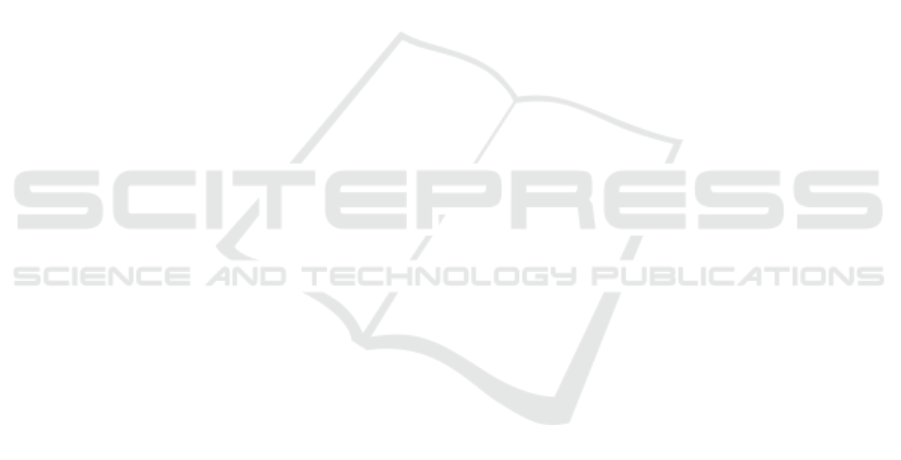
with the comparison of different modeling
approaches for the simulation of control loop
components and control systems in system
simulation environments. The aim was to use the
example of a valve-controlled hydraulic bearing
preload element to investigate how the degree of
model detailing affects the controller design of the
considered force control and how the simulation
performance can be increased by different modeling
approaches and model simplifications. Therefor the
simulation environment SimulationX® was used.
Controlling element of the investigated control
system is a 4/3-way control valve. Different
modeling approaches for control valves were
examined and compared. It was found that by
implementing the experimentally determined 3D
flow-maps of the individual control edges into the
model, the static transmission behavior of the
control valve can be mapped very accurately.
Simulation errors less than 5% could be achieved.
The second valve model based on the flow-load
function and parameterized with the manufacturer's
specifications for nominal pressure and nominal
volume flow showed only slight deviations from the
measured data in a wide range of values. Simulation
errors less than 10% could be achieved.
Disadvantage of these two models is that they are
only applicable to a specific temperature and
viscosity of the hydraulic oil. The third control valve
model was provided from the model library of
SimulationX®. This model shows the lowest
accuracy regarding the static transmission behavior
compared to the map-based model and the flow-load
model. One big advantage of the SimulationX®-
model is that the use of empirical equations takes
into account the oil viscosity in the description of the
flow behavior. The PT2 element on which all three
models are based shows a realistic dynamic
transmission behavior. This could be shown by
comparisons of simulated and experimentally
determined frequency and step responses of the
control valve.
For the simulative mapping of the overall control
system, two modeling approaches have been
compared, a detailed physical model and a
simplified signal flow model. The detailed physical
model shows very realistic simulation results
regarding the investigated behavior of the control
loop. It was found that by certain reparameteri-
zations of the signal flow model its simulation
accuracy can be significantly increased, for example
by reparameterization of the control edge overlaps of
the control valve model. Overall, a good agreement
of the static and dynamic control loop behavior with
the measured data can be achieved with both
models. With regard to the needed simulation time
the simplified signal flow model is clearly superior
to the detail model. The calculation time can be
reduced by at least 75 % by using the signal flow
model. The higher simulation performance of the
signal flow model is particularly evident when using
a parameter optimization function to optimize
controller parameters. The higher performance of the
signal model is even more important if extended
control structures are to be designed by means of
optimization functions, since a larger number of
parameters to be optimized is obtained here. Another
disadvantage of the detail model is the significantly
greater effort in the model parameterization.
REFERENCES
Backhaus, S.-G., 2008. Eine Messstrategie zur
Bestimmung des dynamischen Übertragungsverhaltens
von Wälzlagern. Göttingen: Cuvillier Verlag
Göttingen.
Harris, T., 2001. Rolling Bearing Analysis. s.l.:John Wiley
& Sons.
Hatami, H., 2013. Hydraulische Formelsammlung.
s.l.:Bosch Rexroth Group.
Ivanov, G., 2018. Detailed modeling of a hydraulic
bearing preload element for drive design and control
development. Dresden, s.n.
Lohse, H., 2015. Modellierung hydraulischer
Tiefziehpressen für Prozesskopplung, Reglerauslegung
und energetische Bilanzierung. Aachen: Shaker
Verlag.
Töpfer, H., Schwarz, A., 1988. Wissensspeicher
Fluidtechnik. Leipzig: VEB Fachbuchverlag.
Weber, J., 2011. Aufbau und Übertragungsverhalten von
Stetgiventilen. Studienskript. Dresden: TU Dresden.
Weber, J., 2011. Übertragungseigenschaften des
ventilgesteuerten Zylinderantriebes. Dresden: TU
Dresden.
SIMULTECH 2019 - 9th International Conference on Simulation and Modeling Methodologies, Technologies and Applications
196