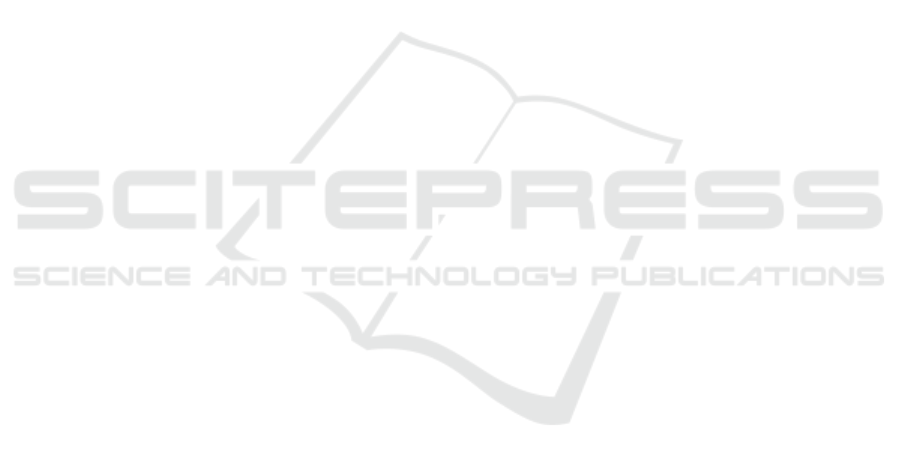
while a robot is in use, which is a particular advantage
in the context of mobile robotics. We show that our
approach is robust and accurate as well as simple to
use. For this reason, we evaluate our approach based
on simulated and real experiments.
2 RELATED WORKS
Robot calibration procedures have been studied ex-
tensively over the past decades. Regarding mobile
manipulators there exist calibration procedures con-
cerning the intrinsic calibration of the manipulator as
in (Bennett et al., 1991) or (Wieghardt and Wagner,
2017) but also procedures for extrinsic calibration of
manipulator and exteroceptive sensors.
The transformation between a manipulator and a
laser scanner can be determined by ascertaining the
relation between the known movement of the manipu-
lator and the corresponding measurements of the laser
scanner. In principle two approaches are investigated
in the research community:
1st) An additional exteroceptive sensor is attached
to the manipulator. This additional sensor is cali-
brated to the laser scanner. The still missing transfor-
mation between the attached sensor and the manipu-
lator needs to be determined as well.
The calibration between a laser scanner and a
camera is examined in several works as (McIvor,
1999), (Mei and Rives, 2006), (Zhang and Pless,
2004). An advantage of these approaches is that cal-
ibration techniques of laser scanner and cameras are
well established in the research community. The ma-
jor drawback regarding mobile manipulators is, that
an additional sensor is needed and a further calibra-
tion between manipulator and camera is neccessary.
This problem is known as hand-eye-calibration prob-
lem and is investigated in several works as (Tsai and
Lenz, 1989) or (Horaud and Dornaika, 1995).
2nd) A calibration target that is well known in its
geometry is attached to the manipulator and moved
within the laser plane. The calibration between the
laser scanner and the manipulator can be determined
by taking into account the known geometry of the cal-
ibration target, the movement of the manipulator and
the measurements of the laser scanner.
An advantage is that no additional sensor is
needed for calibration. The drawback of this calibra-
tion principle is that the laser scanner measurements
needs to be matched with the calibration target’s ge-
ometry unambiguously which requires a calibration
target of appropriate geometry and size.
(Pradeep et al., 2010) examine an approach, us-
ing the intensity of the moving end effector in a 3D
laser scan. This approach requires a 3D laser scanner
which is capable of measuring intensities. In (Antone
and Friedman, 2007) a 3D calibration target is used
to determine the needed transformation with a single
measurement of a 2D laser scanner. This method uses
complex calibration targets of different sizes depend-
ing on the desired accuracy of the calibration. (Ander-
sen et al., 2014) present a method that uses a 2D cali-
bration target. The calibration target is moved within
the spanned area of the 2D laser scanner and the trans-
formation is determined. This method has been eval-
uated in simulation.
In this paper, we propose a calibration procedure
that determines the transformation between a manipu-
lators base and a two 2D laser scanner. Therefore, we
move a 1D geometry within the spanned plane of the
2D laser scanner. In contrast to state-of-the-art cali-
bration procedures this paper examines a method that
does not require additional sensors, using a calibra-
tion target which has a much simpler geometry com-
pared to existing approaches. Furthermore, because
of the 1D nature of the object, alternative objects as
drills can also be used for calibration which makes
our approach independent of specialized calibration
bodies which are needed for other approaches.
The suggested approach simplifies the idea intro-
duced in (Andersen et al., 2014) by using a less com-
plex 1D calibration target. Whereas the approach pre-
sented in (Andersen et al., 2014) fits multiple features
of the calibration targets’ geometry simultaneously,
our proposed approach only fits one intersection of
the 1D calibration target with the laser plane at a time.
The lower number of features for an individual mea-
surement is compensated by repeated measurements
of the targets’ intersection for several configurations
of the manipulator. Besides, in contrast to (Ander-
sen et al., 2014), measurements of real experiments
are used for evaluation to show the capabilities of our
approach.
The calibration procedure does not require labora-
tory environment conditions and can be carried out by
operators without professional skills. The error of the
proposed calibration is lower than the tolerance of the
deployed laser scanner emphasizing its practical rele-
vance. As only a 1D calibration target is required the
procedure is applicable using drilling tools already at-
tached to the end effector.
In summarise the main contributions of this work
are:
• Calibration procedure using a 1D calibration tar-
get and no additional sensor
• Applicable without calibration target when used
with attached drilling tools
Robust Calibration Procedure of a Manipulator and a 2D Laser Scanner using a 1D Calibration Target
113