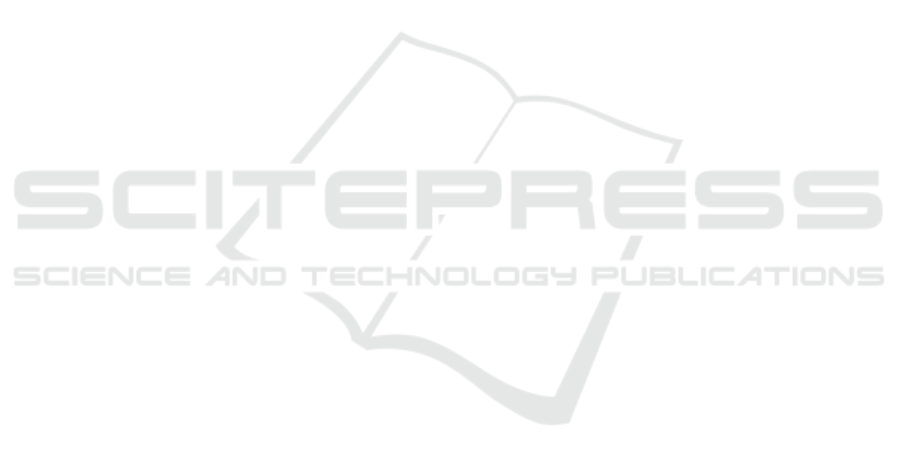
use the research results to develop marketable prod-
ucts.
7 CONCLUSION
In this paper, the OPeRAte-project was presented in
its current stage and in terms of its long-term goal.
The result is a framework for platform-independent,
cross-vendor execution of joined, distributed agricul-
tural tasks.
At present, there is a BPMN-based three-layer
process management which is responsible for creat-
ing, controlling and monitoring task collaboration. As
a reference task serves liquid slurry spreading.
Special hardware in the form of a tank trailer was
manufactured by cooperation partners and success-
fully put to the test in some initial runs. The con-
nection of all machines, devices and sensors to the In-
ternet and the contiuous flow of information between
them creates a central system for the coordination
of multiple task chains. End users, such as farmers
and contractors, benefit from dynamic resource opti-
mization and automated generation of legally required
documentation of tasks performed. At the same time,
complex, internal process structures remain hidden
from the user and are instead abstracted in an under-
standable way by logically structured, graphical user
interfaces.
During development, care was taken to keep the
software architecture as generic as possible so that
modules can be reused and ports to other manufac-
turer models and scenarios remain possible.
The project will continue until the beginning of
2020. Until then, the currently available processes
and implementations will be refined so that at the end
of the project the basis for a product not yet avail-
able in this form exists. OPeRAte has the potential to
sustainably improve agriculture hopefully not only in
Germany through the intelligent application of mod-
ern technologies.
ACKNOWLEDGEMENTS
The project is supported by funds of the Federal Min-
istry of Food and Agriculture (BMEL) based on a de-
cision of the Parliament of the Federal Republic of
Germany via the Federal Office for Agriculture and
Food (BLE) under the innovation support programme.
REFERENCES
AEF (2019). ISOBUS - AEF Online. URL:
https://www.aef-online.org/de/die-aef/isobus.html,
accessed: 24.01.19.
Agrawal, H., Prieto, J., Ramos, C., and Corchado, J. M.
(2016). Smart feeding in farming through IoT in si-
los. In Corchado Rodriguez, J. M., Mitra, S., Thampi,
S. M., and El-Alfy, E.-S., editors, Intelligent Sys-
tems Technologies and Applications 2016, Advances
in Intelligent Systems and Computing, pages 355–
366. Springer International Publishing.
BMEL (2017). D
¨
ungeverordnung. URL: https://
www.bmel.de/DE/Landwirtschaft/Pflanzenbau/
Ackerbau/Texte/Duengung.html, accessed: 28.01.19.
Cavoukian, A. (2009). Privacy by design: The 7
foundation principles. Information and Privacy
Commissioner Ontario, Canada http://www. ipc.
on. ca/images/Resources/7foundationalprinciples. pdf
P
´
agina vigente al, 22.
DBV (2018). Situationsbericht 2018/19. page 16. URL:
https://de.statista.com/statistik/daten/studie/658759/
umfrage/wirtschaftskennzahlen-der-landwirtschaft-
in-deutschland/, accessed: 28.01.19.
DFKI (2017). SDSD - Smarte Daten, Smarte Dien-
ste. Landwirtschaftliche Datendrehscheibe f
¨
ur
effiziente ressourcenschonende Prozesse. URL:
https://www.dfki.de/web/forschung/projekte-
publikationen/projekte/projekt/sdsd/, accessed:
24.01.19.
Dierks, T. and Rescorla, E. (2008). The transport layer
security (tls) protocol version 1.2. Technical report.
URL: https://www.ietf.org/rfc/rfc5246.txt, accessed:
30.01.19.
Eclipse Foundation (2019). Eclipse Mosquitto. URL:
http://mosquitto.org/, accessed: 13.03.19.
ENISA (2014). Privacy and data protection by de-
sign – from policy to engineering. URL:
https://www.enisa.europa.eu/ publications/privacy-
and-data-protection-by-design, accessed: 25.01.19.
Ferguson, S. (2018). John Deere Bets the Farm on AI,
IoT. URL: https://www.lightreading.com/enterprise-
cloud/machine-learning-and-ai/john-deere-bets-the-
farm-on-ai-iot/a/d-id/741284, accessed: 30.01.19.
Freye, D. (2010). Agrarwirtschaft - KOMOBAR heißt
der neue Forschungsschwerpunkt der Hochschule.
(11):28 – 29.
HiveMQ (2019). HiveMQ. URL:
https://www.hivemq.com/, accessed: 13.03.19.
ISO (2017). ISO 11783-1:2017. URL: http://www.iso.org/
cms/render/live/en/sites/isoorg/contents/data/standard/
05/75/57556.html, accessed: 30.01.19.
Kamilaris, A., Gao, F., Prenafeta-Boldu, F. X., and Ali,
M. I. (2016). Agri-IoT: A semantic framework for In-
ternet of Things-enabled smart farming applications.
In 2016 IEEE 3rd World Forum on Internet of Things
(WF-IoT), pages 442–447.
Minwoo Ryu, Jaeseok Yun, Ting Miao, Il-Yeup Ahn, Sung-
Chan Choi, and Jaeho Kim (2015). Design and im-
plementation of a connected farm for smart farming
system. In 2015 IEEE SENSORS, pages 1–4, Busan.
IEEE.
OPeRAte: An IoT Approach towards Collaborative, Manufacturer-independent Farming 4.0
175