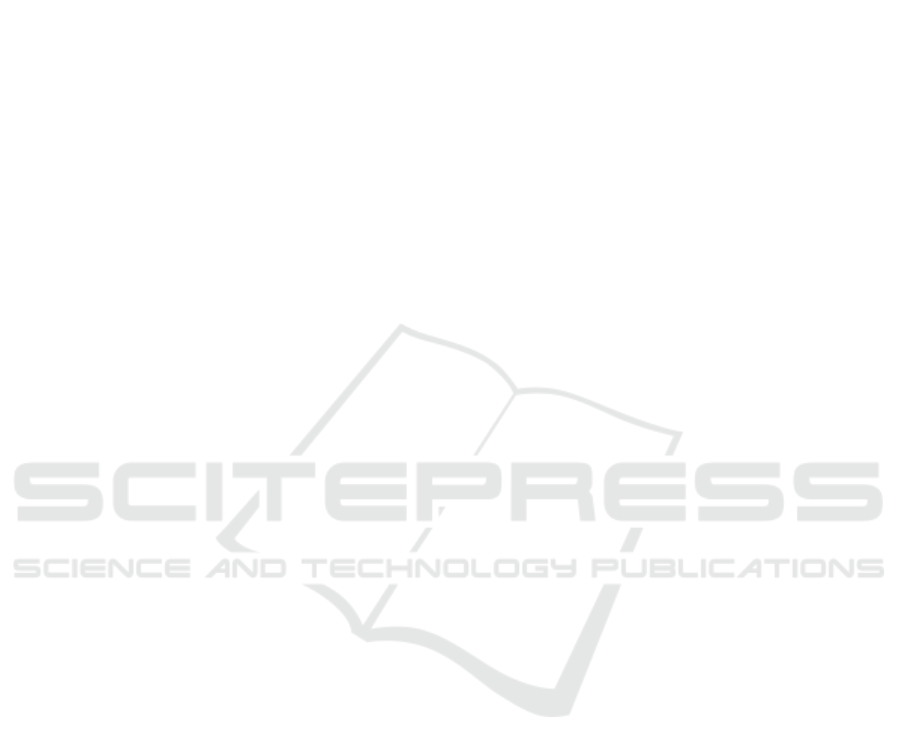
A Modular Underactuated Gripper with Force Control System
A. Margun, D. Bazylev, K. Zimenko and A. Kremlev
Faculty of Control Systems and Robotics, ITMO University, 49 Kronverkskiy av., 197101 Saint Petersburg, Russia
Keywords:
Underactuated Gripper, Force Sensitive System, Force Control, Passive System, Modularity.
Abstract:
A design of an underactuated electromechanical gripper with force control algorithm is presented in this paper.
The key feature of the gripper is the ability to grasp fragile objects and objects of a complex shape. Such
advantages are due to the usage of elastic joints and force sensitive resistors embedded in modules of gripper’s
fingers. Also low cost and mass of the presented device makes its application rational for a larger number
of robotic systems. Proposed force control system is based on PI control and passification approaches that
provide tuning simplicity and good performance in the case of unknown environments. Experimental results
show the efficiency of proposed solution.
1 INTRODUCTION
Development of cheap and mobile mechatronic com-
plexes equipped with a grasping devices is an ac-
tively increasing area of robotics. Creation of univer-
sal grippers for mobile robots operating in unknown
environment is an particular task (Bicchi, 2000; Choi
et al., 2017; Ma et al., 2013).
Grasping devices for mobile robots should satisfy
following conditions:
• low mass and dimensions;
• ability to grasp objects with unknown complex
shape;
• ability of force interaction control;
• low cost and modular structure;
• low energy consumption, etc.
Low mass and energy consumption allow to in-
stall gripper on mobile robots with limited charge of
battery. Low cost and modularity of the structure are
preffered due to practical and financial reasons. In
particular, the modular design significantly improves
the maintainability of the device and its post-warranty
service. On the other hand, a simpler construction
usually ensures a higher reliability of technical sys-
tems (Telegenov et al., 2015).
Interaction with unknown environment may in-
clude accurate grasping for fragile objects and fast re-
action in the case of active environment for damage
prevention. There are three ways to solve this prob-
lem: use of tacticle sensors (as, for example, in Tegin
and Wikander, 2005), adaptive (Bazylev et al., 2015)
and robust (Margun et al., 2014) control laws, use of
underactuated and compliant devices.
One can categorize grasping devices with three
classes: mechanical, vacuum and magnetic. Mag-
netic grippers operate only with ferromagnetic ob-
jects. Therefore, further we do not consider this class.
Vacuum grippers provide grasping of only objects
with special form and structure. So we can not use
them in unknown environment.
There are following classes of mechanical grip-
pers: hydraulic, pneumatic and electric. Hydraulic
grippers can apply the largest strength among all
classes but provide low velocity, require massive
pumps and a lot of energy (Lane et al., 1999). Pneu-
matic grippers are popular due to their light weight
and compact size. The need of use compressors and
impossibility of force and position precise control
(usually only ”bang-bang” control is available) are
main disadvantages of this type. Grippers with elec-
tric motors do not require compressed air or liquid
and provide position and force control. Comparison
of different gripper types is in Table 1.
There are a lot of mechanical schemes for electric
grippers which allow to grasp objects with complex
shape. Some solutions are based on the use of elastic
joints (see Camillo, 2014; Chen and Lin, 2004; Ma
and Dollar, 2014; Ma et al., 2013; Zhang et al., 2018,
etc). Simplicity of manufacture, modularity and low
cost are the main reasons for the increased interest in
such devices. However, the lack of force sensitivity
prevents the use of these grippers in tasks that require
Margun, A., Bazylev, D., Zimenko, K. and Kremlev, A.
A Modular Underactuated Gripper with Force Control System.
DOI: 10.5220/0007923904170422
In Proceedings of the 16th International Conference on Informatics in Control, Automation and Robotics (ICINCO 2019), pages 417-422
ISBN: 978-989-758-380-3
Copyright
c
2019 by SCITEPRESS – Science and Technology Publications, Lda. All rights reserved
417