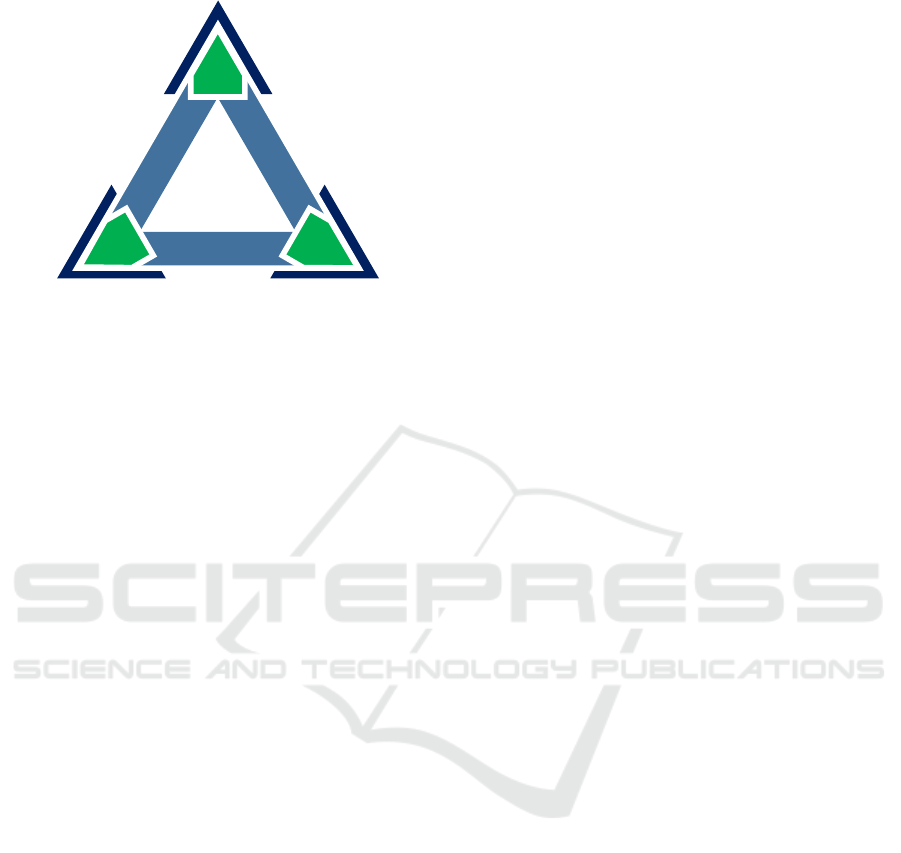
Surface finish
Accuracy Speed
Figure 2: Qualitative triangle: Speed-Accuracy-Surface fin.
tion to a specific one-shot off-line time parametriza-
tion of the motion trajectories given by individ-
ual lines of G-Code. For smoothing of the trajecto-
ries, a specific analytical algorithm employing B
´
ezier
curves of fifth-degree (quintic B
´
ezier curve) is pro-
posed. The degree of B
´
ezier curve was selected
to achieve smooth connection to other trajectory seg-
ments (Sencer et al., 2015). The problem can be
looked at from a more general point of view, repre-
sented by the qualitative triangle: Speed-Accuracy-
Surface finish, shown in Fig. 2. It depicts relations
among specific qualitative features taken in to account
in motion control. All three features cannot naturally
be achieved simultaneously in full. Instead, a suitable
compromise is sought, which respects the given tech-
nological and economic requirements.
Recently, the requirement is to have very short
production cycle with reasonable accuracy and qual-
ity. Therefore, to solve such antagonistic requirement
(dual problem), the technology takes into account def-
inite tolerances i.e. engineering fits, since no element
or part can be manufactured completely accurately.
The range of permissible dimensions or tolerances is
determined with respect to the element or part func-
tion. This feature determine useful admissible range
in which the motion trajectory should be maintained.
The size of the admissible range (tolerance) forms in-
terval for the motion smoothing. This idea of admis-
sible tolerances is considered in the intended solution
of smoothing problem, proposed here in our paper.
This paper is organized as follows. Section 2 de-
scribes the tested path model and its G-Code. Sec-
tion 3 contains the description of the proposed
smoothing algorithm based on a specific construction
of quintic B
´
ezier curves. Section 4 deals with arc-
length time parametrization procedure including the
computation of arc-length using Simpson’s rule, time
parametrization with respect to adaptive arc length
and backward decomposition to the individual Carte-
sian components, i.e. individual curve coordinates.
Section 5 demonstrates representative examples of
smoothed curves constructed by the proposed algo-
rithm implemented in MATLAB environment.
2 PATH MODEL AND G-CODE
Path model reflects the target application and its
technological parameters. In the case of machining,
the parameters include maximum feed rate, accelera-
tion and jerk. These parameters are given by the spe-
cific construction of the machine tool or robot. Limits
on mentioned parameters are accompanied by addi-
tional technological limits such as maximum cutting
velocity and required accuracy (admissible or pre-
scribed tolerances and character of nominal dimen-
sions).
All these parameters determine resultant motion,
the parameters of machine tools determine start-up
time (acceleration, time to reach the desired feed
rate from zero) and stopping time (deceleration, time
to stop from feed rate to zero) whereas inherent run-
ning phase depends on prescribed feed rate (given
by specific technology and the used cutting tool)
and the geometry of the motion path (Msaddek et al.,
2014; Luo et al., 2007).
Thus, the path model consists of the above men-
tioned constraints on the tool motion together
with the description of the path geometry. The sim-
plest (and still most common) way of describing
the geometry of the path is to use a combination of lin-
ear and circular arc segments. Other, more advanced
methods for the path description and representation
exist, such as B-spline, Akima spline and NURBS,
but these elements are not universally supported.
A lot of research has been done in the recent years
on the topic of construction of and motion planning
on these curves (Erkorkmaz et al., 2017; Heng and
Erkorkmaz, 2010; Sencer et al., 2015). However,
the research is still ongoing and the commercial im-
plementation is not yet common and standardized.
The used G-code in this paper is presented in this
section. Its parametric interpretation by linear seg-
ments and B
´
ezier curves will be used for the proposed
smoothing algorithm. The algorithm outputs will be
involved in the method of time parametrization.
Now, let us introduce the G-Code used for test-
ing. The elements in the G-Code are the fol-
lowing: Rapid positioning G00; Linear interpo-
lation G01; (for completeness: Circular interpola-
tions, clockwise/counterclockwise G02/G03; Dwell
ICINCO 2019 - 16th International Conference on Informatics in Control, Automation and Robotics
230