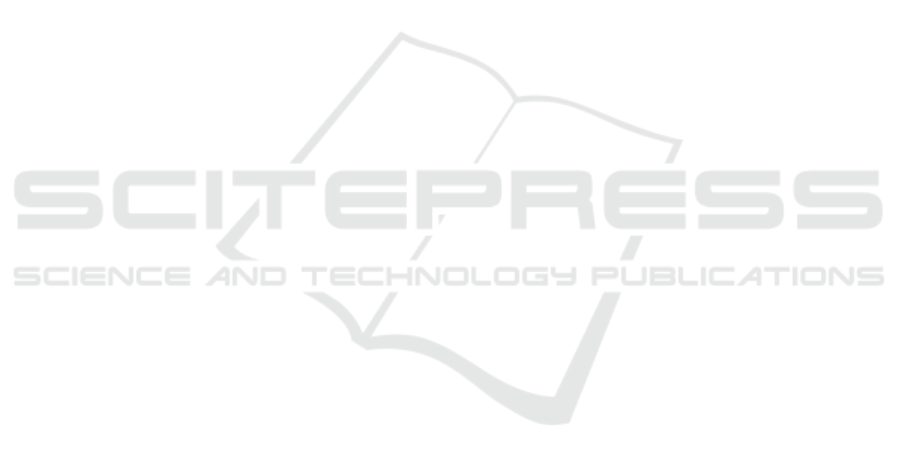
acquisition, automation and engineering in general
(Calderón et al., 2016). Some recent examples are
devoted to educational remote laboratories (Mejías et
al., 2017; Chacón et al., 2017), ZigBee-based wireless
networks (Pereira et al., 2015), CPSs (García et al.,
2016), greenhouse control (Robles et al., 2017), or
monitoring of fuel cells (Calderón et al., 2016; Segura
et al., 2017).
Nonetheless, despite the versatility of Arduino
boards, for industrial locations they present several
weaknesses like signals levels non-compliant with
industrial ranges, not suitability for rail-mounting,
low robustness, etc. (Puigt, 2015).
Within the context of the abovementioned new
paradigms, SCADA systems are required to exchange
data with new smart devices, sensors and/or actuators.
Precisely, Arduino boards are commonly used as
development platforms for such smart devices.
Therefore, communication solutions must be
designed towards the convergence of open source
hardware and widely used traditional SCADA-
devoted software. A widely used SCADA software
environments is Laboratory Virtual Instrumentation
Engineering Workbench (LabVIEW) of National
Instruments (LabVIEW Online). This package is
considered as representative due to the fact that it has
a worldwide presence and support for thousands of
technologies and instruments (Arpaia et al., 2015).
In this case, the integration of Arduino with
LabVIEW can be approached by means of the
LabVIEW Interface for Arduino (LIFA) toolkit.
Examples of the first approach have been reported in
(Calderón et al., 2016), (Segura et al., 2017) and
(Vivas et al., 2019), where an Arduino
microcontroller is used as data acquisition board for
measuring hydrogen fuel cells voltage and
temperature, whereas a LabVIEW-based interface
feeds information to the user.
Nevertheless, this toolkit does not provide
Ethernet connection. An option consists on
developing a TCP or UDP linkage between the
LabVIEW and the Arduino, but this solution involves
deep expertise about such kind of communication.
This paper presents a system that seamlessly
integrates Arduino boards into a LabVIEW-based
SCADA system through Ethernet connection and a
standardized protocol widely used for industrial
facilities, the Open Platform Communications (OPC)
interface.
In order to solve Ethernet communication, a
suitable option consists on using the open source
software package Arduino OPC Server, developed by
I. Martínez Marchena (Arduino OPC Server Online).
It enables the communication between Arduino
boards and software applications that support OPC
connectivity, like LabVIEW.
It must be noted that OPC interface was created in
1996 to handle interoperability in industrial control
and automation applications (OPC Foundation
Online). Currently, it is considered as one of the main
contenders to lead the standardization and systems
integration in advanced frameworks (González et al.,
2017b; González et al., 2019). According to the
literature survey conducted by the authors, there is no
paper reporting an OPC communication between
LabVIEW and Arduino.
This proposal is framed in a research project to
develop and implement a Smart Micro-Grid based on
renewable energy sources and its digital replica. To
this aim, an automation and supervision system is
crucial to manage and operate such challenging
facility. Arduino chips need to be connected to a
LabVIEW-based SCADA for a proper measurement
and monitoring of several of the involved variables.
The goal of this work is to promote the joint
utilization of open source tools with industrial
supervisory software. Therefore, with the aim of
demonstrating the feasibility and validity of the
proposed approach, an experimental system has been
implemented using an Arduino Mega and a
LabVIEW-based SCADA.
In the authors’ humble opinion, the integration of
the de facto standard software for supervision and
instrumentation, LabVIEW, and the versatility of the
open source Arduino microcontroller provides a
powerful benchmark for R&D activities in the fields
of Industry 4.0, IIoT and Smart Grids.
The remainder of the paper is as follows. Section
2 deals with the description of the developed system,
both hardware and software subsystems. In Section 3,
the development of the system and initial outcomes
are reported. Finally, main conclusions and further
works are outlined in Section 4.
2 MATERIALS AND METHODS
The developed system comprises hardware and
software components therefore; in this section the
involved entities are separately described.
2.1 Hardware Subsystem
Among the available Arduino boards (Uno, Yun,
Mini, Nano, Mega, Duemilanove, Lilypad, etc.) the
model Mega 2560 R3 has been selected. It
incorporates an ATmega2560 microcontroller, 16
analog inputs, 54 digital input/output ports, 4 UARTs,
Integration of Open Source Arduino with LabVIEW-based SCADA through OPC for Application in Industry 4.0 and Smart Grid Scenarios
175