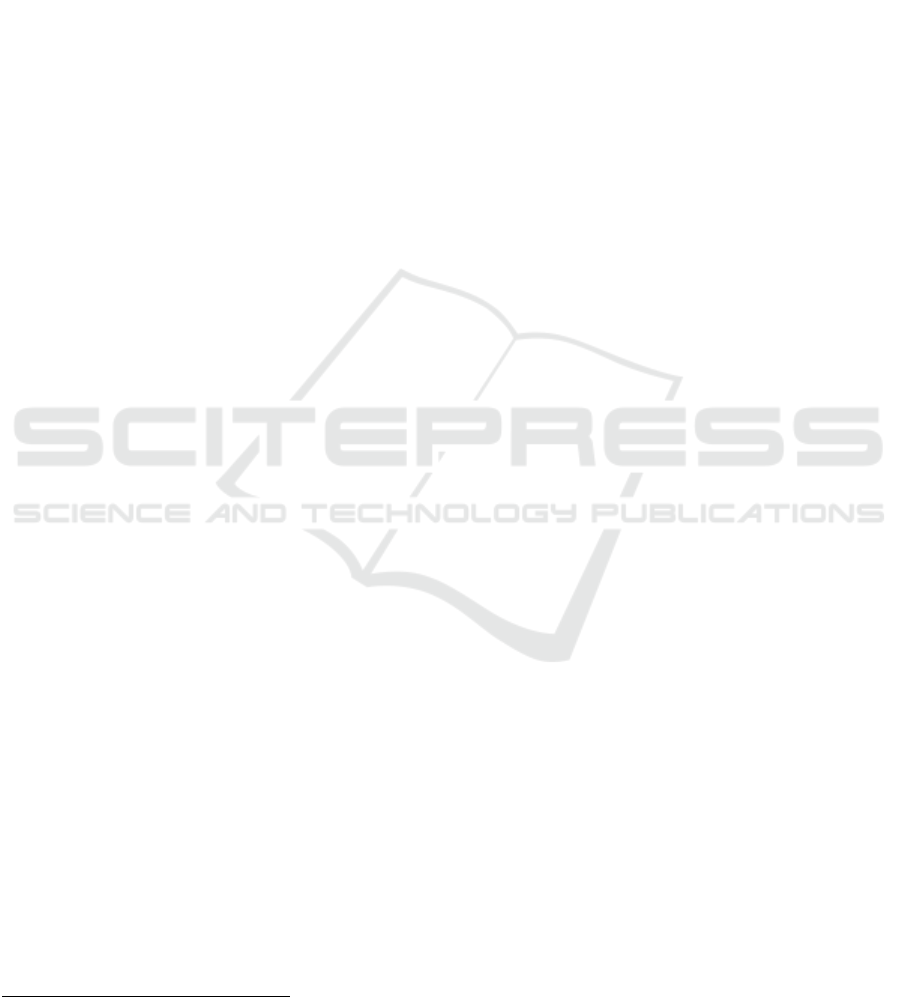
Turbulent Flow Modelling of a Jet in a Cross-Flow Stream:
Model and App
M. Tabatabaian
Department of Mechanical Engineering, British Columbia Institute of Technology, School of Energy,
3700 Willingdon Ave., Burnaby, BC, Canada
Keywords: Turbulent Flow, Jet Flow, Cross Flow, CFD, , Education-Aid App, COMSOL
®
.
Abstract: The flow of a jet stream entering a cross flow main stream is modelled along with introducing the related App.
The turbulent flow details are computed and validated against similar computational and experimental results.
For example, dimensionless streamwise and cross-streamwise velocity components, dimensionless turbulent
kinetic energy, and dissipation are shown in colour-expression figures, along with streamlines near the jet
entrance to the main stream flow. The results agree with those from the existing references. We used a custom
designed structured mesh for all models. Also, for democratization of the model applications a COMSOL®
model-based App is built and introduced
a
.
1 INTRODUCTION
The topic of turbulent flow modelling of a crossflow
jet is of interest, both for understanding of the flow
detail and industrial applications. This type of flow
occurs in many industrial and natural applications.
For instance, during landing and take-off of airplanes,
gas turbines, fuel injections, oil refinery piping, waste
discharge into reservoirs or atmosphere. In any of
these flow types turbulence occurs and enhances
mixing or, in general, the exchange of mass and
energy between the jet and the mainstream flows.
With the advances of computational fluid dynamics
(CFD) and practical availability of commercial CFD
software tools more industries are using models of
turbulent flows in their design process. COMSOL
®
is
a Multiphysics software package including CFD
facilities and tools for building license-independent
App’s. In this paper we model the flow of a jet stream
which is injected into another main stream flow, using
COMSOL. Among the volume of research work
performed on this topic, we selected the work of
Karvinen & Ahlstedt (Rodi, 2005) who modelled the
experimental work of Özcan & Larsen (Report MEK-
FM, 2001-02), done for a similar setting. Former
authors used several turbulence models (i.e., k-ε,
a
Materials in this article and the model/App are used with
permission from Mercury Learning and Information, ©
2015 and 2017. All rights reserved.
versions of k-ω, versions of low-Re k-ε, and Reynolds
stress) for the purpose of comparison and validation
with those experimental results of the latter. Their
main conclusion was that the k-ε model results
matched the experimental results better. We use the
above-mentioned references for validation of our
modelling results, using the model with a
custom-designed structured mesh, after performing
mesh sensitivity analysis. The model run on a
workstation laptop with 16GB RAM, and a 2-core
CPU. Step-by-step instructions for building the
model is given in (Tabatabaian, 2015).
2 FLOW DOMAIN GEOMETRY
AND DATA
The flow domain consists of a main 2D channel and
a perpendicular jet tube. The main channel and jet
flow domains are schematically shown in Figure 1
below, with having the symmetry line in the middle
of the main stream channel. The centre of coordinate
system is located at the centre-line of the jet pipe with
the axis located at the bottom of the main
stream channel. The main stream cross-flow enters
Tabatabaian, M.
Turbulent Flow Modelling of a Jet in a Cross-Flow Stream: Model and App.
DOI: 10.5220/0007718701970201
In Proceedings of the 9th International Conference on Simulation and Modeling Methodologies, Technologies and Applications (SIMULTECH 2019), pages 197-201
ISBN: 978-989-758-381-0
Copyright
c
2019 by SCITEPRESS – Science and Technology Publications, Lda. All rights reserved
197