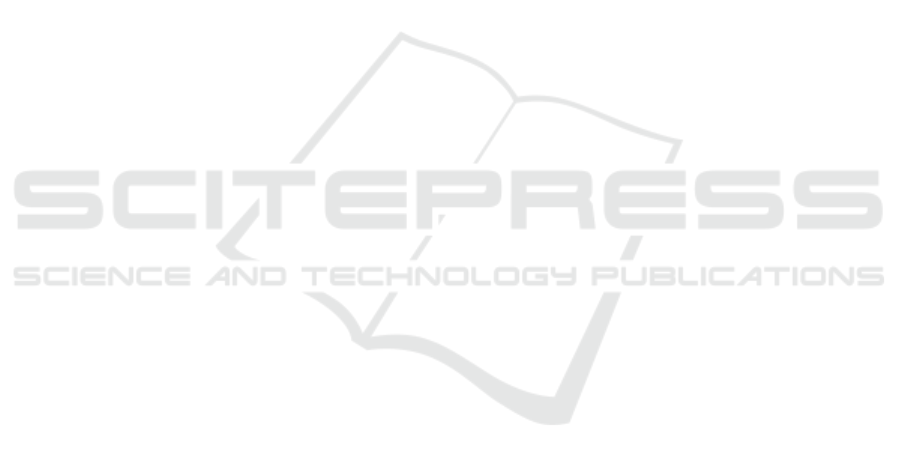
reference torques. Experiments are conducted on a
UR5e robot with the proposed TVIST implementation
to validate its effectiveness.
Preliminary experimental results demonstrate that
the new TVIST implementation yields effective vibra-
tion suppression in the UR5e robot, and reduces the
residual vibrations by 78.5-88.6% in the tested cases.
In addition, experimental results show that it is possible
to increase the productivity of the robot by up to 6.3%
because the stabilization time is significantly reduced
through the proposed TVIST implementation strategy.
We can conclude that the proposed method facili-
tates practical implementation of TVIST for vibration
suppression on commercial industrial robots that has
online trajectory generation and position control with
feed-forward velocity and torque.
ACKNOWLEDGEMENTS
This work was supported by Universal Robots A/S
and Innovation Fund Denmark, through the Industrial
PhD program. We wish to thank Anders Skovgaard
Knudsen from Universal Robots A/S for his valuable
help in proofreading.
REFERENCES
Beazel, V. M. (2004). Command shaping applied to nonlin-
ear systems with configuration-dependent resonance.
PhD thesis, Purdue University.
Biagiotti, L. and Melchiorri, C. (2008). Trajectory Planning
for Automatic Machines and Robots. Springer-Verlag
Berlin Heidelberg.
Book, W. (1993). Controlled motion in an elastic world.
Journal of Dynamic Systems, Measurement and Control,
Transactions of the ASME, 115(2B):252–261.
Chang, P. H. and Park, H.-S. (2005). Time-varying input
shaping technique applied to vibration reduction of
an industrial robot. Control Engineering Practice,
13(1):121 – 130.
Chatlatanagulchai, W., Beazel, V. M., and Meckl, P. H.
(2006). Command shaping applied to a flexible robot
with configuration-dependent resonance. In 2006 Amer-
ican Control Conference.
Cho, J.-K. and Park, Y.-S. (1995). Vibration reduction in
flexible systems using a time-varying impulse sequence.
Robotica, 13(3):305–313.
Cole, M. O. (2011). A discrete-time approach to impulse-
based adaptive input shaping for motion control without
residual vibration. Automatica, 47(11):2504 – 2510.
Hearne, J. (2009). Posture dependent vibration resistance of
serial robot manipulators to applied oscillating loads.
Master’s thesis, University of Waterloo.
ISO 9283 (1998). Manipulating industrial robots - perfor-
mance criteria and related test methods.
Khalil, W. and Dombre, E. (2004). Modeling Identification
and Control of Robots. Butterworth-Heinemann.
Kim, J. and Croft, E. A. (2018). Preshaping input trajectories
of industrial robots for vibration suppression. Robotics
and Computer-Integrated Manufacturing, 54:35 – 44.
Kivila, A. (2017). Modeling, estimation and control for
serial flexible robot arms. PhD thesis, Georgia Institute
of Technology.
Kozak, K., Singhose, W., and Ebert-Uphoff, I. (2006). Per-
formance measures for input shaping and command
generation. Journal of Dynamic Systems, Measurement
and Control, Transactions of the ASME, 128(3):731–
736.
Laakso, T. I., Valimaki, V., Karjalainen, M., and Laine, U. K.
(1996). Splitting the unit delay - tools for the fractional
delay filter design. IEEE Signal Processing Magazine,
13(1):30–60.
Magee, D. P. (1996). Optimal arbitrary time-delay filtering
to minimize vibration in elastic manipulator systems.
PhD thesis.
Magee, D. P. and Book, W. J. (1992). The application
of input shaping to a system with varying parameters.
In Japan/USA Symposium on Flexible Automation,
volume 1, pages 519–526.
Murphy, B. R. and Watanabe, I. (1992). Digital shaping fil-
ters for reducing machine vibration. IEEE Transactions
on Robotics and Automation, 8(2):285–289.
Pham, M. T., Gautier, M., and Poignet, P. (2002). Ac-
celerometer based identification of mechanical systems.
In Proceedings 2002 IEEE International Conference
on Robotics and Automation (Cat. No.02CH37292),
volume 4, pages 4293–4298 vol.4.
Rappole, B. W. (1992). Minimizing residual vibrations
in flexible systems. Master’s thesis, MIT Artificial
Intelligence Laboratory.
Sayahkarajy, M., Mohamed, Z., and Faudzi, A. A. M. (2016).
Review of modelling and control of flexible-link manip-
ulators. Proceedings of the Institution of Mechanical
Engineers, Part I: Journal of Systems and Control
Engineering, 230(8):861–873.
Singer, N. C. (1989). Residual vibration reduction in com-
puter controlled machines. PhD thesis, Massachusetts
Institute of Technology. Dept. of Mechanical Engineer-
ing.
Singer, N. C. and Seering, W. P. (1990). Preshaping
command inputs to reduce system vibration. Jour-
nal of Dynamic Systems, Measurement, and Control,
112(1):76–82.
Singh, T. and Vadali, S. (1993). Robust time-delay control.
Journal of dynamic systems, measurement, and control,
115(2A):303–306.
Thomsen, D. K., Søe-Knudsen, R., Brandt, D., Balling, O.,
and Zhang, X. (2018). Generating vibration free rest-to-
rest trajectories for configuration dependent dynamic
systems via 3-segmented input shaping. In IEEE
International Conference on Robotics and Automation.
Thomsen, D. K., Søe-Knudsen, R., Brandt, D., Balling, O.,
and Zhang, X. (2019). Smooth online time-varying in-
put shaping with fractional delay FIR filtering. Control
Engineering Practice, 88:21–37.
Experimental Implementation of Time-varying Input Shaping on UR Robots
497