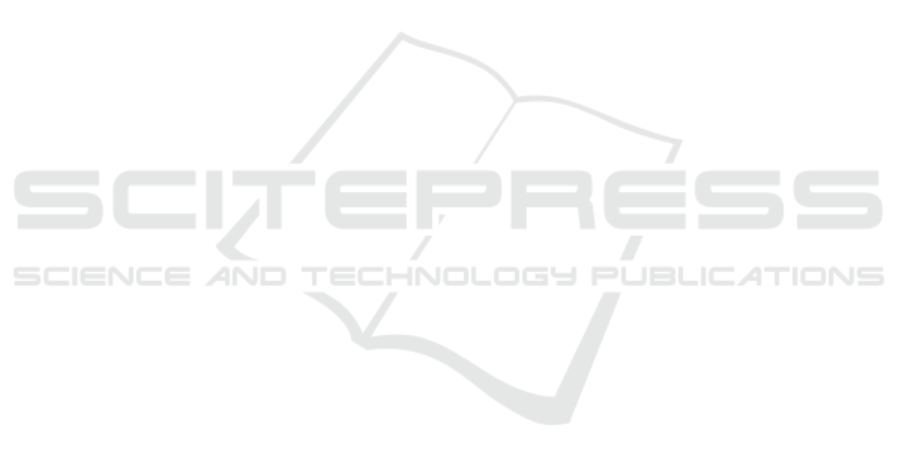
workers of the future. In IEEEE Robotics & Automation
Magazine.
Blackmore, S., 2009. New concepts in agricultural
automation. In HGCA conference.
Fang, H., Fan, R., Thuilot, B., Martinet, P., 2005. Trajectory
tracking control of farm vehicles in presence of sliding,
In IEEE/RSJ International conference on Intelligent
Robots and Systems.
Hiramatsu, T., Morita, S., Pencelli, M., Niccolini, M.,
Ragaglia, M., Argiolas, A., 2019. Path-Tracking
controller for tracked mobile robot on rough terrain, In
International conference on field and service robotics.
Huang, D., Hai, J., 2015. Trajectory tracking control of
wheeled mobile robots based on disturbance observer,
In IEEE Chinese Automation Congress.
Hyungbo, S., Gyunghoon, P., Youngjun, J., Juhoon, B.,
Nam Hoon, J., 2016. Yet another tutorial of disturbance
observer: robust stabilization and recovery of nominal
performance. In Control theory and technology. South
China University of technology and academy of
mathematics and systems science, vol. 14.
Lenain, R., Thuilot, B., Cariou, C., Martinet, P., 2004.
Adaptive and predictive nonlinear control for sliding
vehicle guidance, In IEEE/RSJ International
conference on Intelligence Robots and Systems.
MathWorks, 2018 Modeling a vehicle dynamics system,
retrieved February 7, 2019 from
https://jp.mathworks.com/help/ident/examples/modeli
ng-a-vehicle-dynamics-system.html?lang=en.
Morita, S., Hiramatsu, T., Niccolini, M., Argiolas, A.,
Ragaglia, M., 2018. Kinematic track modelling for fast
multiple body dynamics simulation of tracked vehicle
robot, In The 24th International Conference on
Methods and Models in Automation and Robotics.
Narby, E., 2006. Modeling and estimation of dynamics tire
properties, In examensarbete, Department of Electrical
Engineering Linköpings tekniska högskola Linköpings
universitet.
Nguyen, B., M., Fujimoto, H., Hori Y., 2014. Yaw angle
control for autonomous vehicle using Kalman filter
based disturbance observer. In SAEJ. EVTeC and APE
Japan.
Noguchi, N., Barawid Jr, O, C., 2011. Robot farming
system using multiple robot tractors in Japan
agriculture. In 18
th
IFAC world congress Milano.
Pentzer, J., Brennan, S., Reichard, K., 2014. Model-based
Prediction of Skid-steer Robot Kinematics Using
Online Estimation of Track Instantaneous Centers of
Rotation, In Journal of Field Robotics.
Rathgeber, C., Winkler, F., Odenthal, D., Muller, S., 2015.
Disturbance observer for lateral trajectory tracking
control for autonomous and cooperative driving. In
International journal of mechanics and mechatronics
engineering vol. 9.
Samuel, M., Hussein, M., Mohamad, B., Lucky, W., 2016.
A review of some pure-pursuit based path tracking
techniques for control of autonomous vehicles, In
International journal of computer applications.
Shalal, N., Low, T., McCarthy, C., Hancock, N., 2013. A
review of autonomous navigation systems in
agricultural environments, In SEAg 2013.
Taghia, J., Katupitiya, J., 2013. A sliding mode controller
with disturbance observer for a farm vehicle operating
in the presence of wheel slip. In IEEE/ASME
international conference on advanced intelligent
mechatronics.
Wen-Hua, C., Jun, Y., Lei, G., Shihua, L., 2016.
Disturbance-observer-based control and related
methods – An overview. In IEEE Transl. Industrial
electronics., vol. 63.
Werner, R., 2015. Centimeter-level accuracy path tracking
control of tractors and activity steered implements.
Ph.D. thesis, Technischen Universität Kaiserslautern
zur Verleihung des akademischen Grades.
Yu, S., Wang, J., Wang, Y., Chen, H., 2018. Disturbance
observer based control for four wheel steering vehicles
with model reference. In IEEE/CAA Journal of
Automatica Sinica,
ICINCO 2019 - 16th International Conference on Informatics in Control, Automation and Robotics
258