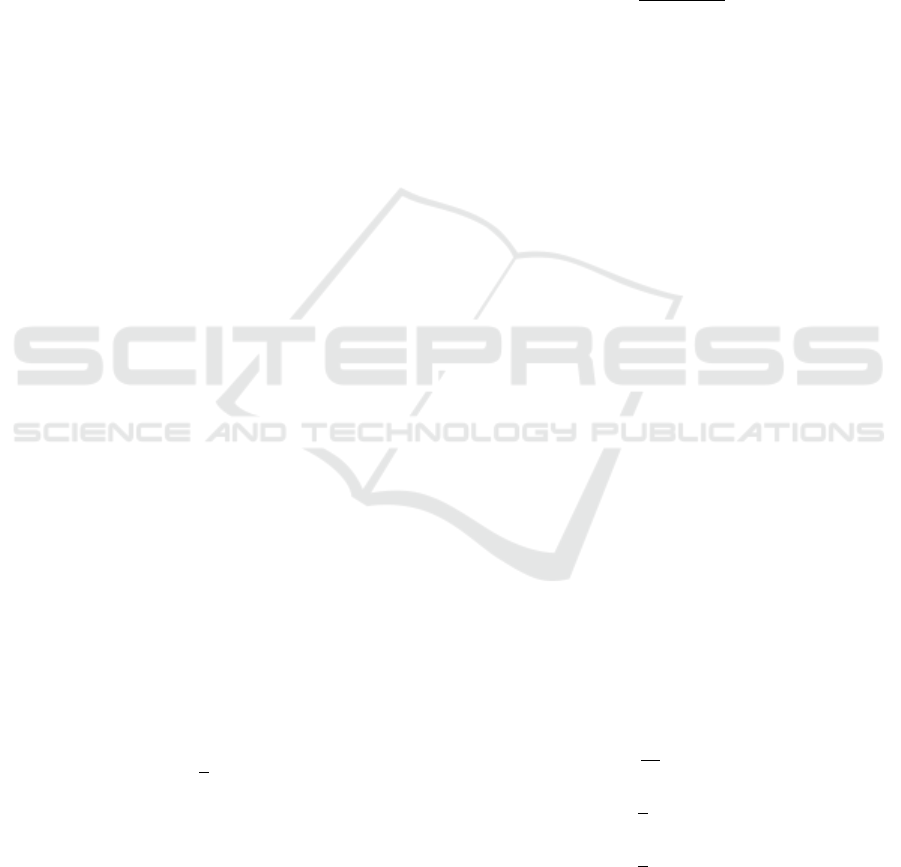
circle of radius d(s) representing the cross section of
the manipulator at the point s ∈ [0, 1] of its axis. Note
that d measures the thickness of the manipulator: in
octopus arm shaped manipulators, d is a decreasing
function. Choosing ρ(s) := πρ
v
d(s)
2
corresponds to
concentrate the mass of Ω(s) on its barycentre.
In our model, bending the manipulator determines
a compression/dilatation of the soft, elastic material
composing its body, for which we assume an uniform
yield point, i.e., the pointwise elastic forces must be
uniformly bounded by some F
max
in order to avoid
inelastic deformations. Now, due to the axial symme-
try, for every s ∈ [0,1], the maximal angular elastic
force in Ω(s) is attained on its boundary and it reads
F(s) = e|q
ss
|d(s), where e is the elastic constant of
the material. Therefore the constraint F(s) ≤ F
max
is
equivalent to the curvature constraint |q
ss
| ≤ ω, where
we set ω(s) = F
max
/(ed(s)).
2.1.1 On Mass Distributions with Exponential
Decay
In our numerical simulations, we assume ρ to have
an exponential decay. By the arguments above, this
choice is consistent with the case of three dimensional
structures whose thickness decays exponentially, and
it can be viewed as an interpolation of self-similar,
discrete structures (Lai et al., 2016a). In turn, self-
similarity assumption has several advantages from
both a practical and theoretical point of view. In-
deed, asking for a manipulator to be self-similar sim-
ply means to be composed by identical, rescaled mod-
ules. From a geometrical point of view, self-similarity
is a powerful assumption allowing, via fractal geome-
try techniques (Lai, 2012), for a detailed investigation
of inverse kinematics of the manipulator, see for in-
stance (Lai et al., 2016b).
2.2 Control Parameter Settings
We now show how to set the control parameters to
model a mechanical breakdown of the actuators.
We recall that the controlled elastic potential is
U[q,µ,u,ω] :=
1
2
µ(ωu − q
s
× q
ss
)
2
.
and the associated elastic force is
F[q,µ, u, ω] := −(Hq
⊥
ss
)
s
− (Hq
⊥
s
)
ss
where H = µ(ωu − q
s
× q
ss
). Clearly, to choose µ ≡ 0
is equivalent to neglect F, and it yields the uncon-
trolled dynamics:
ρq
tt
= (σq
s
)
s
− (Gq
ss
)
ss
. (3)
More generally, to set µ(s) = 0 for s ∈ [s
1
,s
2
] means
that the portion of q between [s
1
,s
2
] is uncontrolled:
it evolves according to (3) with (time dependent, con-
trolled) boundary conditions in q(s
1
,t) and q(s
2
,t).
We conclude with some remarks on how the con-
trol deactivation affects the equilibria of the system.
A general formula for the equilibria of (2) is provided
in (Cacace et al., 2018): if µ(1) = µ
s
(1) = 0, then the
signed curvature κ := q
s
×q
ss
of the (unique) equilib-
rium q of (2) is proportional to µ, precisely it satisfies
κ(s) = µ(s)
ω(s)u(s)
µ(s) + ε(s)
s ∈ (0,1).
In particular for µ ≡ 0 the equilibrium is given by
q(s,t) ≡ (0, −s) for all (s,t) ∈ [0, 1] × (0, T ). More
generally, if q is uncontrolled in [s
1
,s
2
], i.e., µ(s) = 0
for all s ∈ [s
1
,s
2
], then |q
ss
| = |κ(s)| = 0, that is the
corresponding portion of the device at the equilibrium
is arranged in a straight line.
3 THE REACHABILITY
OPTIMAL CONTROL
PROBLEM
In this section we address the problem of steering
the tip of the device –i.e., q(1,t)– to a target point
q
∗
∈ R
2
, using controls that optimize accuracy, steadi-
ness and energy consumption. In the framework of
optimal control theory, this problem can be restated
as a constrained minimization of a cost functional in-
volving:
- the tip-target distance: we want the tip to reach
and remain close to the target;
- a quadratic cost on the controls, that is we want to
force the device –precisely, its symmetry axis– to
bend as least as possible.
- the kinetic energy of the whole manipulator at fi-
nal time.
More formally, given q
∗
∈ R
2
and T, τ > 0, we want
to minimize the functional
J (q,u) =
1
2τ
Z
T
0
|q(1,t)− q
∗
|
2
dt
+
1
2
Z
T
0
Z
1
0
u
2
ds dt
+
1
2
Z
1
0
ρ(s)|q
t
(s,T )|
2
ds,
(4)
among all the controls u : [0,1] × [0, T ] → [−1, 1], and
subject to the symmetry axis dynamics (2). The first
two terms in J account respectively for the tip-target
distance and the quadratic cost on the controls, during
ICINCO 2019 - 16th International Conference on Informatics in Control, Automation and Robotics
84