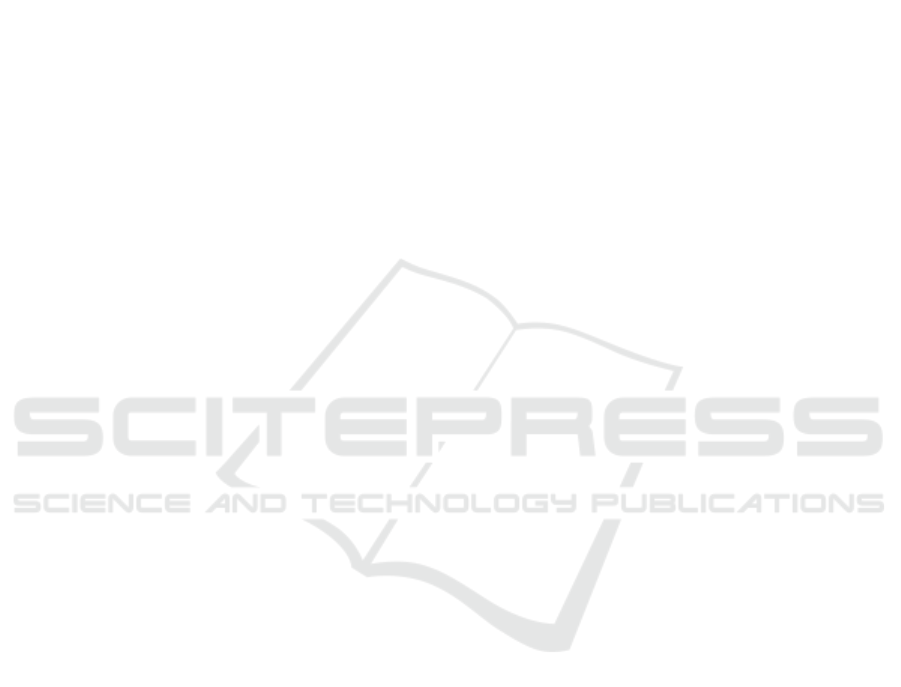
Inventory Routing Problem with Non-stationary Stochastic Demands
Ehsan Yadollahi
1,2
, El-Houssaine Aghezzaf
1
, Joris Walraevens
2
and Birger Raa
1
1
Department of Industrial Systems Engineering and Product Design,
Faculty of Engineering and Architecture, Ghent University, Ghent, Belgium
2
Department of Telecommunications and Information Processing (TELIN),
Faculty of Engineering and Architecture, Ghent University, Ghent, Belgium
Keywords: Inventory Routing Problem, Stochastic Demand, Non-stationary, Optimization.
Abstract: In this paper we solve Stochastic Periodic Inventory Routing Problem (SPIRP) when the accuracy of
expected demand is changing among the periods. The variability of demands increases from period to
period. This variability follows a certain rate of uncertainty. The uncertainty rate shows the change in
accuracy level of demands during the planning horizon. To deal with the growing uncertainty, we apply a
safety stock based SPIRP model with different levels of safety stock. To satisfy the service level in the
whole planning horizon, the level of safety stock needs to be adjusted according to the demand’s variability.
In addition, the behavior of the solution model in long term planning horizons for retailers with different
demand accuracy is taken into account. We develop the SPIRP model for one retailer with an average level
of demand, and standard deviation for each period. The objective is to find an optimum level of safety stock
to be allocated to the retailer, in order to achieve the expected level of service, and minimize the costs. We
propose a model to deal with the uncertainty in demands, and evaluate the performance of the model based
on the defined indicators and experimentally designed cases.
1 INTRODUCTION
Minimizing logistics costs has been a major issue in
many industries, especially those dealing with
relatively high level of costs for transportations,
storage, and stock-outs (Pujawan et al, 2015). In
such a situation, not only the “best” schedules for
the replenishment matters, but also the estimated
costs for storage capacity, holding and stock-out
costs are crucial. Minimizing these costs while the
promised level of service is satisfied, is the major
issue in inventory routing problem.
Forecasting the expected demands is the initial
requirement for Inventory Routing Problem (IRP)
(Sagaert et al, 2018). The accuracy of the expected
demand affects inventory level and related costs
during the planning horizon. Normally these
estimations are done based on the historical data
gathered from previous periods. So far most of the
studies about IRP have considered demands as
stationary stochastic among the periods (Abdul
Rahim et al, 2014; Bertazzi et al, 2015; Diaz et al,
2016; Rahim and Irwan, 2015; Yadollahi et al,
2017), while in real life cases -when the planning is
done for a long horizon- the accuracy of the
estimated demand may decrease among the periods
and make the estimated demand more uncertain.
That influences the IRP optimization in long term
planning horizon regarding the minimization of the
costs and covering the promised service level. A
product with a random demand pattern would
always have higher costs as compared to a product
with sinusoidal or life cycle demand pattern from
both costs and service level points of view.
Therefore, a fair trade-off between service level and
total costs is required (Purohit et al, 2016).
While distribution planning is considered as
operational in nature, storage capacity allocation
tend to be strategic (Manzini and Bindi, 2009) as
they require large capital investments. Therefore,
trading-off the two decisions under uncertainty is
challenging. To this, we also add the non-stationarity
in the stochastic demands at the retailers. In this
paper first we consider solution models for
Stochastic Periodic Inventory Routing Problem
(SPIRP) with non-stationary demands and then
reformulate it to take into account different policies
for allocation of safety stock at the retailers. In the
658
Yadollahi, E., Aghezzaf, E., Walraevens, J. and Raa, B.
Inventory Routing Problem with Non-stationary Stochastic Demands.
DOI: 10.5220/0007948506580665
In Proceedings of the 16th International Conference on Informatics in Control, Automation and Robotics (ICINCO 2019), pages 658-665
ISBN: 978-989-758-380-3
Copyright
c
2019 by SCITEPRESS – Science and Technology Publications, Lda. All rights reserved