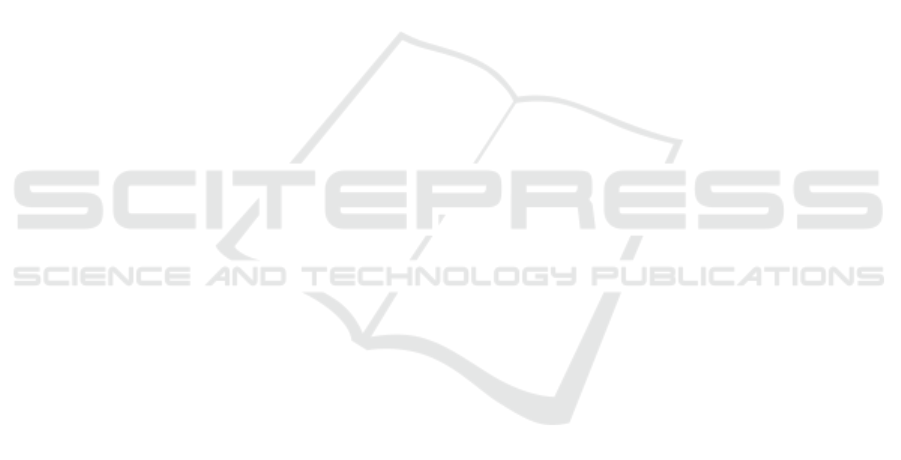
sents a product at a time. Each container/processing-
unit that individually stores/processes a product, at
a certain time, is modeled as a node in a graph
(Dabbene and Gay, 2011).
Palma-Mendoza and Neailey proposed an ap-
proach to integrate the business processes of the en-
tities involved in a supply chain. The main aim is
to guide the business process redesign to support e-
business, thus focusing supply chain B2B integration
and not a value chain oriented organizational collabo-
ration (Palma-Mendoza and Neailey, 2015).
Bevilacqua et al. propose a business process
reengineering for a supply chain of vegetable prod-
ucts (fresh vegetables, canned vegetables, mixed veg-
etables, cooked and pre-cooked vegetables) (Bevilac-
qua et al., 2009). They also suggest software system
design models for managing product traceability. The
authors present a framework based on EPCs (event-
driven process chains) and use ARIS tool to create a
Web interface to provide information to the final con-
sumer (Bevilacqua et al., 2009).
Meroni et al. propose an approach to integrate
and coordinate multi-party business processes and
present a prototype to demonstrate the proposed ap-
proach (Meroni et al., 2018). The paper presents a
methodology to translate BPMN processes to E-GSM
(Extended-Guard-Stage-Milestone) notation.
All the mentioned approaches propose specific so-
lutions for specific problems, and only a few present
specific business process or domain models. Here, a
pattern solution is proposed for any food value chain
traceability problem, namely a pattern business pro-
cess model and the associated pattern domain model.
3 MODELING THE INTEGRATED
BUSINESS PROCESS
This section presents the creation of the integrated
business process model for traceability and quality
monitoring of food products.
After having visited several producers, small
farmers’ associations, food processing industries, dis-
tributors, and supermarkets, and having participated
in the identification and design of several food chain
operators’ product traceability processes, of which
two are presented here, the similarity of different food
value chains, in terms of activities needed to address
traceability and quality monitoring, became apparent.
The approach consisted in eliciting and analyzing
a set of productive business process models from dif-
ferent food value chains’ operators (milk and dairy,
fruit, fisheries, vegetables), understand their occur-
ring order in the chain and integrate them, to obtain
a pattern business process model for traceability and
quality monitoring in food value chains.
To model business processes we are using BPMN
(Business Process Model and Notation), which is the
main standard process modeling language and one of
the most used for that purpose (Cruz et al., 2014).
Created by OMG for providing a notation clear to all
stakeholders involved in Business Process Manage-
ment (BPM), BPMN is easy to understand and usable
by people with different roles and training from top
managers to IT professionals (OMG, 2011), and is ac-
tually used both in academia and in organizations.
Business Process (BP) model diagrams define a
set of business activities carried out by an organiza-
tion for the attainment of a goal (product or service).
This type of model describes a BP internal to a spe-
cific organization(OMG, 2011). Yet, in this paper, we
do not use BPMN in the “usual” form. In fact, the
BPMN business process model is being used as a sim-
ple and easy way to understand and identify all the
activities that affect a product lot (or batch). So, in
this paper, the main lane (in the main pool) does not
represent nor a company neither a business partner.
Instead, it represents a product lot. So, business pro-
cesses are used here to focus our attention in the ac-
tivities that involve, or affect, a products lot and about
which a traceability platform needs to receive and
store information. External participants, in the mod-
els, represent the value chain operators responsible for
providing information about the activity with which
they are exchanging messages. These messages rep-
resent the information that a participant needs to pro-
vide. The activities are, in fact, executed by the par-
ticipants, represented as external participants sending
messages to the corresponding value chain activity.
The traceability platform’s main goal is to gather
and store all the relevant information from value chain
activities, to be able to identify: what was done; who
did it; when it was done; where it was done; under
what conditions it was executed. Thus, all operators
involved in the value chain must be identified.
For this presentation, and due to space limitations,
we have selected two different flows of activities in
food value chains. The next subsections present two
value chain business process models, respectivelly
about fresh vegetables, in subsection 3.1, and freeze-
dried apples, in subsection 3.2. Finally, subsection 3.3
presents a process model integrating all food value
chain’s activities, not just from the two cases pre-
sented, but also from case studies from other food
value chains (e.g. fishery, meat, aquaculture, dairy).
A Food Value Chain Integrated Business Process and Domain Models for Product Traceability and Quality Monitoring: Pattern Models for
Food Traceability Platforms
287