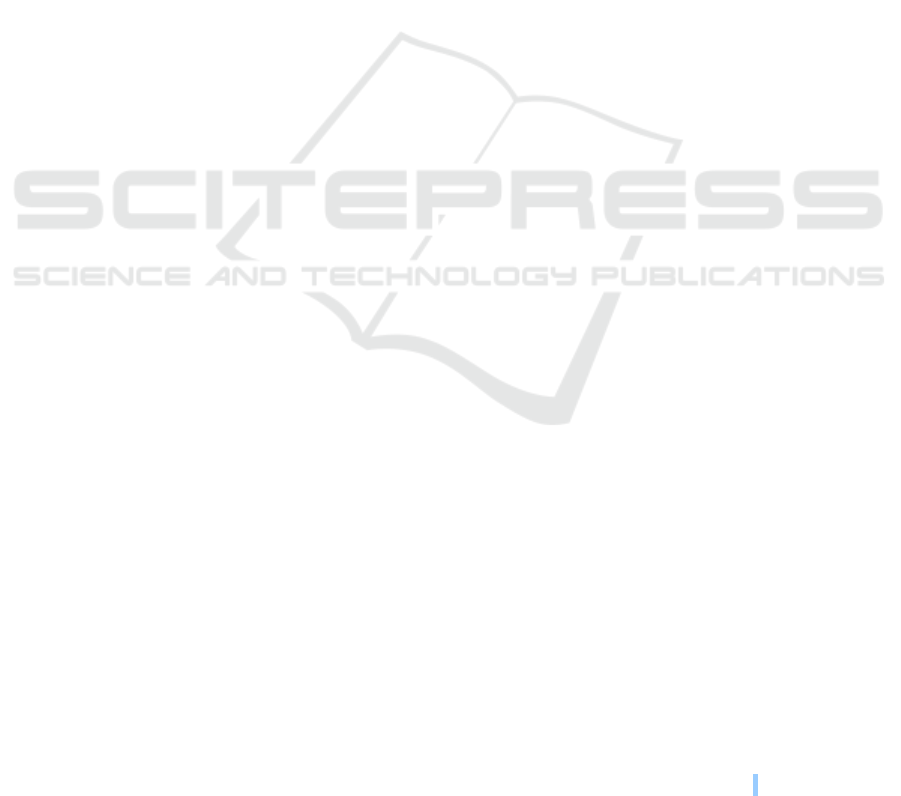
presented in a compact form. This equation is then
used to derive the kinematics equations in several
useful forms such as companion, actuation,
optimization and control forms. The proposed unified
approach can be applied to various robots, including
any combination of propulsion such as hybrid
walking/rolling, mobile manipulators and Stewart-
type platforms. A software package has been
developed to implement the kinematics modelling and
optimization in its various forms. The software
includes animation of the robot motion. The program
has been applied to a hybrid walking/rolling robot for
traversing on bumpy terrain. Various results
demonstrate the satisfactory performance of the
systems in path following, balancing and tip-over
avoidance.
REFERENCES
Bellicoseo, C.D., Jenelten, F., Gehring, C. and Hutter, M.,
2018. Dynamic locomotion through online nonlinear
motion optimization for quadruped robots,” IEEE
Robotics and Automation Letters, vol. 3, no. 3, pp.
2261-2268.
Cordes, F., Dettmann, A., and Kirchner, A., 2011.
Locomotion modes for a hybrid wheeled-legplanetary
rover, in Proc. of IEEE Int. Conf. on Robotics and
Biomimetics, vol. 1, pp. 654–659, 2004.
Cully, A., Clune, J., Tarapore, D., and Mouret, J-B., 2015.
Robots that can adapt like animals,” Nature volume521,
pp. 503–507.
Gonzales de Santos, P., Estremera, J., and Garcia, E., 2003.“
The SILO4- A true walking robot for comparative study
of walking machines techniques. IEEE Robot. Autom.
Mag., vol. 10, no. 4, pp. 23- 32.
Grand, C. BenAmar, F., Plumet, F. and Bidaud, P., 2000.
Stability control of a wheel-legged mini-rover, in Proc
of Int. Conf. on Climbing and Walking Robots.
Fujita, T., and Sasaki, T., 2017. “Development of hexapod
tracked mobile robot and its hybrid locomotion with
object-carrying,” IEEE Int. Symp. on Robotics and
Intelligent Sensors.
Iagnemma, K., Rzepniewski, A., Dubowsky, S.,
Huntsberger, T., Pirjanian, P., Schenker, P., 2000.
Mobile Robot Kinematic Reconfigurability for Rough-
Terrain,” Proceedings of the SPIE Symposium on
Sensor Fusion and Decentralized Control in Robotic
Systems III.
Jehanno, J-M., Cully, A., Grand, C., and Mouret, J-B., 2014.
“Design of a wheel-legged hexapod robot for creative
adaptation,” World Scientific Publishing, vol. 20, no. 6.
Kelly, A. and Seegmiller, N. 2015 “Recursive Kinematic
Propagation for Wheeled Mobile Robots”, vol. 34, no.
3, Int. J. Robotics Research. .
Kelly, A., 2012 “A vector algebra formulation of mobile
robot velocity kinematics,” Proc. 2012 Int. Conf. Field
and Service Robots.
Muir, P.F., and Neuman, C. P., 1991. “Kinematic modeling
of wheeled mobile robots,” J. Robotic Systems vol. 4, no.
2, pp. 281–340.
Nakamura, N., 1991. Advanced Robotics-Redundancy and
Optimization, Chapter 4, Addison-Wesley.
Rajagopalan, R., 1997 “A generic kinematic formulation for
wheeled mobile robots,” Journal of Robotic Systems
vol. 14, no. 2, pp. 77–91.
Shkolnik, A. and Tedrake, R. 2007. “Inverse Kinematics for
a Point-Foot Quadruped Robot with Dynamic
Redundancy Resolution”, 2007 IEEE Int. Conf.
Robotics and Automation Roma, Italy.
Siegwart, R., Lamon, P., Estier, T., Lauria, M., and Piguet,
R., 2002. “Innovative design for wheeled locomotion in
rough terrain,” Robotics and Autonomous Systems, vo.
40, pp. 151–162.
Shin, D.D., and K.H. Park, K.H., 2001. “Velocity kinematic
modeling for wheeled mobile robots,” Proc. 2001 IEEE
Int. Conf. Robotics and Automation, vol. 4. pp. 3516–
3522.
Smith, J., Sharf, I., and M. Trentini, M., 2006. Paw: a
Hybrid wheeled-leg robot, in Proc. of IEEE Int. Conf.
on Robotics and Automation.
Tarokh, M., McDermott, G., Hayati, S., and Hung, J., 1999
"Kinematic modeling of a high mobility Mars rover,"
Proc. IEEE Int. Conf. Robotics and Automation, pp.
992-998.
Tarokh, M. and McDermott, G., 2005. Kinematics
modelling and analysis of articulated rovers. IEEE
Trans. Robotics, vol. 21, no. 4, pp. 439-454.
Tarokh, M., G. McDermott and L. Mireles, 2006. Balance
control of articulated rovers with active Suspension.
Proc. 8th IFAC-IEEE Symposium on Robot Control:
Vol. FrP- 2.1-2, pp. 1-6. Bologna, Italy.
Tarokh, M., and McDermott, G., 2007. “A systematic
approach to kinematics modeling of high mobility
wheeled rovers,” Proc. IEEE Int. Conf. Robotics and
Automation, pp. 4905- 4910, Rome, Italy.
Tarokh, M., Ho, H.D., and A. Bouloubasis, A., 2013.
Systematic kinematics analysis and balance control of
high mobility rovers over rough terrain," J. Robotics and
Autonomous Systems, 61, 13-24.
Winkler, A.W., Farshidian, F., Pardo, D., Neunert, M., and
Buchli, J., 2017. “Fast Trajectory Optimization for
Legged Robots Using Vertex-Based ZMP Constraints,”
IEEE Robotics and Automation Letters, Vol. 2, No. 4,
pp.2201-2208.
Winkler, A.W., Bellicoso, C.D., Hutter, M. and J. Buchli, J.,
2018. “Gait and trajectory optimization for legged
systems through phased-based end-effector
parameterization,” IEEE Robotics and Automation
Letters, vol.3, no. 3, pp. 1560-1567.
Ylonen, S., and Halme, A., 2002. Further development and
testing of the hybrid locomotion of Workpartner robot,
in Proc of Int. Conf. on Climbing on Walking Robots
(CLAWAR).
Yuan, J., and S. Hirose, S., 2004. “Research on leg-wheel
hybrid stair- climbing robot,zero carrier,” in IEEE Int.
Conf. on Robotics and Biomimetics.
ICINCO 2019 - 16th International Conference on Informatics in Control, Automation and Robotics
122