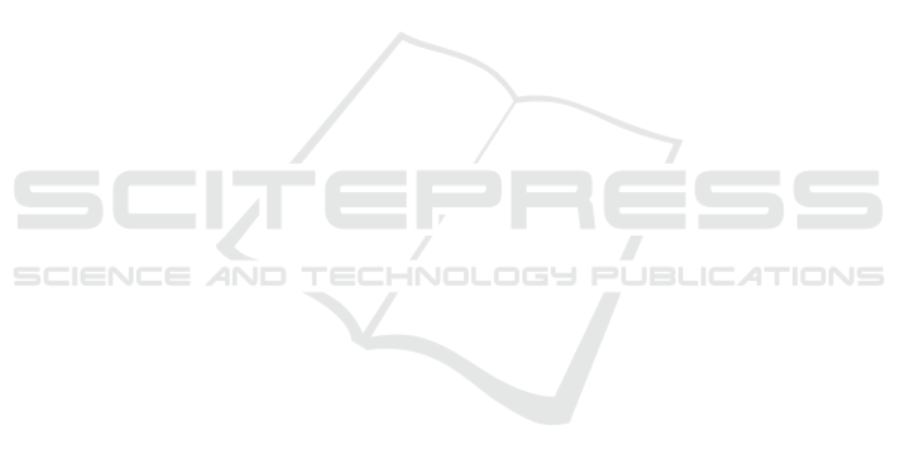
mits to address in a common framework, several kinds
of mobile robots, thanks to a backstepping approach.
A desired orientation is first computed, allowing the
robot to converge to the desired distance from the
structure to be followed, whatever its configuration
(skid-steering, car-like, or four-wheel-steering). This
is achieved using the derivative with respect to curvi-
linear distance, in order to have a behaviour which
is independent from the velocity. Beyond the con-
vergence of the lateral error, this first step also per-
mits to detect and avoid collisions, by considering
the minimal and maximal admissible orientation, in-
side the motion control framework. Moreover, this
desired orientation is also used to compute a speed
limitation for skid-steering mobile robots, allowing
to achieve harsh manoeuvres. The second step con-
sists in the regulation of the orientation of the robot
to the desired one computed in the first step. For
skid-steering robots, this is achieved relying on a
model with derivatives w.r.t. time, allowing them
to rotate even with a null longitudinal speed in or-
der to enhance the manoeuvrability. For four-wheel-
steering mobile robots (and consequently car-like mo-
bile robots), a strategy based on the curvilinear ab-
scissa is proposed, adding two steps in the approach.
The front steering angle is first controlled to impose
that the orientation
˜
θ
2
(robot orientation increased by
the rear steering angle) converges to the desired one
and next the rear steering angle regulates the actual
robot orientation to increase the manoeuvrability or to
ensure the parallelism of the robot with respect to the
structure to be followed, depending on the situation.
Such an approach permits to regulate independently
the position and the orientation of the robot.
The effectiveness of the proposed algorithm has
been investigated through full scale experiments,
showing its robustness and efficiency in various con-
ditions, with different kinds of structures to be fol-
lowed (indoor furnitures and vegetations) and with
several kinds of robots. In particular, this algo-
rithm has been successfully tested on a 25-kg skid-
steering robot and on a 520-kg four-wheel-steering
robot, showing the generality of the proposed con-
trol law(s). This opens the way to achieve fully au-
tonomous agricultural tasks, especially in orchard or
vineyard, for spraying application. A new robot, able
to carry out an automated sprayer is indeed under de-
velopment to test such an approach in fully working
conditions.
ACKNOWLEDGMENT
This work has been sponsored by the French Na-
tional Research Agency under the grant number
ANR-14-CE27-0004 attributed to Adap2E project
(adap2e.irstea.fr). It has also been sponsored by
the French government research program ”Investisse-
ments d’Avenir” through the IDEX-ISITE initiative
16-IDEX-0001 (CAP 20-25), the IMobS3 Labora-
tory of Excellence (ANR-10-LABX-16-01) and the
RobotEx Equipment of Excellence (ANR-10-EQPX-
44). This research was also financed by the European
Union through the Regional Competitiveness and
Employment program -2014-2020- (ERDF – AURA
region) and by the AURA region.
REFERENCES
Astrand, B. and Baerveldt, A.-J. (2005). A vision based
row-following system for agricultural field machinery.
Mechatronics, 15(2):251 – 269.
Bayar, G., Bergerman, M., Koku, A. B., and Konukseven,
E. I. (2015). Localization and control of an au-
tonomous orchard vehicle. Computers and Electron-
ics in Agriculture, 115:118 – 128.
Bergerman, M., Billingsley, J., Reid, J., and Van Henten,
E. (2016). Robotics in Agriculture and Forestry. In
Springer Handbook of Robotics, pages 1463–1492.
Springer International Publishing.
Blackmore, S. (2016). Towards robotic agriculture. In SPIE
Commercial+ Scientific Sensing and Imaging, pages
986603–986603. International Society for Optics and
Photonics.
Cariou, C., Lenain, R., Thuilot, B., and Martinet, P. (2010).
Autonomous maneuver of a farm vehicle with a trailed
implement: motion planner and lateral-longitudinal
controllers. In IEEE International Conference on,
Robotics and Automation (ICRA), pages 3819–3824.
Cherubini, A. and Chaumette, F. (2013). Visual naviga-
tion of a mobile robot with laser-based collision avoid-
ance. The International Journal of Robotics Research,
32(2):189–205.
D’Andr
´
ea-Novel, B., Campion, G., and Bastin, G. (1995).
Control of nonholonomic wheeled mobile robots by
state feedback linearization. The International journal
of robotics research, 14(6):543–559.
Deremetz, M., Lenain, R., Couvent, A., Cariou, C., and
Thuilot, B. (2017). Path tracking of a four-wheel steer-
ing mobile robot: A robust off-road parallel steering
strategy. In European Conference on Mobile Robots
(ECMR), pages 1–7.
Lenain, R., Deremetz, M., Braconnier, J.-B., Thuilot, B.,
and Rousseau, V. (2017). Robust sideslip angles ob-
server for accurate off-road path tracking control. Ad-
vanced Robotics, 31(9):453–467.
Marmoiton, F. and Slade, M. (2016). Toward Smart Au-
tonomous Cars. In Intelligent Transportation Systems:
ICINCO 2019 - 16th International Conference on Informatics in Control, Automation and Robotics
112