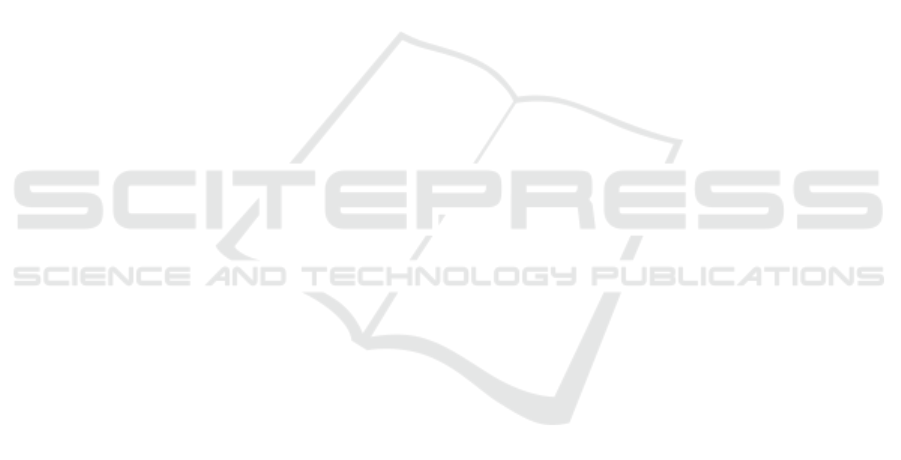
Fig. 1 presents a fragment of a fractal enterprise
model of the current business activity. In the root of
this model is a primary process of manufacturing and
delivering products. Underneath of it, there are
various assets that are needed for the process working
smart-free. Under smart-free, we mean that instances
of this process (production batches) are started with
normal frequency. As shown in FEM in Fig.1, the
process requires variety of assets such as workers on
the flour (Workforce), manufacturing equipment
(Technical and informational infrastructure) and
customers (Beneficiary). Note that the FEM fragment
in Fig.1 does not show all assets that are needed to
run the primary process, for example, a stock of
orders for producing product batches is not presented.
The choice of what to present in Fig. 1 has been made
based on the most important assets and assets that are
of interest for BMI to be considered in the paper.
After the assets of the first level (underneath the
primary process) are put in the model, the unfolding
of FEM continues by applying the asset-processes
archetype, which requires finding processes that
manage the identified assets. These processes are
connected with the asset(s) by three types of
relationships: Acquire, Maintain and Retire.
Dependent on the type of assets, the asset managing
processes have different nature. For a workforce type
of assets, they are hiring, training and retiring. For the
infrastructure type of assets, they are acquisition,
maintenance, and phasing out. For the execution
template (EXT) type of assets, they are
develop/design, maintain and phase out.
After the management processes are identified,
assets that are needed to run them are identified using
process-assets archetypes. For example, the customer
asset needs sales and marketing for both acquiring
new customers and keeping them attached to the
company, so that they continue to add orders to the
stock of orders. The equipment asset, e.g. machines
X, needs a service/maintenance process (see Fig. 1).
The process of unfolding of FEM can continue by
applying the asset-processes archetype for newly
identified assets. Thus, marketing and sales requires
well-defined value proposition and reputation that
backs it (see Fig. 1), as well as other assets (not
identified in the figure), like sales executives.
Machine X maintenance requires service technicians,
machine process experts, machine providers (partners
to provide spare parts, advice, etc.) and diagnostic
tools. As machine diagnostic and prediction is in the
focus of this work, we will look at this topic in more
details in the next sub-section.
3.2 Machine Maintenance
In a manufacturing organization, production
equipment - machines are very important resources
for production. Different Key Performance Indicators
(KPIs) related to manufacturing resources are used to
ensure the optimal usage of the machines, such as
OEE (Overall Equipment Efficiency) defined in ISO
standard (ISO, 2014a; ISO, 2014b). A stoppage in
production line due to machine failure costs a lot of
money for an organization.
In the context of Industry 4.0, maintenance is an
important area that has an enormous potential in
terms of cost saving and resource efficiency. There
are many use cases that come under the category
"maintenance 4.0", like automatic maintenance order
generation, notifications to stakeholders (users, other
machines and mobile devices), predictive
maintenance, flexible manufacturing, and support
services (augmented reality).
Normally, in an organization, maintenance is
counted as an overhead (however, a mandatory one)
on the production. In order to avoid unpredictable
costs, machines are serviced in regular intervals
(sometimes according to manufacturer
specifications). However, despite all regular services,
sometimes unplanned maintenance also has to be
carried out due to failure in machines or loss of
quality in operations carried out by the machines. If a
particular machine or its part is situated in a critical
position in the line, it has a drastic impact on the
whole production, as well as on the quality of
products delivered to the customers; thus a failure in
such an equipment affects the overall KPIs.
In a manufacturing organization, machines are
used as long as they fit for the purpose, no matter how
old they become. Several kinds of maintenance are
carried out to keep the production lines running.
These are briefly described below.
1. Planned Maintenance. The planned maintenance
is carried out according to a specific plan like after
completion of certain number of operating hours
(e.g. 20,000 hours), or after certain cycles (e.g.
2,000,000 cycles). It is carried out regularly to
avoid the unplanned (failure-based) maintenance
in order to save costs. However, this planned
maintenance is carried out sometime earlier than
completion of the operating hours in order to
avoid an extra stoppage in production when the
production line is stopped for a different reason
(like new software updates). However, an earlier
planned maintenance affects negatively the costs
of production for an organization, as shown in Fig.
2.
ICEIS 2019 - 21st International Conference on Enterprise Information Systems
528