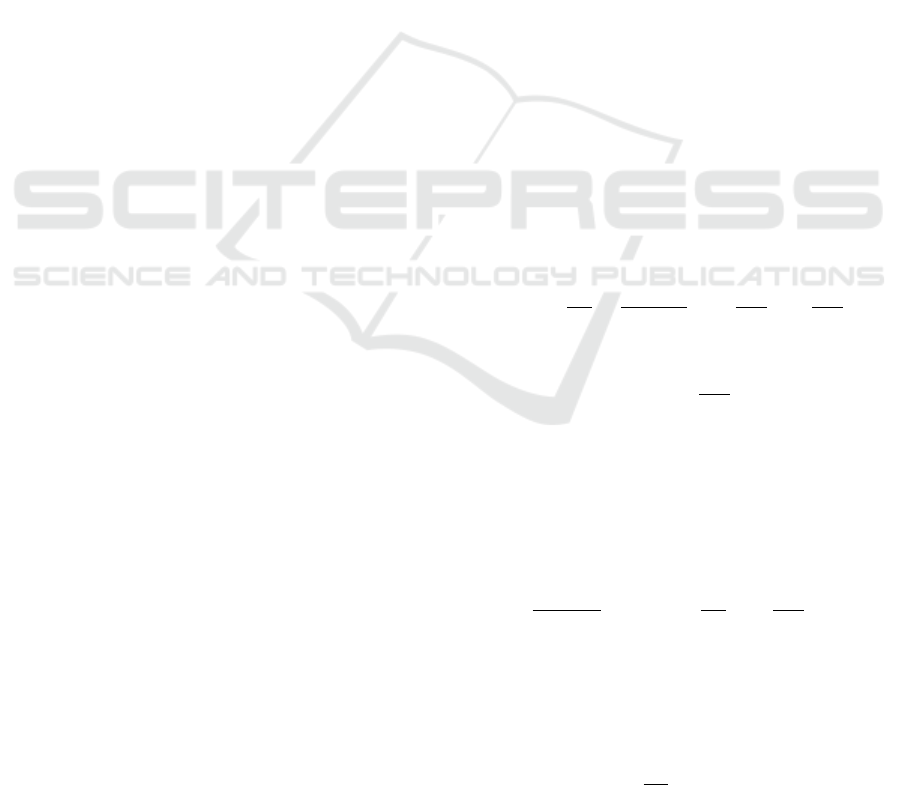
active vibration control system is proposed in (Ballo,
2001) and then the results were compared with theo-
retical considerations estimation.
Bedarff and Pelz (Bedarff and Pelz, ) developed
an active and integrated suspension system capable
of changing its stiffness. This is done by changing
the load carrying area. They choose double acting air
spring bellow with adjustable piston segments.
Zepeng et. al. (Zepeng et al., 2017) tried to
solve the overshoot phenomena found in electric ve-
hicle. This is done by applying fuzzy control to elec-
trically controlled air suspension (ECAS). This work
is done theoretically and verified using AMESim.
It was found that the fuzzy control can solve the
overshoot problem. Miriji and Arockia (Mirji and
Arockia, 2014) applied a fuzzy logic control to half-
car suspension model using Matlab. The half car
suspension (four-degree of freedom) model was es-
tablished and the equations of motion were derived.
Fuzzy logic and PID control for suspension model
were achieved using Matlab. The results showed that
the fuzzy control resulted in more improvement in
stability than PID control. Omar and Ozkan (Omar
and
¨
Ozkan, 2015) applied Linear Quadratic Regu-
lator (LQR) method to study the effect of in-wheel
electric motors mass on the active suspension sys-
tem performance. Their study showed that there was
a bad effect of increasing the unsprung mass due to
the addition of in-wheel motor to the system on the
road holding and ride comfort. Another disadvan-
tage was a higher actuator force was needed to work
in the suspension system with in-wheel motor com-
pared to the same system without IWM. Gohari and
Tahmasebi (Gohari and Tahmasebi, 2015) designed
neuro-active force control (AFC) technique and ap-
plied in active seat suspension system. The con-
troller used is PID which controls the actuator and
the force generated from the actuator was then mea-
sured. The estimated mass was estimated using Arti-
ficial Neural Network (ANN). The results of simula-
tion demonstrated that neuro-AFC scheme improves
the performance of control system compared to the
uncontrolled and PID controller counterpart. Gokul
and Malar presented a new design for air suspension
using LQR control strategy which is applied on air
suspension dynamic model, then the performance was
checked on shaker table. A comparative study is done
between the proposed control system and PID con-
trol system under different operating conditions and
it was found the system performance is improved us-
ing LQR control strategy(S. and K., 2019). From the
above paragraphs, it is divided into two main sections.
The first is developing the air spring dynamic model
to use it in a simulation for suspension system. The
second is developing techniques to improve the per-
formance of vehicle suspension such as variable area
air spring, excitation frequency preknowledge, Apply
fuzzy logic control or neuro active force control.
The motivation of this work is to develop an au-
tomotive suspension system with variable stiffness
for the conflicting requirements of ride and handling.
This paper is concerned with the control of air-spring
suspension using PI-like Fuzzy Logic with control al-
gorithm responsible for changing the air volume to
vary the spring stiffness through using two unequal
volumes.
This paper is organized as follows: the mathe-
matical model of the air-spring suspension system is
developed in Section II. The proposed finite control
augmented with PI-like FLC is discussed in details in
Section III, while the applied Genetic Algorithm opti-
mization is highlighted in Section IV. The simulation
results are presented and discussed in Section V. Fi-
nally, Section VI is the conclusion.
2 MATHEMATICAL MODEL
The stiffness, K of the air spring is defined as the in-
cremental force, dF per incremental deflection, dz.
The force can be calculated by gauge pressure p
g
in-
side the spring multiplied by the effective area, A
e
.
F = p
g
A
e
(1)
K =
dF
dz
=
d(p
g
A
e
)
dz
= A
e
d p
g
dz
+ p
g
dA
e
dz
(2)
Neglecting the change in the effective area, we obtain:
K = A
e
d p
g
dz
(3)
To calculate the change of pressure inside the spring,
polytrophic process is assumed (Gavriloski et al.,
2014).
pV
n
= constant (4)
Where p is pressure, V is the volume and n is poly-
trophic coefficient. By differentiation:
d(p
g
V
n
)
dz
= p
g
nV
n−1
dV
dz
+V
n
d p
g
dz
= 0 (5)
Since the cross-section area is considered constant,
the rate of change of volume per unit deflection is
the effective area but with negative sign. This is be-
cause decreasing the volume increases the deflection
and vice versa.
dV
dz
= −A
e
(6)
ICINCO 2019 - 16th International Conference on Informatics in Control, Automation and Robotics
290