, 323(6088):533–536.
Santner, T. J., Williams, B. J., and Notz, W. I. (2003).
The Design and Analysis of Computer Experiments.
Springer New York.
Silvas, E., Hofman, T., Murgovski, N., Etman, P., and Stein-
buch, M. (2016). Review of optimization strategies for
system-level design in hybrid electric vehicles. IEEE
Transactions on Vehicular Technology, pages 1–1.
Stipetic, S. and Goss, J. (2016). Calculation of efficiency
maps using scalable saturated flux-linkage and loss
model of a synchronous motor. In 2016 XXII Inter-
national Conference on Electrical Machines (ICEM).
IEEE.
Vaillant, M. (2016). Design Space Exploration zur
multikriteriellen Optimierung elektrischer Sport-
wagenantriebsstr
¨
ange: Variation von Topologie
und Komponenteneigenschaften zur Steigerung von
Fahrleistungen und Tank-to-Wheel Wirkungsgrad.
PhD thesis, KIT Karlsruhe.
Winsel, T. (2002). Stabile neuronale Prozessmodelle - au-
tomatisierte Generierung echtzeitfhiger Modelle zur
Nachbildung des dynamischen Verhaltens von Ver-
brennungsmotoren. VDI-Verlag, Dsseldorf.
Wirasingha, S. G. and Emadi, A. (2011). Classification and
review of control strategies for plug-in hybrid electric
vehicles. IEEE Transactions on Vehicular Technology,
60(1):111–122.
Zhou, K., Ivanco, A., Filipi, Z., and Hofmann, H. (2015).
Finite-element-based computationally efficient scal-
able electric machine model suitable for electrified
powertrain simulation and optimization. IEEE Trans-
actions on Industry Applications, 51(6):4435–4445.
VEHITS 2019 - 5th International Conference on Vehicle Technology and Intelligent Transport Systems
24