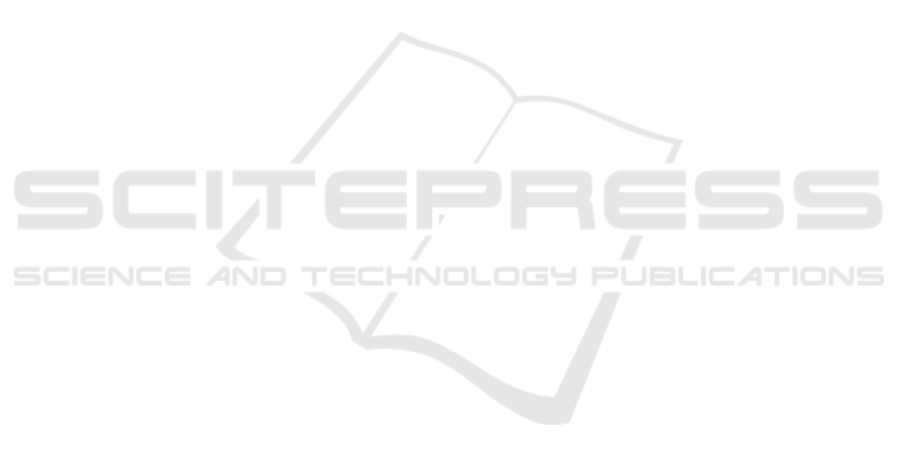
sium on Operating Systems Design and Implementa-
tion ({OSDI} 16), pages 265–283.
Adnan, N. H. and Mahzan, T. (2015). Gesture recognition
based on human grasping activities using pca-bmu.
Gesture, 6(11).
Awe, O., Mengistu, R., and Sreedhar, V. (2017). Smart
trash net: waste localization and classification. arXiv
preprint.
Bostelman, R., Hong, T., and Marvel, J. (2016). Survey
of research for performance measurement of mobile
manipulators. Journal of Research of the National In-
stitute of Standards and Technology, 121:342–366.
Chitta, S., Sucan, I., and Cousins, S. (2012). Moveit![ros
topics]. IEEE Robotics & Automation Magazine,
19(1):18–19.
Chu, K., Zhang, Q., Han, H., Xu, C., Pang, W., Ma, Y.,
Sun, N., and Li, W. (2017). A systematic review and
meta-analysis of nonpharmacological adjuvant inter-
ventions for patients undergoing assisted reproductive
technology treatment. International Journal of Gyne-
cology & Obstetrics, 139(3):268–277.
Chu, Y., Huang, C., Xie, X., Tan, B., Kamal, S., and Xiong,
X. (2018). Multilayer hybrid deep-learning method
for waste classification and recycling. Computational
Intelligence and Neuroscience, 2018.
Cruz, L., Lucio, D., and Velho, L. (2012). Kinect and rgbd
images: Challenges and applications. In 2012 25th
SIBGRAPI Conference on Graphics, Patterns and Im-
ages Tutorials, pages 36–49. IEEE.
Dai, W., Sun, Y., and Qian, X. (2013). Functional analysis
of grasping motion. In 2013 IEEE/RSJ International
Conference on Intelligent Robots and Systems, pages
3507–3513. IEEE.
Donoho, D. L. and Grimes, C. (2003). Hessian eigen-
maps: Locally linear embedding techniques for high-
dimensional data. Proceedings of the National
Academy of Sciences, 100(10):5591–5596.
Feng, C., Taguchi, Y., and Kamat, V. R. (2014). Fast plane
extraction in organized point clouds using agglomera-
tive hierarchical clustering. In Robotics and Automa-
tion (ICRA), 2014 IEEE International Conference on,
pages 6218–6225. IEEE.
Gundupalli, S. P., Hait, S., and Thakur, A. (2017). A review
on automated sorting of source-separated municipal
solid waste for recycling. Waste management, 60:56–
74.
LeCun, Y., Bottou, L., Bengio, Y., Haffner, P., et al. (1998).
Gradient-based learning applied to document recogni-
tion. Proceedings of the IEEE, 86(11):2278–2324.
Lei, Q., Chen, G., and Wisse, M. (2017). Fast grasping of
unknown objects using principal component analysis.
AIP Advances, 7(9):095126.
Lu, Y. (2017). Industry 4.0: A survey on technologies, ap-
plications and open research issues. Journal of Indus-
trial Information Integration, 6:1–10.
Masuta, H., Motoyoshi, T., Sawai, K. K. K., and Oshima,
T. (2016). Plane extraction using point cloud data for
service robot. In Computational Intelligence (SSCI),
2016 IEEE Symposium Series on, pages 1–6. IEEE.
Mittal, G., Yagnik, K. B., Garg, M., and Krishnan, N. C.
(2016). Spotgarbage: smartphone app to detect
garbage using deep learning. In Proceedings of the
2016 ACM International Joint Conference on Per-
vasive and Ubiquitous Computing, pages 940–945.
ACM.
Nguyen, A. and Le, B. (2013). 3d point cloud segmentation:
A survey. In RAM, pages 225–230.
Ni, H., Lin, X., and Zhang, J. (2017). Classification of als
point cloud with improved point cloud segmentation
and random forests. Remote Sensing, 9(3):288.
Nurunnabi, A., Belton, D., and West, G. (2012). Robust
segmentation in laser scanning 3d point cloud data.
In Digital Image Computing Techniques and Appli-
cations (DICTA), 2012 International Conference on,
pages 1–8. IEEE.
Rad, M. S., von Kaenel, A., Droux, A., Tieche, F., Ouer-
hani, N., Ekenel, H. K., and Thiran, J.-P. (2017). A
computer vision system to localize and classify wastes
on the streets. In International Conference on Com-
puter Vision Systems, pages 195–204. Springer.
Rusu, R. B. and Cousins, S. (2011). 3d is here: Point cloud
library (pcl). In Robotics and automation (ICRA),
2011 IEEE International Conference on, pages 1–4.
IEEE.
Simonyan, K. and Zisserman, A. (2014). Very deep con-
volutional networks for large-scale image recognition.
arXiv preprint arXiv:1409.1556.
ten Pas, A., Gualtieri, M., Saenko, K., and Platt, R. (2017).
Grasp pose detection in point clouds. The Interna-
tional Journal of Robotics Research, 36(13-14):1455–
1473.
Tenenbaum, J. B., De Silva, V., and Langford, J. C. (2000).
A global geometric framework for nonlinear dimen-
sionality reduction. science, 290(5500):2319–2323.
Thilagamani, S. and Moorthi, S. (2011). A survey on image
segmentation through clustering. International Jour-
nal of Research and Reviews in Information Sciences,
1.
Vo, A.-V., Truong-Hong, L., Laefer, D. F., and Bertolotto,
M. (2015). Octree-based region growing for point
cloud segmentation. ISPRS Journal of Photogramme-
try and Remote Sensing, 104:88–100.
Xiao, J., Zhang, J., Adler, B., Zhang, H., and Zhang, J.
(2013). Three-dimensional point cloud plane seg-
mentation in both structured and unstructured en-
vironments. Robotics and Autonomous Systems,
61(12):1641–1652.
Zeng, A., Song, S., Yu, K., Donlon, E., Hogan, F. R., Bauz
´
a,
M., Ma, D., Taylor, O., Liu, M., Romo, E., Fazeli,
N., Alet, F., Dafle, N. C., Holladay, R., Morona, I.,
Nair, P. Q., Green, D., Taylor, I., Liu, W., Funkhouser,
T. A., and Rodriguez, A. (2017). Robotic pick-and-
place of novel objects in clutter with multi-affordance
grasping and cross-domain image matching. CoRR,
abs/1710.01330.
ICINCO 2019 - 16th International Conference on Informatics in Control, Automation and Robotics
622