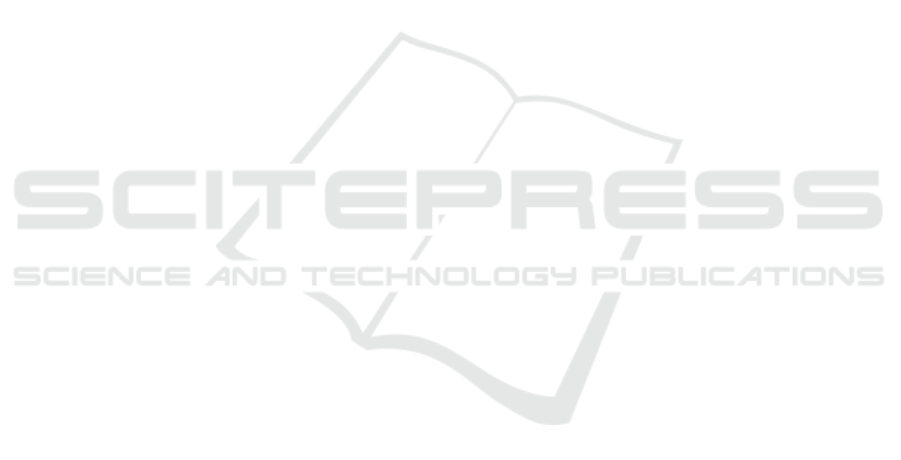
nipulator with flexible links. In Proceedings of the 3
rd
Joint International Conference on Multibody System
Dynamics and the 7
th
Asian Conference on Multibody
Dynamics, Busan, Korea.
Eberhard, P. and Ansarieshlaghi, F. (2019). Nonlinear posi-
tion control of a very flexible parallel robot manip-
ulator. In Proceedings ECCOMAS Thematic Con-
ference on Multibody Dynamics, Duisburg, Germany
(accepted for publication).
Endo, T., Sasaki, M., Matsuno, F., and Jia, Y. (2017).
Contact-force control of a flexible timoshenko arm in
rigid/soft environment. IEEE Transactions on Auto-
matic Control, 62(5):2546–2553.
Feliu-Talegon, D., Feliu-Batlle, V., Tejado, I., Vinagre,
B. M., and HosseinNia, S. H. (2019). Stable force
control and contact transition of a single link flexible
robot using a fractional-order controller. ISA transac-
tions.
Hogan, N. (1985). Impedance control: An approach to ma-
nipulation: Part II–Implementation. Journal of Dy-
namic Systems, Measurement, and Control, 107(1):8–
16.
Jung, S., Hsia, T. C., and Bonitz, R. G. (2004). Force track-
ing impedance control of robot manipulators under
unknown environment. IEEE Transactions on Con-
trol Systems Technology, 12(3):474–483.
Kamikawa, Y., Enayati, N., and Okamura, A. M. (2018).
Magnified force sensory substitution for telemanipu-
lation via force-controlled skin deformation. In IEEE
International Conference on Robotics and Automation
(ICRA), pages 1–9, Brisbane, Australia.
Khalil, H. K. (2002). Nonlinear systems, volume 3. Prentice
hall, Upper Saddle River.
Li, Y., Ganesh, G., Jarrass
´
e, N., Haddadin, S., Albu-
Schaeffer, A., and Burdet, E. (2018). Force,
impedance, and trajectory learning for contact tool-
ing and haptic identification. IEEE Transactions on
Robotics, 34(5):1170–1182.
Luh, J., Fisher, W., and Paul, R. (1983). Joint torque con-
trol by a direct feedback for industrial robots. IEEE
Transactions on Automatic Control, 28(2):153–161.
Morlock, M., Burkhardt, M., Schr
¨
ock, C., and Seifried,
R. (2017). Nonlinear state estimation for trajectory
tracking of a flexible parallel manipulator. IFAC-
PapersOnLine, 50(1):3449–3454.
Morlock, M., Burkhardt, M., and Seifried, R. (2016).
Control of vibrations for a parallel manipulator
with flexible links - concepts and experimental re-
sults. In MOVIC & RASD, International Conference,
Southampton, England.
Sandoval, J., Su, H., Vieyres, P., Poisson, G., Ferrigno,
G., and Momi, E. D. (2018). Collaborative frame-
work for robot-assisted minimally invasive surgery us-
ing a 7-dof anthropomorphic robot. Robotics and Au-
tonomous Systems, 106:95–106.
Schindlbeck, C. and Haddadin, S. (2015). Unified passivity-
based cartesian force/impedance control for rigid and
flexible joint robots via task-energy tanks. In IEEE
international conference on robotics and automation
(ICRA), pages 440–447, Seattle, Washington. IEEE.
Seifried, R., Burkhardt, M., and Held, A. (2011). Trajec-
tory control of flexible manipulators using model in-
version. In Proceedings of the ECCOMAS Thematic
Conference on Multibody Dynamics, Brussels, Bel-
gium.
Siciliano, B. and Khatib, O., editors (2016). Springer Hand-
book of Robotics. Springer Heidelberg.
Siciliano, B. and Villani, L. (1999). Robot Force Control.
Springer Science & Business Media.
Suarez, A., Giordano, A. M., Kondak, K., Heredia, G., and
Ollero, A. (2018). Flexible link long reach manipu-
lator with lightweight dual arm: Soft-collision detec-
tion, reaction, and obstacle localization. In IEEE In-
ternational Conference on Soft Robotics (RoboSoft),
pages 406–411. IEEE.
Vogel, J., Haddadin, S., Jarosiewicz, B., Simeral, J. D.,
Bacher, D., Hochberg, L. R., Donoghue, J. P., and
van der Smagt, P. (2015). An assistive decision-and-
control architecture for force-sensitive hand–arm sys-
tems driven by human–machine interfaces. The In-
ternational Journal of Robotics Research, 34(6):763–
780.
Hybrid Force/Position Control of a Very Flexible Parallel Robot Manipulator in Contact with an Environment
67