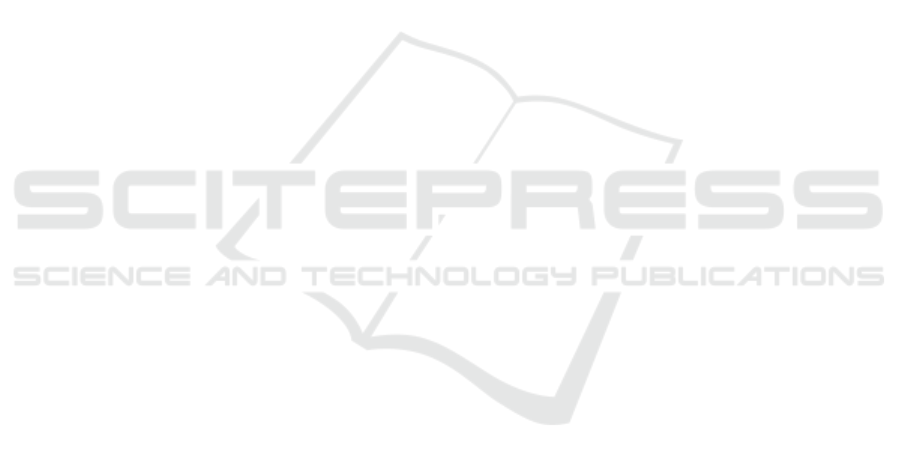
validation. This quasi-serial RobotArm desktop
model was subsequently rapid prototyped via 3D
printing. The parameters input into Cura for slicing of
the model have been outlined in Section 3.
The kinematic model was then derived for 2D planar
space via a closed loop vector method. These
kinematic equations needed to be validated and hence
an empirical versus analytical test approach was
implemented. The graphical empirical results were
obtained with the use of an equivalent SolidWorks
model of the physical RobotArm geometry. The
analytical results were obtained via the forward
kinematic equations outlined in Section 4. The results
were then tabulated in Section 5 and subsequently
compared. The results correlated extremely closely
well with a maximum error of less than 0.02%.
Future work looks to define the inverse kinematic
equations, develop a 3D workspace for a single
RobotArm, including singularities and non-
linearities. Further is to then introduce several of
these RobotArms into the same workspace for
collaborative applications. A Graphical User
Interface (GUI) will be developed in order to control
and monitor the final platform.
REFERENCES
Carricato, M. & Parenti-Castelli, V. 2002. Singularity-Free
Fully-Isotropic Translational Parallel Mechanisms. The
International Journal of Robotics Research, 21, 161-
174.
Issa, A., Aqel, M. O. A., Albelbeisi, M. M., , M. O. &
Mortaja, M. A. Palletizing Manipulator Design and
Control Using Arduino and MATLAB. 2017
International Conference on Promising Electronic
Technologies (ICPET), 16-17 Oct. 2017 2017. 60-65.
Klimchik, A., Magid, E., Caro, S., Waiyakan, K. &
Pashkevich, A. Stiffness of serial and quasi-serial
manipulators: comparison analysis. MATEC Web of
Conferences, 2016. EDP Sciences, 02003.
Klimchik, A. & Pashkevich, A. 2017. Serial vs. quasi-serial
manipulators: Comparison analysis of elasto-static
behaviors. Mechanism and Machine Theory, 107, 46-
70.
Liu, X.-J., Li, J. & Zhou, Y. 2015. Kinematic optimal
design of a 2-degree-of-freedom 3-parallelogram planar
parallel manipulator. Mechanism and Machine Theory,
87, 1-17.
Liu, Z., Wu, J. & Wang, D. 2019. An engineering-oriented
motion accuracy fluctuation suppression method of a
hybrid spray-painting robot considering dynamics.
Mechanism and Machine Theory, 131, 62-74.
Pandilov, Z. & Dukovski, V. 2012. Parallel kinematics
machine tools: Overview-from history to the future.
Annals of the Faculty of Engineering Hunedoara, 10,
111.
Pandremenos, J., Doukas, C., Stavropoulos, P. &
CHRYSSOLOURIS, G. 2011. Machining with robots:
a critical review. Proceedings of DET2011, 1-9.
Shaik, A. A., Tlale, N. S. & Bright, G. 2012. A new hybrid
machine design for a 6 DOF industrial robot arm.
Sun, L. & Fang, L. 2018. An approximation method for
stiffness calculation of robotic arms with hybrid open-
and closed-loop kinematic chains. Advances in
Mechanical Engineering, 10, 1687814018761297.
Tao, Y., Chen, F. & Xiong, H. 2014. Kinematics and
Workspace of a 4-DOF Hybrid Palletizing Robot.
Advances in Mechanical Engineering, 6, 125973.
Tobler, F. 2016. RobotArm [Online]. Thingyverse.com.
Available:
https://www.thingiverse.com/thing:1718984 [Accessed
15/9/2018 2018].
Xiao, W., Huan, J. & Dong, S. 2014. A STEP-compliant
Industrial Robot Data Model for robot off-line
programming systems. Robotics and Computer-
Integrated Manufacturing, 30, 114-123.
Yeshmukhametov, A., Kalimoldayev, M., Mamyrbayev, O.
& Amirgaliev, Y. Design and kinematics of
serial/parallel hybrid robot. Control, Automation and
Robotics (ICCAR), 2017 3rd International Conference
on, 2017. IEEE, 162-165.
Quasi-serial Manipulator for Advanced Manufacturing Systems
305