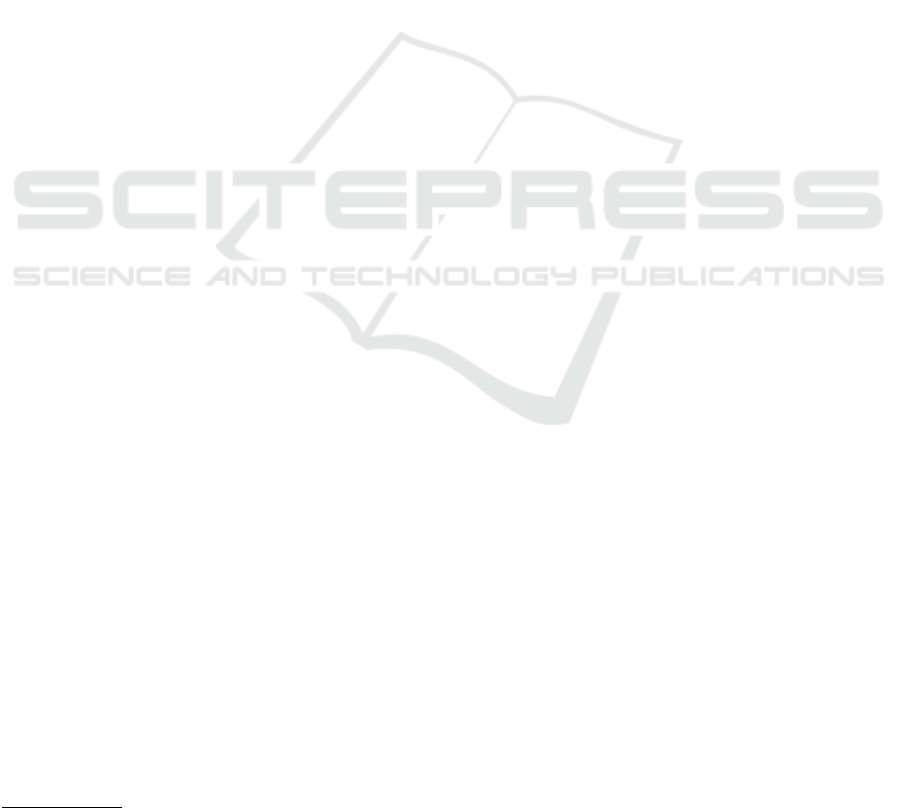
be improved for example with a Debian package. As
soon as OSI is running, it is easy to use.
5 CONCLUSION
In this paper, a co-simulation setup is described using
the Open Simulation Interface for testing automated
driving functions. Generic and standardized inter-
faces help to reduce the integration effort and enable
flexibility and interchangeability. OSI defines such a
generic interface to describe environment and sensor
data for validating automated driving functions in vir-
tual scenarios. In a demonstrator, developed within
the European research project Enable-S3, we vali-
dated an ACC function based on co-simulation tech-
niques. The demonstrator is based on standardized
interfaces to provide a modular and flexible simula-
tion framework in which scenarios, simulation units
and the function under test can easily be exchanged.
Therefore, we used OSI to connect an environment
simulation application, a sensor model and a visu-
alization component to validate ADAS functionality.
We had to extend tools to be able to exchange com-
plex data types, such as object lists, which was nec-
essary to test automated driving functions. Based on
this co-simulation setup, we analyzed OSI v3 with re-
gard to content and performance. We think OSI is a
promising specification and is also considered to be-
come an ASAM
6
standard. For the demonstrator we
used OSI on object list level. As a next step we would
like to analyze this interface specification with sen-
sor low level data. Further, we work on an imple-
mentation of the Distributed Co-Simulation Protocol
to be used instead of the TCP connection. This en-
ables a standardized distributed simulation and sup-
ports hence interchangeability and interoperability.
ACKNOWLEDGEMENTS
This work has been conducted within the ENABLE-
S3 project that has received funding from the ECSEL
JOINT UNDERTAKING under GRANT AGREE-
MENT No 692455. This JOINT UNDERTAKING
receives support from the European Union’s HORI-
ZON 2020 RESEARCH AND INNOVATION PRO-
GRAMME and Austria, Denmark, Germany, Finland,
Czech Republic, Italy, Spain, Portugal, Poland, Ire-
land, Belgium, France, Netherlands, United King-
dom, Slovakia, Norway. The publication was writ-
ten at VIRTUAL VEHICLE Research Center in Graz
6
https://www.asam.net/
and partially funded by the COMET K2 – Compe-
tence Centers for Excellent Technologies Programme
of the Federal Ministry for Transport, Innovation and
Technology (bmvit), the Federal Ministry for Dig-
ital, Business and Enterprise (bmdw), the Austrian
Research Promotion Agency (FFG), the Province of
Styria and the Styrian Business Promotion Agency
(SFG).
REFERENCES
Blochwitz, T., Otter, M., Akesson, J., Arnold, M., Claus-
zlig, C., Elmqvist, H., Friedrich, M., Junghanns, A.,
Mauszlig, J., Neumerkel, D., Olsson, H., and Viel,
A. (2012). Functional mockup interface 2.0: The
standard for tool independent exchange of simula-
tion models. In Proceedings of the 9th International
MODELICA Conference, number 76, pages 173–184.
Link
¨
oping University Electronic Press.
Driesten, C. v. and Schaller, T. (2019). Overall approach to
standardize ad sensor interfaces: Simulation and real
vehicle. In Bertram, T., editor, Fahrerassistenzsysteme
2018, pages 47–55, Wiesbaden. Springer Fachmedien
Wiesbaden.
Elgharbawy, M., Schwarzhaupt, A., Scheike, G., Frey, M.,
and Gauterin, F. (2016). A generic architecture of
adas sensor fault injection for virtual tests. In 2016
IEEE/ACS 13th International Conference of Com-
puter Systems and Applications (AICCSA), pages 1–7.
Feilhauer, M. and H
¨
aring, J. (2016). A multi-domain simu-
lation approach to validate advanced driver assistance
systems. In 2016 IEEE Intelligent Vehicles Sympo-
sium (IV), pages 1179–1184.
Hanke, T., Hirsenkorn, N., Dehlink, B., Rauch, A.,
Rasshofer, R., and Biebl, E. (2015). Generic architec-
ture for simulation of adas sensors. In 2015 16th In-
ternational Radar Symposium (IRS), pages 125–130.
Krammer, M., Benedikt, M., Blochwitz, T., Alekeish, K.,
Amringer, N., Kater, C., Materne, S., Ruvalcaba,
R., Schuch, K., Zehetner, J., Damm-Norwig, M.,
Schreiber, V., Nagarajan, N., Corral, I., Sparber, T.,
Klein, S., and Andert, J. (2018). The distributed co-
simulation protocol for the integration of real-time
systems and simulation environments.
Krammer, M., Marko, N., and Benedikt, M. (2016). Inter-
facing real-time systems for advanced co-simulation -
the acosar approach. In STAF 2016: Software Tech-
nologies: Applications and Foundations.
Maurer, M. and Winner, H. (2013). Automotive Systems
Engineering. Springer Publishing Company, Incorpo-
rated.
Modelica (2018). FMI functional mockup interface. https:
//fmi-standard.org/. Accessed: 2018-08-24.
Schaermann, A., Rauch, A., Hirsenkorn, N., Hanke, T.,
Rasshofer, R., and Biebl, E. (2017). Validation of ve-
hicle environment sensor models. In 2017 IEEE Intel-
ligent Vehicles Symposium (IV), pages 405–411.
Schneider, S.-A. and Saad, K. (2018). Camera behav-
ioral model and testbed setups for image-based ADAS
functions. e & i Elektrotechnik und Informationstech-
nik, pages 1–7. issn: 1613-7620.
SIMULTECH 2019 - 9th International Conference on Simulation and Modeling Methodologies, Technologies and Applications
262