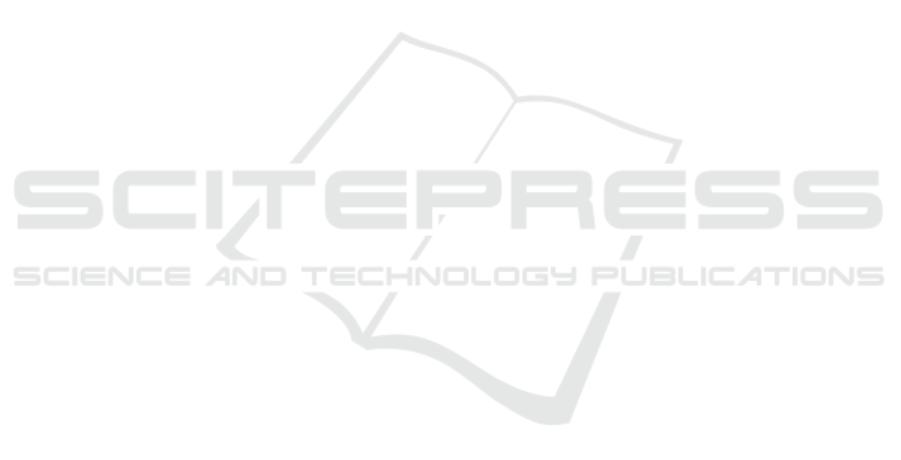
and mathematical models behind the CAE system
ASTRA.
Reducing the number of compressor stages proved
to be an effective way of altering the operation
point of the gas turbine in case a substantial
change is necessary. Distortion of the
performance map of the compressor changes the
conditions of the joint operation of the
corresponding turbine, so its operating point needs
to be adjusted. Joint operation of the compressor
and turbine is adjusted by changing the area of
characteristic cross-sections.
Parameters of the upgraded power plant were
calculated for the 6 MW (3-stage low-pressure
compressor) and 8.3 MW (4-stage LPC) variants,
with the corresponding air flow rates 27 and 17
percent below the baseline engine, respectively.
Restrictions on the rotational speeds and air-gas
channel geometry were applied during the
optimization to preserve the stress-strain state of
the critical elements of the engine and keep most
of its parts unaltered. Subsequent strength
analyses will provide more specific data on this
matter.
Results of the thermodynamic optimization will
be used as the initial input for the in-detail
simulation (Filinov, 2018), optimization of
turbomachines (Matveev, 2018; Marchukov,
2017; Popov, 2017, ) and other engine’s elements
(Falaleev, 2017; Zubrilin, 2017), adjustments of
the engine design and developing the
manufacturing process of the engine parts
(Kokareva, 2018).
Results of the engine development project would
be used to develop the method of combined use of
the mathematical models suitable for the amount
of available information at each design stage.
ACKNOWLEDGEMENTS
This work was supported by the Ministry of education
and science of the Russian Federation in the
framework of the implementation of the Program of
increasing the competitiveness of Samara University
among the world's leading scientific and educational
centers for 2013-2020 years.
REFERENCES
Allen, J.G., Newmark, G.L., 2018. The Life and Death of
North American Rail Freight Electrification. In
Transportation Research Record.
Azadeh, A., Salehi, V., Kianpour, M., 2018. Performance
evaluation of rail transportation systems by considering
resilience engineering factors: Tehran railway
electrification system. In Transportation Letters.
Bartosh, E.T., 1972. Gas turbine for railway application,
Transport. Moscow.
Baturin, O., Tkachenko, A., Krupenich, I., 2017.
Identifying the approach to significantly improve the
performance of NK-36ST gas turbine power plant. In
Proceedings of the ASME Turbo Expo.
Desjouis, B., Remy, G., Ossart, F., Marchand, C., Bigeon,
J., Sourdille, E., 2015. A new generic problem
formulation dedicated to electrified railway systems. In
Electrical Systems for Aircraft, Railway and Ship
Propulsion.
D'Ovidio, G., Carpenito, A., Masciovecchio, C.,
Ometto, A., 2017. Preliminary analysis on advanced
technologies for hydrogen light-rail trains application
in sub-urban non electrified routes. In Ingegneria
Ferroviaria.
Duffy, M.C., 1998–1999. The Gas Turbine in Railway
Traction. In Transactions of the Newcomen Society.
Falaleev, S.V., Vinogradov, A.S., 2017. Procedure for
designing an unloading device for the thrust bearing of
the rotor of a turbomachine. In Journal of Machinery
Manufacture and Reliability.
Filinov, E., Tkachenko, A., Omar, H.H., Rybakov, V., 2018.
Increase the Efficiency of a Gas Turbine Unit for Gas
Turbine Locomotives by Means of Steam Injection into
the Flow Section. In MATEC Web of Conferences.
Goldshtein, I., Averbukh, M., 2019. Electrification Israel
Railroads: Network Frequency Instability and
Challenges of Distribution Voltage Control. In 2018
IEEE International Conference on the Science of
Electrical Engineering in Israel.
Hao, H., Liu, F., Liu, Z., Zhao, F., 2017. Measuring energy
efficiency in China's transport sector. In Energies.
Jones, P.B., Levy, J., Bosco, J., Schwartz, L., 2018. The
future of transportation electrification: utility, industry
and consumer perspectives. In Technical report # 10.
Lawrence Berkeley National Laboratory.
Kokareva, V.V., Smelov, V.G., Agapovichev, A.V., Sotov,
A.V., Sufiiarov, V.S., 2018. Development of SLM
quality system for gas turbines engines parts
production. In IOP Conference Series: Materials
Science and Engineering.
Krastev, I., Tricoli, P., Hillmansen, S., Chen, M., 2016. Future
of electric railways: Advanced electrification systems with
static converters for ac railways. In IEEE Electrification
Magazine.
Kuz'michev, V.S., Tkachenko, A.Y., Krupenich, I.N., 2014.
Composing a virtual model of gas turbine engine
working process using the CAE system "ASTRA". In
Research Journal of Applied Sciences.
Lee, T., 1975. Turbines westward, T. Lee Publications.
Manhattan, Kansas.
Lu, S.-M., 2016. A low-carbon transport infrastructure in
Taiwan based on the implementation of energy-saving
measures. In Renewable and Sustainable Energy
Reviews.
SIMULTECH 2019 - 9th International Conference on Simulation and Modeling Methodologies, Technologies and Applications
336