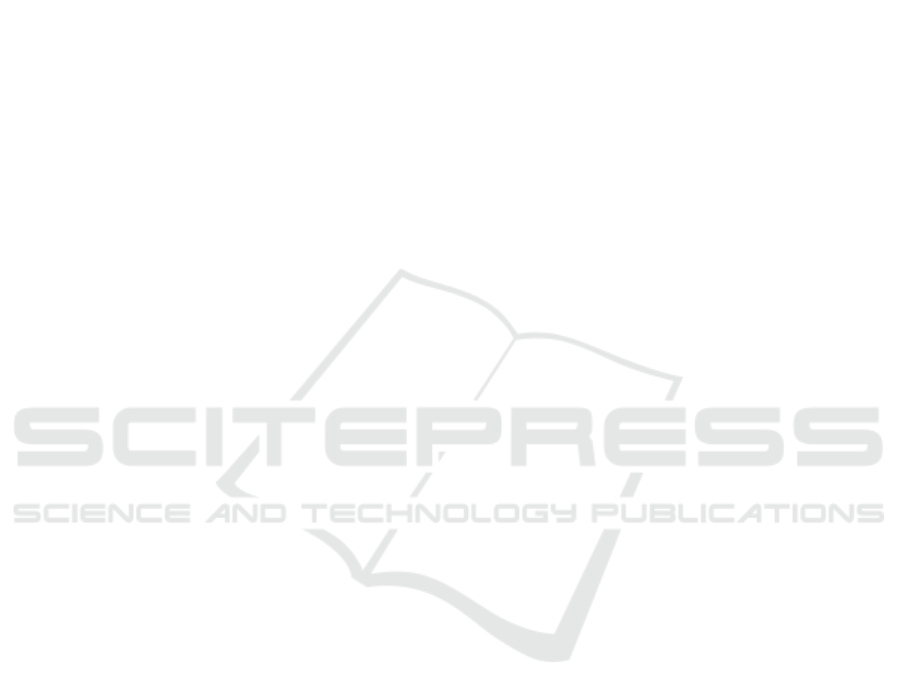
Computational Fluid Dynamics Model for Sensitivity Analysis and
Design of Flow Conditioners
V. Askari, D. Nicolas, M. Edralin and C. Jang
British Columbia Institute of Technology, School of Energy, Department of Mechanical Engineering,
3700 Willingdon Avenue, Burnaby, BC, Canada
Keywords: Computational Fluid Dynamics, Flow Conditioner, Swirling Flow, Flow Measurement, Flow Velocity Profile.
Abstract: Flow conditioners are used to measure flow rate more accurately. The sensitivity of flow measurement devices
to swirling flows and not fully developed flows are subjects of concerns to flowmeter manufacturers as well
as industries. Inaccurate flow measurement occurs in the presence of swirl flow and when the flow velocity
profile is not fully developed. Distorted profiles occur when the piping configuration upstream of the flow
measurement devices changes. Certain length of straight piping upstream of a flow meter is required to
achieve acceptable flow velocity profile for expected flow meter accuracy. In some installations, it is not
realistic to run lengths of piping to reach an acceptable flow velocity profile. Introducing flow conditioners
into the system reduces piping needed to reach fully developed flow and significantly weaken swirling flows.
In this study, a Computational Fluid Dynamics (CFD) model is developed and validated which is used to
investigate systematically the sensitivity of various parameters for perforated flow conditioners. Published
data and an experimental setup was used to verify the CFD model.
1 INTRODUCTION
Flow conditioners are used for homogenizing the
velocity profile, as well as removing swirls, created
by disturbances. Installations such as elbows and
double elbows, create swirls in the flow that can result
in inaccurate measurements by the flow meters. It is
essential the use of a flow conditioner to remove
disturbances in the flow, enabling proper
performance of the flow meter. Most flowmeters are
calibrated under conditions of fully developed flow.
Typically, without a flow conditioner it can take
approximately 30 L/D to obtain acceptable flow
profile for the measurement devices. Adding long
straight piping can be costly, and use up large
amounts of space. Using a flow conditioner
accelerates the development of flow profile as well
while also fading swirls. There are certain standards,
specifically ISO 5167, which define acceptable fully
developed flow, free from swirls and pulsations. The
standard states that, swirl-free conditions are
presumed “to exist when the swirl angle at all points
over the pipe cross-section is less than 2° (ISO,
2003).” The acceptable flow conditions exist when,
“at each point across the pipe cross-section, the ratio
of the local axial velocity to the maximum axial
velocity at the cross-section agrees to within ±5%
which would be achieved in swirl-free flow at the
same radial position at a cross-section located at the
end of a very long straight length L/D>100 of similar
pipe (ISO, 2003).”
The purpose of this project was to investigate the
performance of current perforated flow conditioners,
and to design and build a CFD model as a test bench
using academic COMSOL® Multiphysics software.
The CFD model is used to further investigate the
performance of the perforated flow conditioners and
sensitivity of the design parameters.
2 FLOW CONDITIONERS
There are various types of flow conditioners such as
those shown in Figure 1. However, for this study, two
perforated flow conditioners shown in Figure 2 are
examined. The perforated flow conditioner is chosen
over the other types due to its most used in industry
and ease of installation. Flow conditioners that
require long lengths of piping such as the tube-type
flow conditioner is effective in removing
disturbances in flow, but it is not ideal for
applications that are limited by space. In addition,
Askari, V., Nicolas, D., Edralin, M. and Jang, C.
Computational Fluid Dynamics Model for Sensitivity Analysis and Design of Flow Conditioners.
DOI: 10.5220/0007917401290140
In Proceedings of the 9th International Conference on Simulation and Modeling Methodologies, Technologies and Applications (SIMULTECH 2019), pages 129-140
ISBN: 978-989-758-381-0
Copyright
c
2019 by SCITEPRESS – Science and Technology Publications, Lda. All rights reserved
129