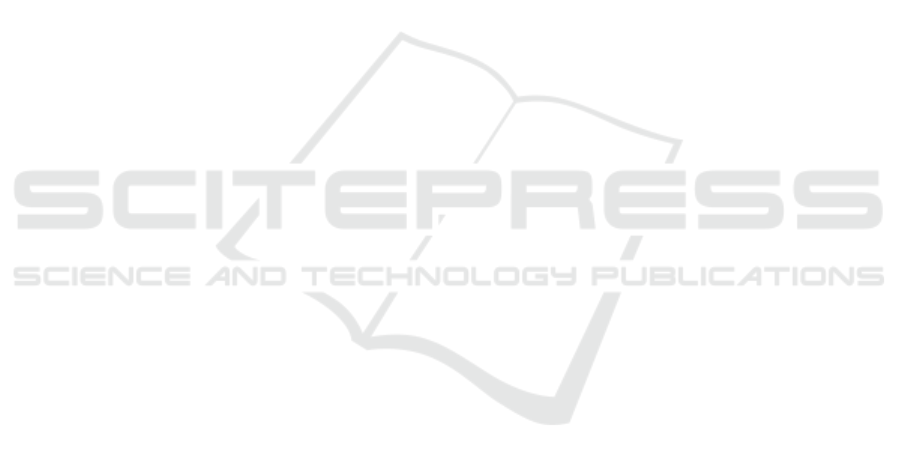
spiration to Implementation. A K Peters, Wellesley,
Massachusetts.
Lehrer, M., Srinivasan, M. V., Zhang, S. W., and Horridge,
G. A. (1988). Motion cues provide the bee’s visual
world with a third dimension. Nature, 332(24):356–
357.
Lundsgaard, S. K. and Grivas, N. J. (2006). Method and
apparatus for detecting vehicular collisions. United
States Patent US 7,119,669 B2.
Mane, A. and Rana, J. (2014). Vehicle collision recognition
and monitoring system based on AVR platform. Inter-
national Journal of Engineering Research and Gen-
eral Science, 2(6):540–545.
McKerrow, P. J. (1991). Introduction to Robotics. Addison-
Wesley Publishing Company, Sydney.
McMahan, W., Romano, J. M., and Kuchenbecker, K. J.
(2012). Using accelerometers to localize tactile con-
tact events on a robot arm. In Proceedings of the
Workshop on Advances in Tactile Sensing and Touch-
Based Human-Robot Interaction, ACM/IEEE Inter-
national Conference on Human-Robot Interaction,
Boston, MA. IEEE.
Moorits, E. and Usk, A. (2012). Buoy collision detection.
In Bo
ˇ
zek, J. and Grgi
´
c, M., editors, Proceedings EL-
MAR, 54th international Symposium, Zadar, Croatia.
IEEE.
Na, S. Y., Shin, D., Kim, J. Y., and Choi, S.-I. (2005). Col-
lision recognition and direction changes using fuzzy
logic for small scale fish robots by acceleration sensor
data. In International Conference on Fuzzy Systems
and Knowledge Discovery, pages 329–338, Berlin.
Springer-Verlag.
Nadarajan, K. and Sridharan, M. (2010). Online detection
of instability for robust teamwork in humanoid soccer
robots. In Proceedings of the 5th Workshop on Hu-
manoid Soccer Robots, Nashville,TN.
Santos-Victor, J., Sandini, G., Curotto, F., and Garibaldi, S.
(1993). Divergent stereo for robot navigation: Learn-
ing from bees. In Proceedings of Computer Vision and
Pattern Recognition, New York, pages 434–439.
Santos-Victor, J., Sandini, G., Curotto, F., and Garibaldi, S.
(1995). Divergent stereo in autonomous navigation:
From bees to robots. International Journal of Com-
puter Vision, 14:159–177.
Speleers, P. and Ebner, M. (2019). Acceleration based colli-
sion detection with a mobile robot. In McDermoot, J.,
Castelli, M., Sekanina, L., Haasdijk, E., and Garc
´
ıa-
S
´
anchez, P., editors, 3rd IEEE International Confer-
ence on Robotic Computing, IRC 2019, Nalpes, Italy,
February, pages 437–438, Los Alamitos, CA. IEEE.
Srinivasan, M. V. (1992a). Distance perception in insects.
Current Directions in Psychological Science, 1(1):22–
26.
Srinivasan, M. V. (1992b). How bees exploit optic flow: be-
havioural experiments and neural models. Phil. Trans.
R. Soc. Lond. B, 337:253–259.
The R Development Core Team (2008). R: A language and
environment for statistical computing. R Foundation
for Statistical Computing.
Thompson, C., White, J., Dougherty, B., Albright, A., and
Schmidt, D. C. (2010). Using smartphones and wire-
less mobile sensor networks to detect car accidents
and provide situational awareness to emergency re-
sponders. In Proceedings of the Third International
ICST Conference on MOBILe WirelessMiddleWARE,
Operating Systems, and Applications, Chicago, IL,
pages 29–42, Berlin. Springer.
Vail, D. and Veloso, M. (2004). Learning from accelerom-
eter data on a legged robot. IFAC Proceedings,
37(8):822–827.
Wisanuvej, P., Liu, J., Chen, C.-M., and Yang, G.-Z. (2014).
Blind collision detection and obstacle characterisation
using a compliant robotic arm. In IEEE International
Conference on Robotics and Automation, pages 2249–
2254.
Collision Detection for a Mobile Robot using Logistic Regression
173