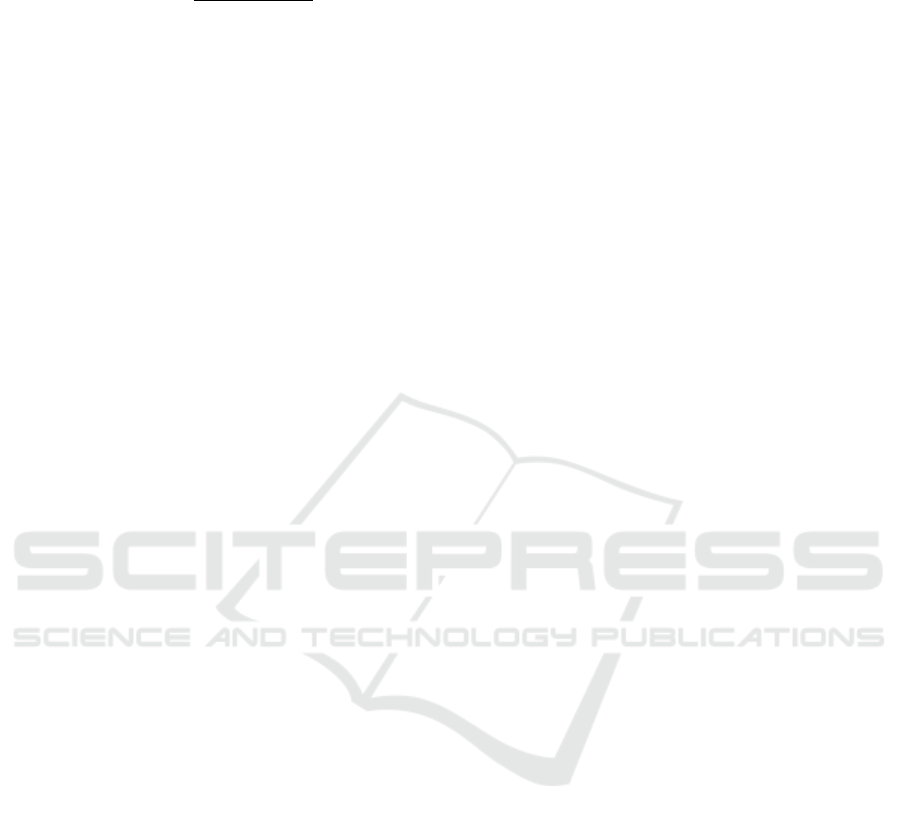
ation of the model complexity:
f itness =
1
RSS · (1 + k
P
d)
, (19)
where d is the number of estimation parameters, RSS
is the residual sum of squares of the error in time do-
main. With k
P
the trade-off between model complex-
ity and accuracy can be adjusted. Here, it has been
set to 2. Information criteria could be used instead,
but they require knowledge of the measurement noise
(James et al., 2013) and experiments have shown that
they lead to rather high model complexities if the
number of samples is large.
The genetic operations of step 6 are explained in
the following section.
3.2 Genetic Operations
In step 6 of figure 5 genetic operations are performed
on the current population to create the offspring. First,
new individuals are created by means of recombi-
nation, also called crossover or also by means of
cloning. The percentage that an individual is just
cloned from the parent population is p
clone
. So the
number of cloned individuals stems from a Binomial
distribution N
clone
∼ B(n
P
, p
clone
) with n
P
the size of
the population. A total of N
P
− N
clone
individuals is
generated by means of recombination: The first par-
ent is copied up to a randomly chosen node. The
branch behind this node is replaced by a branch of
the second parent, the origin of which is also chosen
randomly. Each new node is not added but dropped if
a construction rule would be violated by adding it. At
the end a node with a one-mass system is added if no
multiple-mass system exists.
Choosing a parent either for cloning or for repro-
duction is done via Roulette Wheel Selection based on
the fitness, see (Nelles, 2001).
After the new population has been created, differ-
ent kinds of mutations are performed with a certain
probability:
• Point Mutation: One randomly chosen node is
assigned a random, new model type that satisfies
the construction rules. The new estimation param-
eters are defined randomly within the permissible
range.
• Insertion Mutation: A node is added, if possi-
ble, originating from a randomly chosen existing
node. Its model type is random but satisfies the
construction rules.
• Deletion Mutation: A randomly chosen node is
deleted, again only if the construction rules are
respected by the operation.
• Chromosome Mutation: In this mutation a node
is also chosen randomly, but the mutation is not
limited to the one node. Instead, the node and the
whole branch originating from it is replaced by
a new, randomly grown branch that satisfies the
construction rules. The size of the resulting tree
is set randomly, but not less than the original tree
without the new branch. This kind of mutation is
inspired by (Koza, 1994).
Construction Rules. Whenever a genetic operation
is performed or when the initial population is created,
the construction rules must be considered:
• Each model can be included a minimum of 0 times
and a maximum of 1 time.
• Exactly one model of the general type ’multiple-
mass system’ must be included in all individuals.
• The model type ’one-mass system’ is mutually ex-
clusive with the model type ’backlash’.
It is believed that the mutations play an important
role in the parameter identification. When nodes are
copied from the parent population in cloning or re-
combination, the current parameter estimates are also
copied and used as a starting point for the optimiza-
tion in the next generation. As a consequence, previ-
ously found good solutions are passed on to the next
generation shortening optimization time and preserv-
ing good solutions. However, the drawback is that the
optimizer is subject to premature convergence due to
this procedure. When new, random parameters are
reintroduced by the mutations, local minima can be
escaped. The same is true for the structure optimiza-
tion.
4 SIMULATION RESULTS
A reference model is simulated and its output is used
instead of real measurements. The reference model
is a 2-mass resonating system with all three friction
components but no gravity, current control or delay
time, no noise. The excitation for the reference model
and the optimization models is a torque signal that
would lead to a standard industrial jerk-limited re-
versing motion if applied to a single moving mass,
see figure 6.
As output the velocity at mass 1 is used. The lower
and upper bounds of the estimation parameters are set
to 50 %, resp. 200 % of the assumed values. Only the
gravity torque has a range centred around 0 because
gravity is allowed to be both positive and negative.
The GP algorithm is run for 20 generations with 6 in-
dividuals. For the parameter optimization a maximum
Structure and Parameter Identification of Process Models with Hard Non-linearities for Industrial Drive Trains by Means of Degenerate
Genetic Programming
373