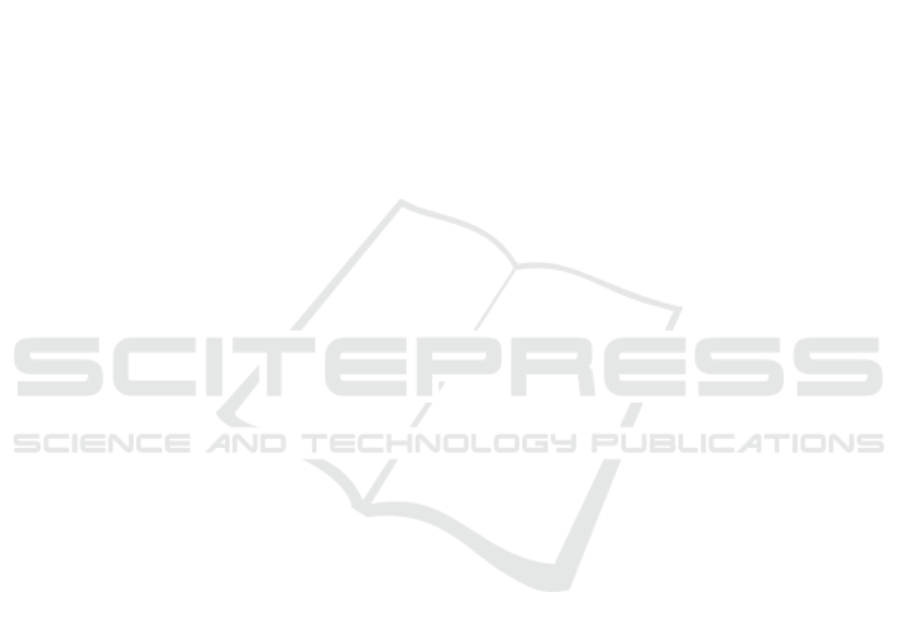
Software-in-the-Loop-simulation of a District Heating System as Test
Environment for a Sophisticated Operating Software
Ophelia Frotscher
1
, Thomas Oppelt
1
, Thorsten Urbaneck
1
, Sebastian Otto
2
, Ingrid Heinrich
2
,
Andreas Schmidt
2
, Thomas Göschel
3
,
Ulf Uhlig
3
and Holger Frey
3
1
Chemnitz University of Technology, Faculty of Mechanical Engineering, Professorship Applied Thermodynamics,
09107 Chemnitz, Germany
2
Ingenieurbüro Last- und Energiemanagement LEM Software, Nordplatz 6, 04105 Leipzig, Germany
3
inetz GmbH, Augustusburger Straße 1, 09111 Chemnitz, Germany
Keywords: Software-in-the-Loop, District Heating, Renewable Energy, Operation, Simulation, Optimisation.
Abstract: With the expansion of renewable energies, district heating (DH) systems are becoming increasingly complex.
Various heat sources like solar thermal plants and combined heat and power (CHP) plants are integrated in
parallel, in addition thermal energy storages (TES) are often used to balance load and heat generation.
Sophisticated software solutions are required to optimise the plant operation. Based on deterministic physical
models and artificial neural networks, the software Heating Network Navigator (HN-Navi) is being developed
to optimise the operation of such systems. Since tests in the real system are not possible for reasons of supply
security, the HN-Navi is first tested in a software-in-the-loop (SiL) environment. TRNSYS (version 18) is
used as simulation software to create a complex reference model (CRM) as basis for the SiL environment.
The complexity of such real energy systems can lead to potentially high computing costs when it comes to
simulating or optimising their operation as realistically and accurately as possible. For this reason, both
software tools, i.e. HN-Navi and CRM, will be developed and tested with regard to the Brühl solar DH system
in Chemnitz (Germany), whereby the finished software will also be used for other heat supply systems.
TRNSYS offers the possibility to develop own models for all system components, with which a proper
reproduction of the real system can be achieved. Within the scope of the project, practical tests and extensive
quantitative software comparisons with the real system will also be carried out. The article reports on the
development of this SiL environment and its practical feasibility.
1 INTRODUCTION
More and more district heating systems in Europe
combine different heat sources like solar thermal
plants and combined heat and power (CHP) plants
(solar district heating, 2019). In most cases a thermal
energy storage (TES) is applied for balancing load
and heat generation, e. g. the solar district heating
(DH) systems in the Brühl quarter in Chemnitz
(Urbaneck et al., 2015; Urbeneck et al., 2017,
Shrestha et al. 2017; Urbaneck et al. 2017; Urbaneck
et al. 2017). The different components within such
systems lead to complex structures with mutual
influences. This means that a quantitatively optimal
operation can only be guaranteed through the use of
sophisticated software solutions.
For this reason, numerous projects are now
dealing with the optimization of energy supply
systems. Widely used approaches include the use of
prediction models to estimate the availability of
renewable energies and energy demand (Kuboth et
al., 2019) and improved simulation models to
predictively describe the plant behaviour of such
systems (Schweiger et al. 2018).
The approach of this project, which has been
running since July 2017, is the optimization of the
supply facilities. One of the advantages is the direct
contact with the network operator without troubling
the end customers and the optimization of the control
of all system components. The developed software
system is named Heating Network Navigator (HN-
Navi) (Oppelt et al., 2018; Oppelt et al., 2018) and is
intended to help heating network operators to achieve
an optimal system operation despite difficult
boundary conditions (integration of fluctuating
renewable energy sources, varying electricity prices,
etc.) and complex technical demands.
Frotscher, O., Oppelt, T., Urbaneck, T., Otto, S., Heinrich, I., Schmidt, A., Göschel, T., Uhlig, U. and Frey, H.
Software-in-the-Loop-simulation of a District Heating System as Test Environment for a Sophisticated Operating Software.
DOI: 10.5220/0007809602230230
In Proceedings of the 9th International Conference on Simulation and Modeling Methodologies, Technologies and Applications (SIMULTECH 2019), pages 223-230
ISBN: 978-989-758-381-0
Copyright
c
2019 by SCITEPRESS – Science and Technology Publications, Lda. All rights reserved
223