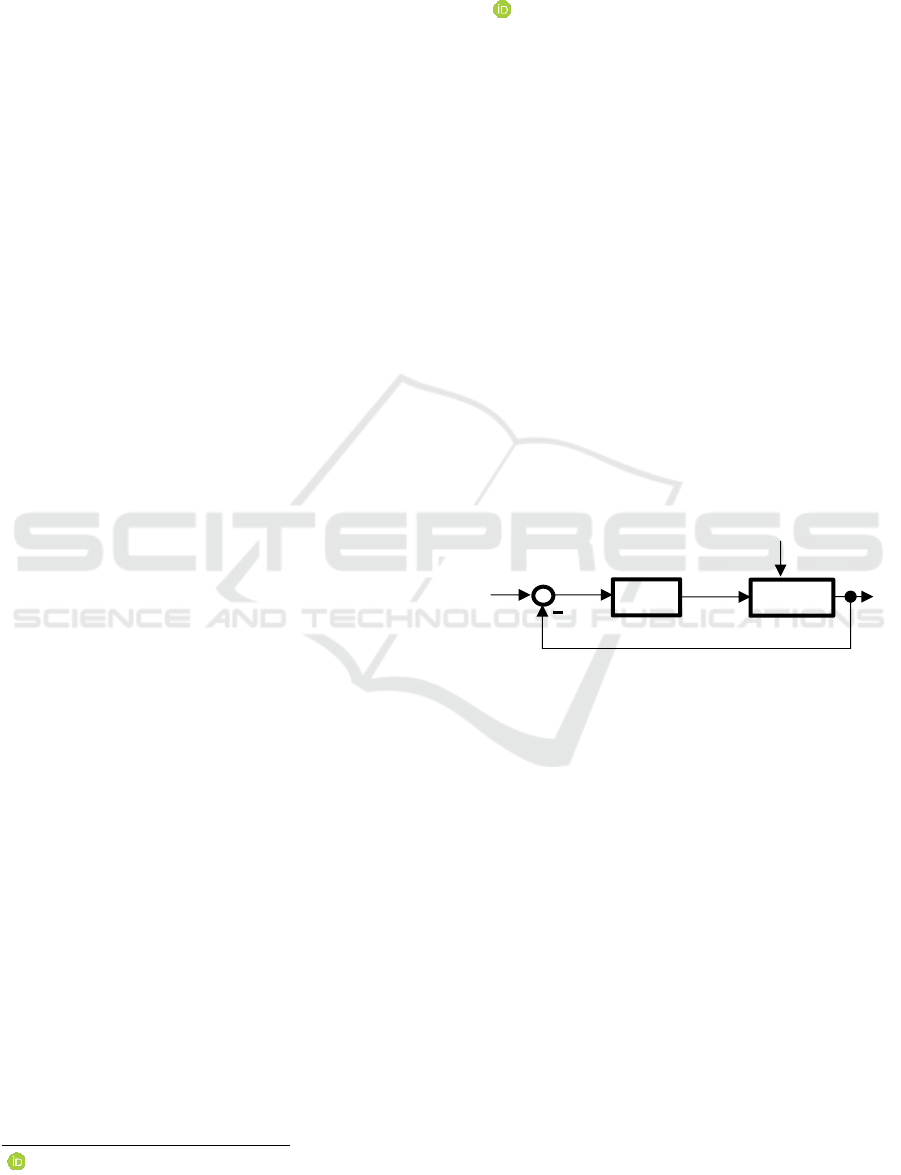
Improved Relay Feedback Identification using Shifting Method
M. Hofreiter
a
Department of Instrumentation and Control Engineering, Czech Technical University, Prague, Czech Republic
Faculty of Mechanical Engineering, Prague, Czech Republic
Keywords: System Identification, Static Gain, Relay Control, Parameter Estimation, Frequency Characteristic, Feedback,
Time Delay, Auto-tuning.
Abstract: This paper presents a new method for estimation of a static gain and remaining parameters of a second order
time delayed model by relay feedback identification. For this purpose, it uses a recently published method
called shifting method which enables to estimate two points of frequency characteristic from a single relay
feedback test. These two frequency response points are determined without any assumptions about a model
transfer function and they can be used for fitting parameters of a process transfer function with various
structures. For the first time the shifting method is used for a static gain estimation. This unique solution is
even applicable under constant load disturbance. A great advantage for practical use is the comprehensibility
and computational simplicity of the method. This identification method is primarily proposed for automatic
tuning of controllers. The method is demonstrated on a simulated example and a laboratory apparatus “Air
Aggregate”.
1 INTRODUCTION
There are many methods for automatic controller
tuning but only some of them are really used in
practice. Some of existing tuning rules for controllers
rely on a model of the process.
The relay feedback test belongs to autotuning
methods which are successfully applied in industry.
This approach for parameter identification and
autotuning PID controller was suggested by Åstrom
and Hägglund (1984). For this purpose, they
suggested the use of an ideal relay to generate a
sustained oscillation in the closed loop. A closed loop
where a process is under a relay control is illustrated
by the block diagram in Fig. 1, where w denotes the
desired variable, y the controlled variable, u the
manipulated variable, d the disturbance variable and
e the control error. This relay feedback approach
enables to calculate the ultimate gain and the ultimate
frequency like the Ziegler-Nichols method (Ziegler
and Nichols, 1943) but without a priory information
about the process, in a shorter time and in a controlled
manner.
The relay feedback test belongs among the most
popular methods in engineering applications for a
a
https://orcid.org/0000-0001-9373-2988
Figure 1: Block diagram of a process under relay feedback.
closed-loop identification. The main advantage of the
relay feedback test is to prevent the process drift away
from its set point. There are many relay-based
parametric estimation methods for single-input-single
output (SISO) systems. These methods can be
categorized into three groups, namely, describing
function method, curve fitting approach, and use of
frequency response estimation for model fitting (Liu,
Wang and Huang, 2013). There are several overview
publications dedicated to the relay feedback
identification, e.g. Yu (1999), Liu and Gao (2012),
Liu, Wang and Huang (2013), Chidambaram and
Sathe (2014), Kalpana and Thyagarajan (2018),
Ruderman (2019). The presented relay identification
methods are devoted mainly to the identification of
linear low-order time delayed models. Fortunately,
PID controllers tuned according to low-order models
of the processes can control most industrial processes
Hofreiter, M.
Improved Relay Feedback Identification using Shifting Method.
DOI: 10.5220/0007798406010608
In Proceedings of the 16th International Conference on Informatics in Control, Automation and Robotics (ICINCO 2019), pages 601-608
ISBN: 978-989-758-380-3
Copyright
c
2019 by SCITEPRESS – Science and Technology Publications, Lda. All rights reserved
601