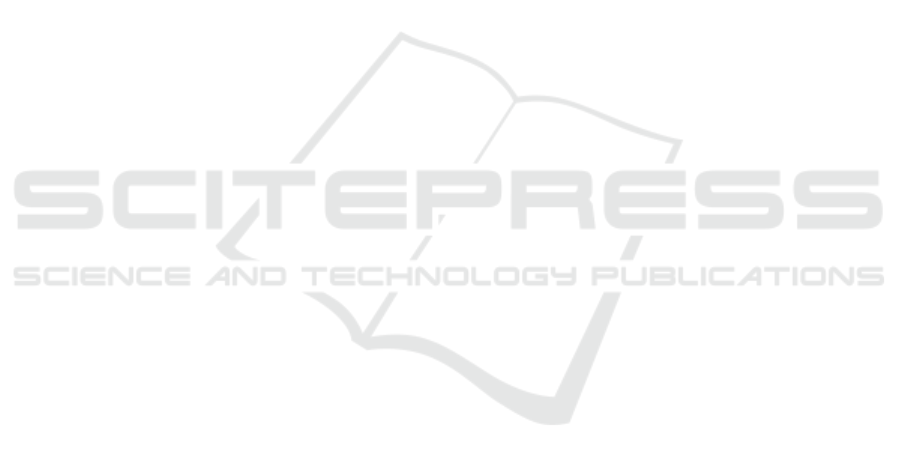
tificial Intelligence, 71(1):43–100.
Bechon, P., Barbier, M., Infantes, G., Lesire, C., and Vidal,
V. (2014). Hipop: Hierarchical partial-order planning.
In STAIRS, pages 51–60.
Bercher, P., H
¨
oller, D., Behnke, G., and Biundo, S. (2016).
More than a name? on implications of preconditions
and effects of compound htn planning tasks. In ECAI,
pages 225–233.
Bryan, A., Ko, J., Hu, S., and Koren, Y. (2007). Co-
evolution of product families and assembly systems.
CIRP Annals, 56(1):41–44.
Cashmore, M., Fox, M., Long, D., and Magazzeni, D.
(2016). A compilation of the full PDDL+ language
into SMT. In AAAI Workshop: Planning for Hybrid
Systems.
Castillo, L., Fern
´
andez-Olivares, J., Garcia-Perez, O., and
Palao, F. (2006). Efficiently handling temporal knowl-
edge in an htn planner. In ICAPS, pages 63–72.
Castillo, L., Fern
´
andez-Olivares, J., and Gonzalez, A.
(2003). Integrating hierarchical and conditional plan-
ning techniques into a software design process for au-
tomated manufacturing. In ICAPS.
Dornhege, C., Eyerich, P., Keller, T., Tr
¨
ug, S., Brenner,
M., and Nebel, B. (2009). Semantic attachments for
domain-independent planning systems. In Conf. on
Automated Planning and Scheduling.
Erol, K., Hendler, J., and Nau, D. (1994). Htn planning:
Complexity and expressivity. In AAAI, volume 94,
pages 1123–1128.
Fernandez-Gonzalez, E., Williams, B., and Karpas, E.
(2018). Scottyactivity: Mixed discrete-continuous
planning with convex optimization. Artificial Intel-
ligence Research, 62:579–664.
Fox, M. and Long, D. (2002). Pddl+: Modeling continuous
time dependent effects. In Int. NASA Workshop on
Planning and Scheduling for Space, volume 4.
Garrett, C., Lozano-P
´
erez, T., and Kaelbling, L. (2015).
Ffrob: An efficient heuristic for task and motion plan-
ning. In Algorithmic Foundations of Robotics XI,
pages 179–195. Springer.
Gateau, T., Lesire, C., and Barbier, M. (2013). Hidden:
Cooperative plan execution and repair for heteroge-
neous robots in dynamic environments. In IROS,
pages 4790–4795. IEEE.
Georgievski, I. and Aiello, M. (2015). Htn planning:
Overview, comparison, and beyond. Artificial Intel-
ligence, 222:124–156.
Goldman, R. (2006). Durative planning in htns. In ICAPS,
pages 382–385.
Helmert, M. (2006). The fast downward planning system.
Artificial Intelligence Research, 26:191–246.
Hitomi, K. (2017). Manufacturing Systems Engineering:
A Unified Approach to Manufacturing Technology,
Production Management and Industrial Economics.
Routledge.
Hu, S., Ko, J., Weyand, L., ElMaraghy, H., Lien, T., Koren,
Y., Bley, H., Chryssolouris, G., Nasr, N., and Shpi-
talni, M. (2011). Assembly system design and oper-
ations for product variety. CIRP Annals, 60(2):715–
733.
Kambhampati, S., Mali, A., and Srivastava, B. (1998). Hy-
brid planning for partially hierarchical domains. In
AAAI/IAAI, pages 882–888.
Kast, B., Albrecht, S., Feiten, W., and Zhang, J. (2019).
Bridging the gap between semantics and control for
industry 4.0 and autonomous production. In CASE.
IEEE.
Kaufman, S., Wilson, R., Jones, R., Calton, T., and Ames,
A. (1996). The archimedes 2 mechanical assembly
planning system. In ICRA, volume 4, pages 3361–
3368. IEEE.
Lozano-P
´
erez, T. and Kaelbling, L. (2014). A constraint-
based method for solving sequential manipulation
planning problems. In IROS, pages 3684–3691. IEEE.
Marthi, B., Russell, S., and Wolfe, J. (2008). Angelic hier-
archical planning: Optimal and online algorithms. In
ICAPS, pages 222–231.
McDermott, D., Ghallab, M., Howe, A., Knoblock, C.,
Ram, A., Veloso, M., Weld, D., and Wilkins, D.
(1998). Pddl - the planning domain definition lan-
guage. The AIPS-98 Planning Competition Comitee.
Molineaux, M., Klenk, M., and Aha, D. (2010). Planning in
dynamic environments: extending htns with nonlinear
continuous effects. In Conf. on Artificial Intelligence,
pages 1115–1120. AAAI Press.
Nau, D., Au, T.-C., Ilghami, O., Kuter, U., Murdock, J., Wu,
D., and Yaman, F. (2003). Shop2: An htn planning
system. Artificial Intelligence Research, 20:379–404.
Piotrowski, W., Fox, M., Long, D., Magazzeni, D., and
Mercorio, F. (2016). Heuristic planning for hybrid
systems. In Conf. on Artificial Intelligence, pages
4254–4255. AAAI Press.
Schattenberg, B. (2009). Hybrid planning and scheduling.
PhD thesis, University of Ulm, Germany.
Schmitt, P., Neubauer, W., Feiten, W., Wurm, K.,
v. Wichert, G., and Burgard, W. (2017). Optimal,
sampling-based manipulation planning. In ICRA,
pages 3426–3432. IEEE.
Schmitz, S., Schluetter, M., and Epple, U. (2009). Au-
tomation of automation — definition, components and
challenges. In Conf. on Emerging Technologies &
Factory Automation. IEEE.
Srivastava, S., Fang, E., Riano, L., Chitnis, R., Russell, S.,
and Abbeel, P. (2014). Combined task and motion
planning through an extensible planner-independent
interface layer. In ICRA, pages 639–646. IEEE.
Thomas, U. and Wahl, F. (2010). Assembly planning and
task planning—two prerequisites for automated robot
programming. In Robotic Systems for Handling and
Assembly, pages 333–354. Springer.
Toussaint, M. (2015). Logic-geometric programming: An
optimization-based approach to combined task and
motion planning. In IJCAI, pages 1930–1936.
Young, R. M., Pollack, M., and Moore, J. (1994). Decom-
position and causality in partial-order planning. In
AIPS, pages 188–194.
ICINCO 2019 - 16th International Conference on Informatics in Control, Automation and Robotics
260