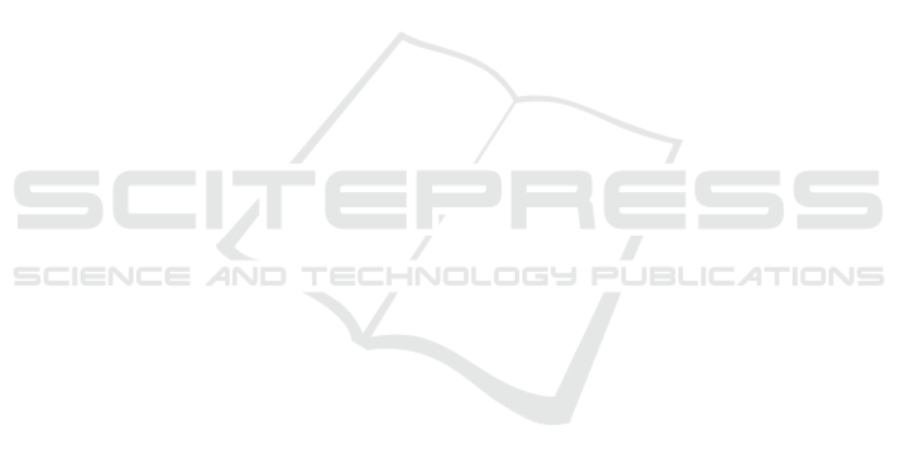
ing or endanger the safety of the personnel on plat-
forms. The vibration suppression for these large scale
boom systems is essential for improving the structure
fatigue life-cycle, operation efficiency and personnel
safety.
Some researchers focus on the dynamic analysis
of the boom structure, some others have investigated
the analysis of the whole boom system including hy-
draulic system and use hydraulic actuators to control
the structure vibration. Sun combined the finite el-
ement calculation method with mathematical formu-
lations of hydraulic drive system including essential
hydraulic components, to obtain a new model which
describes the dynamic interaction between the boom
structure and the drive system of mobile crane. (Sun
and Kleeberger, 2003). The method has been applied
for the exemplary calculation of slewing, lifting and
luffing operations of lattice boom cranes (Sun et al.,
2005)(Sun and Liu, 2006). Both the load-bearing
structure and the drive system can be described in
details. The calculation of a telescopic boom crane
has also been studied. Similar long boom systems
are also used in fire-rescue turntable ladders. The
boom system of a fire-rescue turntable ladder is a
telescopic lattice boom actuated by a hydraulic cylin-
der. Sawodny described the long fire-rescue turntable
ladder as a flexible multi-body system (Zuyev and
Sawodny, 2005) and the dynamic behavior of the hy-
draulic drive system was included in the mathemat-
ical model equations (Sawodny et al., 2002). In the
work of Pertsch (Pertsch et al., 2009), a distributed-
parameter model for the fire-rescue turntable ladder
was derived, based on the Euler-Bernoulli beam the-
ory. The model of the ladder structure was transferred
into low dimensional model space. In their recent
work (Pertsch and Sawodny, 2016), a model for the
coupled bending-torsional vibration associated with
the rotational motion of an articulated aerial ladder
has been derived and an active vibration damping con-
trol has been developed and validated in real opera-
tion.
The hydraulic actuated telescopic boom can be re-
garded as a multi-physical system consisting of the
mechanical structure, hydraulic drives and electrical
control system. The interconnections between the
subsystems are achieved by hydraulic actuators and
electro-hydraulic servo systems. With the increas-
ing demands for more accurate control precision dur-
ing the operations of these long boom manipulators,
the dynamic analysis for such multi-physical systems
has been extended from the dynamic respond study
of separated subsystems to a coupling analysis of dif-
ferent domain subsystems. The bond-graph method
(Gawthrop and Bevan, 2007) is a graphical approach
in which the component energy ports are connected
by bonds using power-conjugate variables, efforts
and flows, to illustrate the energy transformation and
conversion between components and different phys-
ical systems. This port-based modeling method is
widely used to build a mathematical model of electro-
mechanical multi-domain systems (Guo et al., 2016)
(Cheng et al., 2016). The representation of a physi-
cal system as a bond graph can lead to a dynamical
system endowed with a geometric structure, which is
called a Port-Hamiltonian (PH) system. The geomet-
ric structure called Dirac structure is introduced as the
key mathematical concept to unify the description of
complex interactions in multi-physical systems. The
Hamiltonian function of the system energy which is
used to derive system state space equations, can also
be used as Lyapunov function for stability analysis.
Many researchers did a lot of work on the
system modeling and control design for flexible
beam systems based on their representation as Port-
Hamiltonian system. Macchelli also reformulated the
Timoshenko model of beam within the framework
of the Port-Hamiltonian system (Macchelli and Mel-
chiorri, 2004). The transitional and rotational deflec-
tions and momenta were chosen as state variables to
build the (Stokes-) Dirac structure. He also used Port-
Hamiltonian approach to describe the multi-body sys-
tem (rigid body, flexible links and kinematic pairs)
based on the power conserving interconnection (Mac-
chelli et al., 2009). In order to solve the infinite di-
mensional model in Port-Hamiltonian formulation, a
structure-preserving discretization method is needed.
So that the discretized finite-dimensional model still
has the property of (Stokes-) Dirac structure (Moulla
et al., 2012)(Vu et al., 2013). Wang applied a ge-
ometric pseudo-spectral discretization to obtain the
finite-dimensional Port-Hamiltonian framework of
linear Timoshenko beam model, and solved the feed-
forward motion control problem based on this lumped
model (Wang et al., 2017). For the hydraulic sys-
tems, Kugi designed a nonlinear controller for a clas-
sical hydraulic piston actuator system based on the
Port-Hamiltonian model (Kugi and Kemmetm
¨
uller,
2004). In his doctor thesis (Stadlmayr, 2009), Stadl-
mayr gave a Port-Hamiltonian representation of flex-
ible manipulator consisting a long boom with a mass
at the tip and a hydraulic system using hydraulic
cylinder to actuate the manipulator (Stadlmayr and
Schlacher, 2004). Combined with feed-forward and
feedback control system, a MIMO-control was de-
signed and used to accomplish path tracking and vi-
bration suppression for the flexible manipulator.
SIMULTECH 2019 - 9th International Conference on Simulation and Modeling Methodologies, Technologies and Applications
70