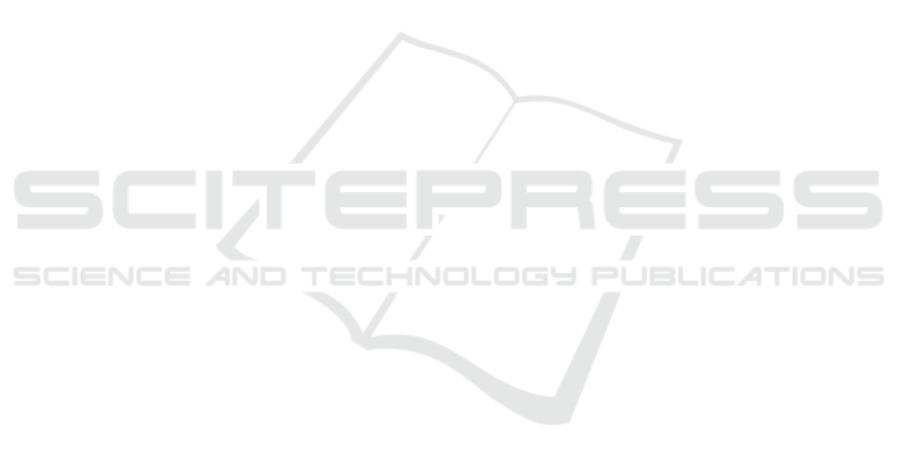
repairs. For this case, it is better to wait for more
maintenance data to validate if an improvement from
the mechanical system is visible and validate if the
stochastic process that defines the failures is then
a renewal process. Otherwise, it will be necessary
to consider modifying the maintenance policy by
implementing more preventive action in order to
follow up and repair the state of the system. However,
beyond the reality of imperfect maintenance, the
correlation between data can come from anomalies
may be related to insufficient data collection or other
situations not representative of the failure process.
5 CONCLUSION
In this study, the reliability and the probability density
from repairable mechanical system were evaluated.
The correlation test accepts the assumption of
dependency for failures data and thereby, they follow
a branching Poisson process. This process could
be modeled from the graph based on a logarithmic
scale and the equations defined in mathematical
formulation section. For practical purposes, the
estimated parameters of first order properties from
the modeling are sufficient to give an interpretation
of the branching process Poisson followed by the
failure data. Given the verification of the Branching
Poisson process model from the mechanical system,
the interest remains in the value of the failure rate λ
and the efficiency of the system repair E(S). Then,
the main utility of the branching Poisson process is
that it can be used to give a physical interpretation of
the deviation for the time between failures.
ACKNOWLEDGMENT
The authors are grateful to support of the Natural
Sciences and Engineering Research Council of
Canada (NSERC) and the Fonds de recherche du
Qu
´
ebec - Nature et technologies (FRQNT).
REFERENCES
Abramowitz, M. and Stegun, I. (1972). Handbook of
Mathematical Functions with Formulas, Graphs, and
Mathematical Tables. U.S. Government Printing
Office, Washington, D.C.
Ascher, H. and Feingold, H. (1984). Repairable System
Reliability: Modeling, Inference, Misconceptions and
Their Cause. Marcel Dekker, New York.
Barlow, R. E. and Hunter, L. (1960). Optimum preventive
maintenance policies. Operations research,
8(1):90–100.
Barlow, R. E. and Proschan, F. (1965). Mathematical
Theory of Reliability. Wiley, New York.
Cox, D. and Lewis, P. A. W. (1966). The Statistical Analysis
of Series of Events. Chapman and Hall, London.
Crow, L. H. (1990). Evaluating the reliability of
repairable systems. In Reliability and Maintainability
Symposium, 1990, pages 275–279, Los Angeles,
USA. IEEE.
Garmabaki, A., Ahmadi, A., Mahmood, Y. A., and
Barabadi, A. (2015). Reliability modelling of multiple
repairable units. Quality and Reliability Engineering
International, 32(7):2329–2343.
Hogg, R. and Craig, A. (1978). Introduction to
Mathematical Statistics. MacMillan, New York, 4th
edition.
Karyagina, M., Wong, W., and Vlacic, L. (1998).
Life cycle cost modelling using marked point
processes. Reliability Engineering & System Safety,
59(3):291–298.
Kvaløy, J. T. and Lindqvist, B. H. (1998). TTT-based
tests for trend in repairable systems data. Reliability
Engineering & System Safety, 60(1):13–28.
Lewis, P. A. W. (1964a). A branching Poisson process
model for the analysis of computer failure patterns.
Journal of the Royal Statistical Society. Series B
(Methodological), pages 398–456.
Lewis, P. A. W. (1964b). Implications of a failure model
for the use and maintenance of computers. Journal of
Applied Probability, 1(02):347–368.
Papoulis, A. (1991). Probability, Random Variables, and
Stochastic Processes. McGraw-Hill, New York, 3rd
edition.
Procaccia, H., Ferton, E., and Procaccia, M. (2011).
Fiabilit
´
e et maintenance des mat
´
eriels industriels
r
´
eparables et non r
´
eparables. Lavoisier, Paris.
Rigdon, S. and Basu, A. (2000). Statistical Methods for the
Reliability of Repairable Systems. Wiley, New York.
Stephens, K. (2012). Reliability Data Analysis with Excel
and Minitab. ASQ Quality Press, Milwaukee.
Tobias, P. A. and Trindade, D. C. (2012). Applied
Reliability. CRC Press, Boca Raton, 3rd edition.
U.S. Department of Defense (1981). Military Handbook,
Reliability Growth Management (MIL-HDBK-189).
U.S. Government Printing Office.
Vaurio, J. (1999). Identification of process and
distribution characteristics by testing monotonic and
non-monotonic trends in failure intensities and hazard
rates. Reliability Engineering & System Safety,
64(3):345–357.
SIMULTECH 2019 - 9th International Conference on Simulation and Modeling Methodologies, Technologies and Applications
208