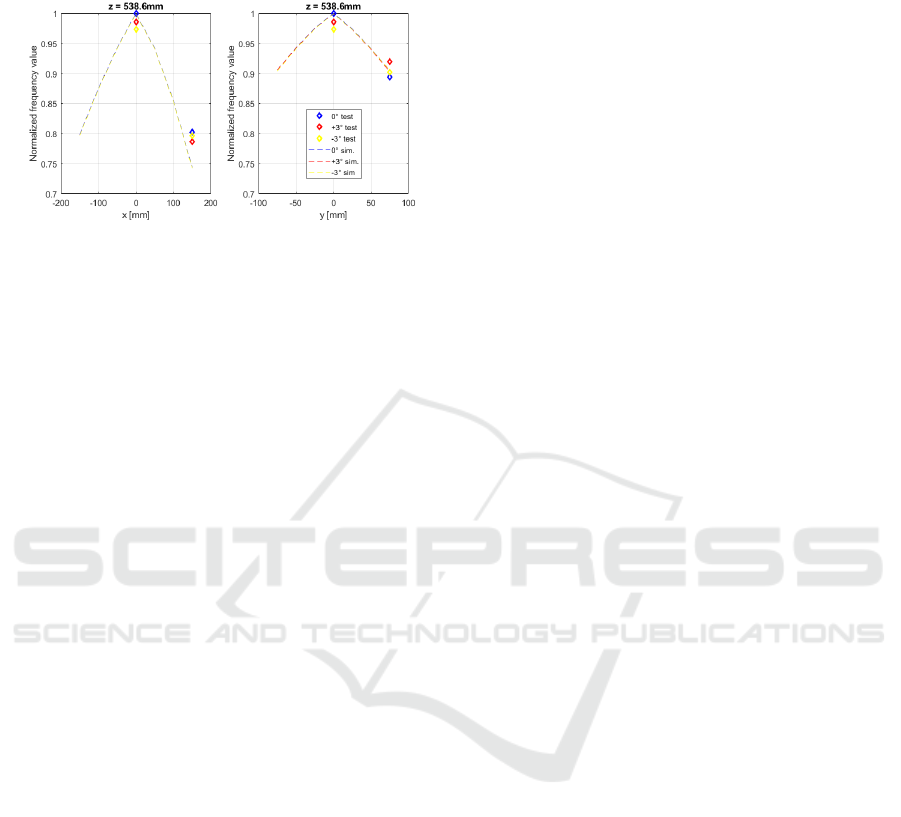
ered negligible in the frequencies distribution into
workspace (fig. 15).
Figure 15: Yaw angle influence.
7 CONCLUSIONS
In this article, a complete methodology for modal
analysis of a 6 DOF parallel kinematics robot is
proposed. In alternative to literature methods, the
proposed procedure do not use complex simulations
setup and expensive experimental campaigns. Simu-
lation analysis has been designed in order to be simple
and effective, with the only support of a approximate
flexible-multibody model. Simulation campaign has
highlighted: modal shapes and their change through
workspace exploration, sensor and hitting points op-
timum configuration and minimum first frequency
robot configuration. These information has been used
for optimal experimental campaign design and iden-
tification of a small set of configuration on which
fine FEM simulation could be set up. Experimental
campaign has been setup with minimum amount of
sensors and effective testing procedure. A complete
data post processing method has been also proposed,
particularly suitable con complex PKM with coupled
modes and taking into account real world data issues.
REFERENCES
Allemang, R. J., Brown, D. L., and Fladung, W. (1994).
Modal parameter estimation: a unified matrix polyno-
mial approach. In Proceedings - SPIE The Interna-
tion Society For Optical Engineering, pages 501–501.
SPIE Internation Society For Optical.
Bayati, I., Belloli, M., Bernini, L., Giberti, H., and Zasso,
A. (2017). Scale model technology for floating off-
shore wind turbines. IET Renewable Power Genera-
tion, 11(9):1120–1126.
Bayati, I., Belloli, M., Ferrari, D., Fossati, F., and Giberti,
H. (2014). Design of a 6-dof robotic platform for wind
tunnel tests of floating wind turbines. Energy Proce-
dia, 53:313–323.
Brandt, A. (2011). Noise and vibration analysis: signal
analysis and experimental procedures. John Wiley &
Sons.
Confalonieri, M., Ferrario, A., and Silvestri, M. (2018).
Calibration of an on-board positioning correction sys-
tem for micro-edm machines. In EUSPEN Conference
Proceedings - 18th International Conference and Ex-
hibition, pages 153–154.
Fu, Z.-F. and He, J. (2001). Modal analysis. Elsevier.
Giberti, H. and Ferrari, D. (2015). A novel hardware-in-
the-loop device for floating offshore wind turbines
and sailing boats. Mechanism and Machine Theory ,
85(Supplement C):82 – 105.
Giberti, H., La Mura, F., Resmini, G., and Parmeggiani, M.
(2018). Fully mechatronical design of an hil system
for floating devices. Robotics, 7(3):39.
La Mura, F., Roman
´
o, P., Fiore, E., and Giberti, H. (2018a).
Workspace limiting strategy for 6 dof force controlled
pkms manipulating high inertia objects. Robotics,
7(1):10.
La Mura, F., Todeschini, G., and Giberti, H. (2018b).
High performance motion-planner architecture for
hardware-in-the-loop system based on position-based-
admittance-control. Robotics, 7(1):8.
Mejri, S., Gagnol, V., Le, T.-P., Sabourin, L., Ray, P., and
Paultre, P. (2016). Dynamic characterization of ma-
chining robot and stability analysis. The Interna-
tional Journal of Advanced Manufacturing Technol-
ogy, 82(1-4):351–359.
Palmieri, G., Martarelli, M., Palpacelli, M., and Carbonari,
L. (2014). Configuration-dependent modal analysis of
a cartesian parallel kinematics manipulator: numeri-
cal modeling and experimental validation. Meccanica,
49(4):961–972.
Silvestri, M., Pedrazzoli, P., Bo
¨
er, C., and Rovere, D.
(2011). Compensating high precision positioning ma-
chine tools by a self learning capable controller. In
Proceedings of the 11th international conference of
the european society for precision engineering and
nanotechnology, pages 121–124.
Vu, V.-H., Liu, Z., Thomas, M., Li, W., and Hazel, B.
(2016). Output-only identification of modal shape
coupling in a flexible robot by vector autoregressive
modeling. Mechanism and Machine Theory, 97:141–
154.
Wiens, G. J. and Hardage, D. S. (2006). Structural dy-
namics and system identification of parallel kinematic
machines. In ASME 2006 International Design En-
gineering Technical Conferences and Computers and
Information in Engineering Conference, pages 749–
758. American Society of Mechanical Engineers.
Theoretical and Experimental Modal Analysis of a 6 PUS PKM
283