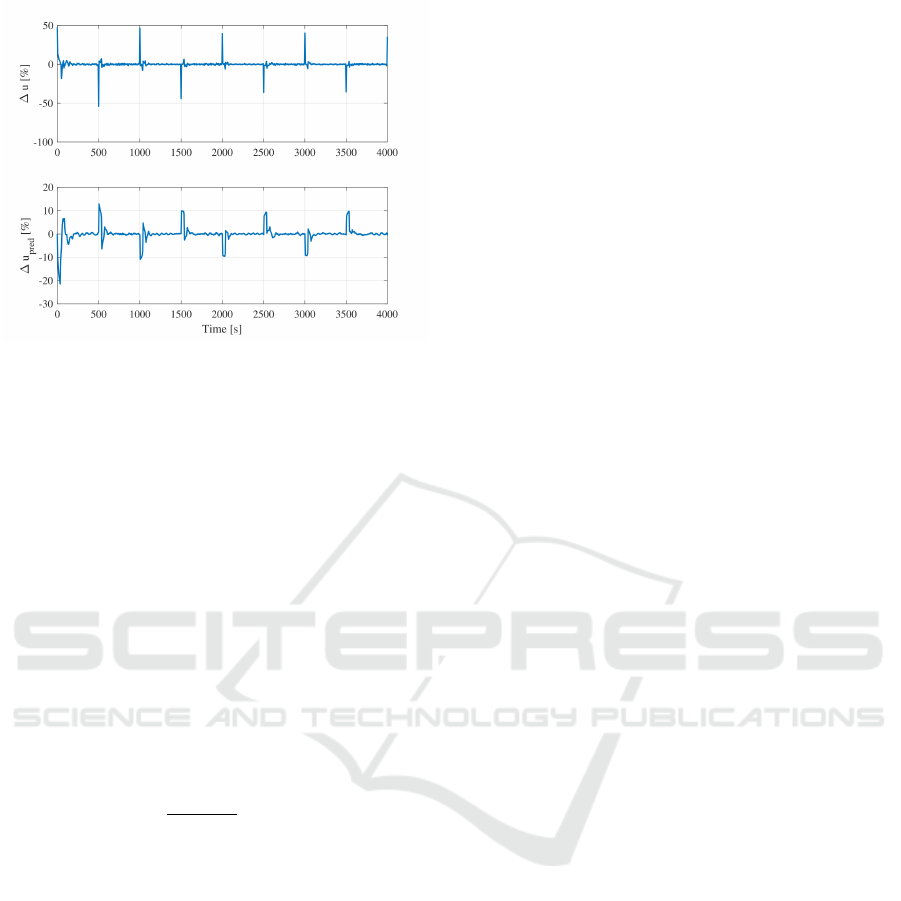
Figure 9: Comparison between ∆u(t) and ∆u
pred
(t).
terms and an overshoot is occurred. In contrast, the
derivative term predicts a future error and calculate
an input which reduces the overshoot based on the es-
timated error. The derivative term predicts a future
error under the assumption that the error is a propor-
tional function. However, the assumption is unrealis-
tic, and a large derivative gain sometimes causes prob-
lems. In contrast, the predictive term of the predictive
PI controller is based on a Smith predictor when a
controlled object is first order. Therefore, the predic-
tive PI controller employs more advanced prediction
than the PID controller although the predictive and
derivative terms have the same role.
Next, the consideration above is checked using the
experimental result. The input signal calculated by
the predictive term is defined as:
u
pred
(t) =
z
−1
K
pred
∆
(z
−d
− 1)u(t). (47)
Fig. 9 shows a comparison between ∆u(t) and
∆u
pred
(t). According to Fig. 9, the prediction term
worked like a brake. For example, ∆u(t) was about
−50 at 1505 second to lower the temperature. In con-
trast, ∆u
pred
(t) was about 10 between 1505 and 1535
seconds. The 30 seconds between 1505 and 1535
mean the estimated dead-time, and the predictive term
tried to suppress a large input signal in the period.
Thus, the control result shows that the predictive term
has the same role as the derivative term.
6 CONCLUSIONS
In this paper, a discrete-time predictive PI controller
has been discussed, and a data-driven self-tuning de-
sign method has also been proposed. Features of the
proposed controller are summarized as follows:
• The proposed controller can realize fast rise time
for a system with long dead-time.
• Any system model is not required to calculate PI
gains.
• Only PI gains are tuned in an on-line manner.
The proposed control scheme has been evaluated by
some numerical and experimental examples. In par-
ticular, the role of the predictive term included in the
proposed controller has been mentioned using the ex-
perimental example.
REFERENCES
Airikka, P. (2014). Robust predictive pi controller tuning.
IFAC Proceedings Volumes, 47(3):9301 – 9306. 19th
IFAC World Congress.
Ashida, Y., Hayashi, K., Wakitani, S., and Yamamoto, T.
(2016). A novel approach in designing pid controllers
using closed-loop data. In 2016 American Control
Conference (ACC), pages 5308–5313.
Ashida, Y., Wakitani, S., and Yamamoto, T. (2017). Design
of an implicit self-tuning pid controller based on the
generalized output. In Proc. of the 20th IFAC World
Congress, pages 14511 – 14516.
Ashida, Y., Wakitani, S., and Yamamoto, T. (2019). De-
sign of a data-driven pi controller. In Proc. of the
2020 International Conference on Artificial Life and
Robotics.
Astrom, K. and Hagglund, T. (2005). Advanced PID Con-
trol. International Society of Automation, North Car-
olina.
Berner, J., Soltesz, K., Hagglund, T., and Astrom, K.
(2018). An experimental comparison of pid auto-
tuners. Control Engineering Practice, 73:124–1133.
Bialkowski, W. (1993). Dreams versus reality: a view from
both sides of the gap: manufacturing excellence with
come only through engineering excellence. Pulp &
Paper Canada, 94:19–27.
Campestrini, L., Eckhard, D., Chia, L. A., and Boeira, E.
(2016). Unbiased mimo vrft with application to pro-
cess control. Journal of Process Control, 39:35 – 49.
Campi, M., Lecchini, A., and Savaresi, S. (2002). Virtual
reference feedback tuning: a direct method for the de-
sign of feedback controllers. Automatica, 38(8):1337
– 1346.
Gallego, A. J., Merello, G. M., Berenguel, M., and Cama-
choa, E. F. (2019). Gain-scheduling model predictive
control of a fresnel collector field. Control Engineer-
ing Practice, 82:1–13.
Goodwin, G. C. and Sin, K. S. (1984). Adaptive Filtering
Prediction and Control. Prentice-Hall, Upper Saddle
River.
Hagglund, T. (1992). A predictive pi controller for pro-
cesses with long dead times. IEEE Control Systems
Magazine, 12(1):57–60.
ICINCO 2019 - 16th International Conference on Informatics in Control, Automation and Robotics
678