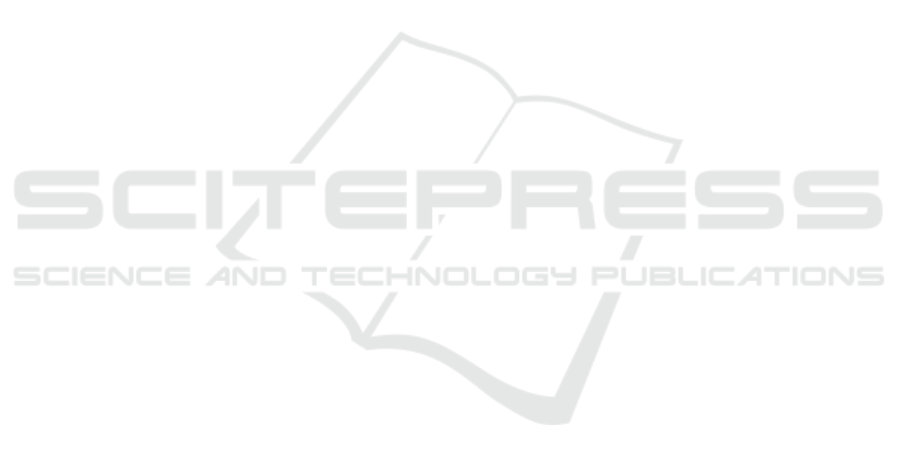
REFERENCES
Andersson, S., S
¨
oderberg, A., and Bj
¨
orklund, S. (2007).
Friction models for sliding dry, boundary and
mixed lubricated contacts. Tribology international,
40(4):580–587.
Bayati, I., Belloli, M., Bernini, L., Giberti, H., and Zasso,
A. (2017). Scale model technology for floating off-
shore wind turbines. IET Renewable Power Genera-
tion, 11(9):1120–1126.
Bayati, I., Belloli, M., Ferrari, D., Fossati, F., and Giberti,
H. (2014). Design of a 6-dof robotic platform for wind
tunnel tests of floating wind turbines. Energy Proce-
dia, 53:313–323.
Berman, A., Ducker, W., and Israelachvili, J. (1996). Ori-
gin and characterization of different stick-slip friction
mechanisms. Langmuir, 12(19).
Chen, Y.-Y., Huang, P.-Y., and Yen, J.-Y. (2002).
Frequency-domain identification algorithms for servo
systems with friction. IEEE transactions on control
systems technology, 10(5):654–665.
Confalonieri, M., Ferrario, A., and Silvestri, M. (2018).
Calibration of an on-board positioning correction sys-
tem for micro-edm machines. In EUSPEN Conference
Proceedings - 18th International Conference and Ex-
hibition, pages 153–154.
Ferrari, D. and Giberti, H. (2014). A genetic algorithm ap-
proach to the kinematic synthesis of a 6-dof parallel
manipulator. In 2014 IEEE Conference on Control
Applications (CCA), pages 222–227.
Fiore, E., Giberti, H., and Ferrari, D. (2016). Dynamics
modeling and accuracy evaluation of a 6-dof hexaslide
robot. In Nonlinear Dynamics, Volume 1, pages 473–
479. Springer.
Giberti, H. and Ferrari, D. (2015). A novel hardware-in-
the-loop device for floating offshore wind turbines
and sailing boats. Mechanism and Machine Theory,
85(Supplement C):82 – 105.
Giberti, H., La Mura, F., Resmini, G., and Parmeggiani, M.
(2018). Fully mechatronical design of an hil system
for floating devices. Robotics, 7(3):39.
Keck, A., Zimmermann, J., and Sawodny, O. (2017). Fric-
tion parameter identification and compensation us-
ing the elastoplastic friction model. Mechatronics,
47:168–182.
Kim, M.-S. and Chung, S.-C. (2006). Friction identifica-
tion of ball-screw driven servomechanisms through
the limit cycle analysis. Mechatronics, 16(2):131–
140.
La Mura, F., Roman
´
o, P., Fiore, E., and Giberti, H. (2018a).
Workspace limiting strategy for 6 dof force controlled
pkms manipulating high inertia objects. Robotics,
7(1):10.
La Mura, F., Todeschini, G., and Giberti, H. (2018b).
High performance motion-planner architecture for
hardware-in-the-loop system based on position-based-
admittance-control. Robotics, 7(1):8.
Lee, W., Lee, C.-Y., Jeong, Y. H., and Min, B.-K. (2015).
Distributed component friction model for precision
control of a feed drive system. IEEE/ASME Trans-
actions on Mechatronics, 20(4):1966–1974.
Maeda, Y. and Iwasaki, M. (2013). Initial friction compen-
sation using rheology-based rolling friction model in
fast and precise positioning. IEEE Transactions on
Industrial Electronics, 60(9):3865–3876.
Negahbani, N., Giberti, H., and Fiore, E. (2016). Error
analysis and adaptive-robust control of a 6-dof paral-
lel robot with ball-screw drive actuators. Journal of
Robotics, 2016.
Olaru, D., Puiu, G. C., Balan, L. C., and Puiu, V. (2004).
A new model to estimate friction torque in a ball
screw system. In Product engineering, pages 333–
346. Springer.
Raineri, I., La Mura, F., and Giberti, H. (2018). Digital twin
development of hexafloat, a 6dof pkm for hil tests.
In The International Conference of IFToMM ITALY,
pages 258–266. Springer.
Ro, P. I., Shim, W., and Jeong, S. (2000). Robust fric-
tion compensation for submicrometer positioning and
tracking for a ball-screw-driven slide system. Preci-
sion Engineering, 24(2):160–173.
Silvestri, M., Pedrazzoli, P., Bo
¨
er, C., and Rovere, D.
(2011). Compensating high precision positioning ma-
chine tools by a self learning capable controller. In
Proceedings of the 11th international conference of
the european society for precision engineering and
nanotechnology, pages 121–124.
Xu, N., Tang, W., Chen, Y., Bao, D., and Guo, Y. (2015).
Modeling analysis and experimental study for the fric-
tion of a ball screw. Mechanism and Machine Theory,
87:57–69.
ICINCO 2019 - 16th International Conference on Informatics in Control, Automation and Robotics
640