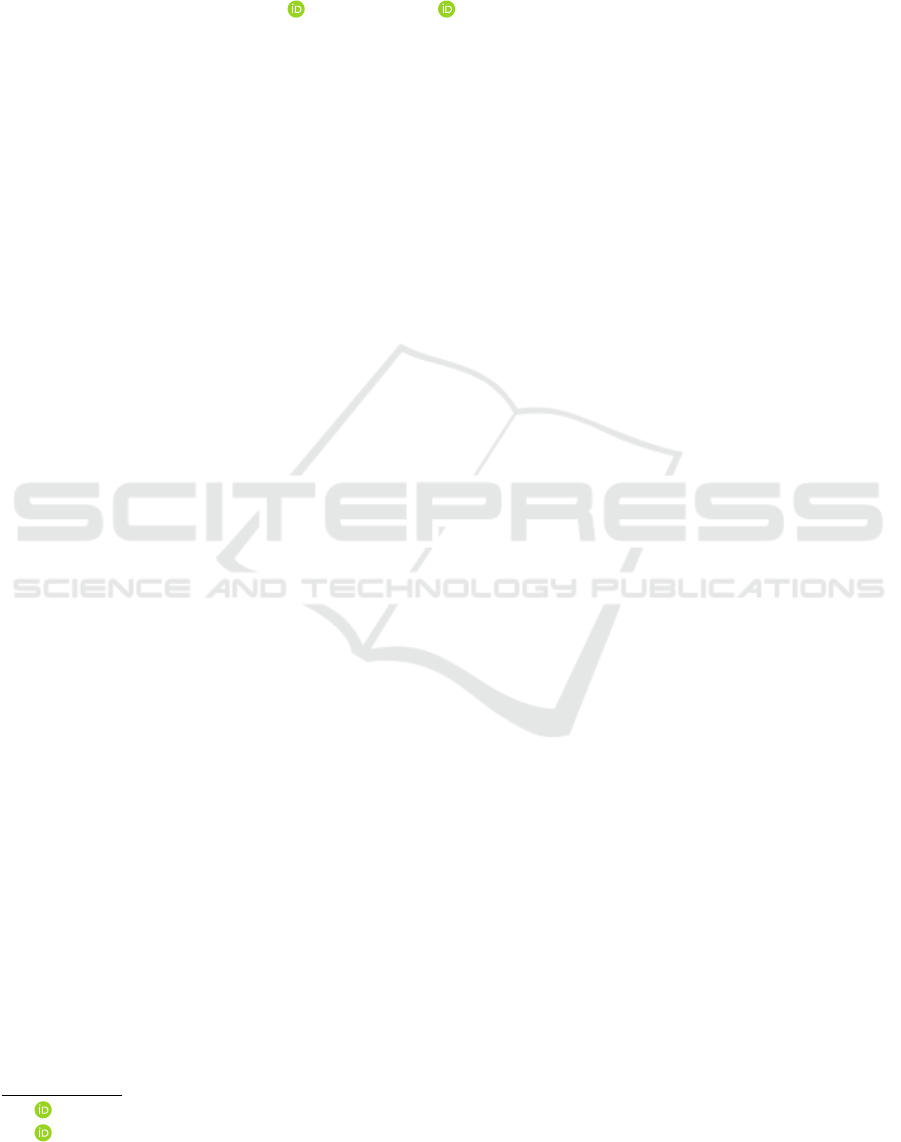
Control of an Industrial Dual-arm Robot in a Narrow Space where
Human Workers are Familiar with
Taeyong Choi
a
, Hyunmin Do
b
, Donil Park and Jinho Kyungk
Department of Robotics and Mechatronics, Korea Institute of Machinery and Materials, 156 Gajeongbuk-ro,
Yuseong-gu, Daejeon, South Korea
Keywords:
Dual-arm Robot, Redundant Robot Control, Manufacturing with Robot.
Abstract:
The industrial dual-arm robot is being developed. The developed industrial dual-arm robot aim to work with
human workers or to work instead of human workers. Redundancy by high degree of freedom caused by arm
and waist make robot movement difficult in the narrow space for human workers. Robot arms would take
unexpected posture without proper redundant control method. In particular elbows can cause hazard situation
by colliding with the environment or body of robot. Here novel method to control robot elbows is introduced.
It shows good performance without loss of the position precision of end-effectors. Also it does not require
high computing power, which make it useful for practical robot control. The proposed method is confirmed
by the simulation.
1 INTRODUCTION
Robotic manufacturing is a significant technology to
meet social needs. Population aging and decrease
of working age population are critical social issues
in the advanced country. In the advanced countries
human workers are reluctant to do repetitive physi-
cal work. Many production lines can be replaced by
robotic manufacturing with the current robotic tech-
nology. Industrial robot systems have been widely
used for manufacturing such as laser welding, transfer
and many repetitive processes.
However assembly works is still rely on human
beings. Assembly works is fundamental process in
the IT products production such as cellular phone,
laptop and etc.. It is also true that manufacturing
the trendy product such as cellular phone, automo-
bile, food and clothes is possible only by human
workers currently. The manufacturing system for
the small quantity and batch production is signifi-
cantly difficult with the automation equipment. Many
researchers have studied robotic manufacturing sys-
tems. (Hayakawa et al., 1998) employed a manipula-
tor to grasp the component parts during the assembly
process. These improved the assembly cell only in the
physical support aspect. (Kruger et al., 2009) intro-
a
https://orcid.org/0000-0002-4752-849X
b
https://orcid.org/0000-0002-2588-0572
duced the examples of human-machine cooperation
for assembly lines. However, there are no concrete-
ness methods in it. (Morioka and Sakakibara, 2010)
introduced new cell production assembly system with
human-robot cooperation. However there have been
no practical improvement yet.
Conventional industrial robot such as the serial
robot has only one arm. In case of serial robot, 6
degrees of freedom (DOF) commonly used to posi-
tion the end-effector of robot to exact position with
orientation. However, they have limitation to replace
human worker because of their low DOF and one arm
structure. Human has many DOF including redundant
joints to be flexible for the complex work. Dual-arms
cooperate to handle more complex and handful object.
Recently, companies and researchers are trying to
develop novel manufacturing system with the indus-
trial dual-arm robot (IDAR). IDARs such as the mo-
toman of (Yaskawa, 2019), the yumi of (ABB, 2019)
and the others of (Smith et al., 2012), are becom-
ing upcoming technology for robotic manufacturing.
IDAR is distinguished with the humanoid-like service
robots by the factors of traditional industrial robot
performance indexes including high precision, high
velocity and accessories of a teaching pendant and
control box.
Most of IDARs have redundant joints unlike 6
DOF conventional manipulator. Some of them has
DOF more than 6 at each arms. Some of them have
Choi, T., Do, H., Park, D. and Kyungk, J.
Control of an Industrial Dual-arm Robot in a Narrow Space where Human Workers are Familiar with.
DOI: 10.5220/0007918003390344
In Proceedings of the 16th International Conference on Informatics in Control, Automation and Robotics (ICINCO 2019), pages 339-344
ISBN: 978-989-758-380-3
Copyright
c
2019 by SCITEPRESS – Science and Technology Publications, Lda. All rights reserved
339