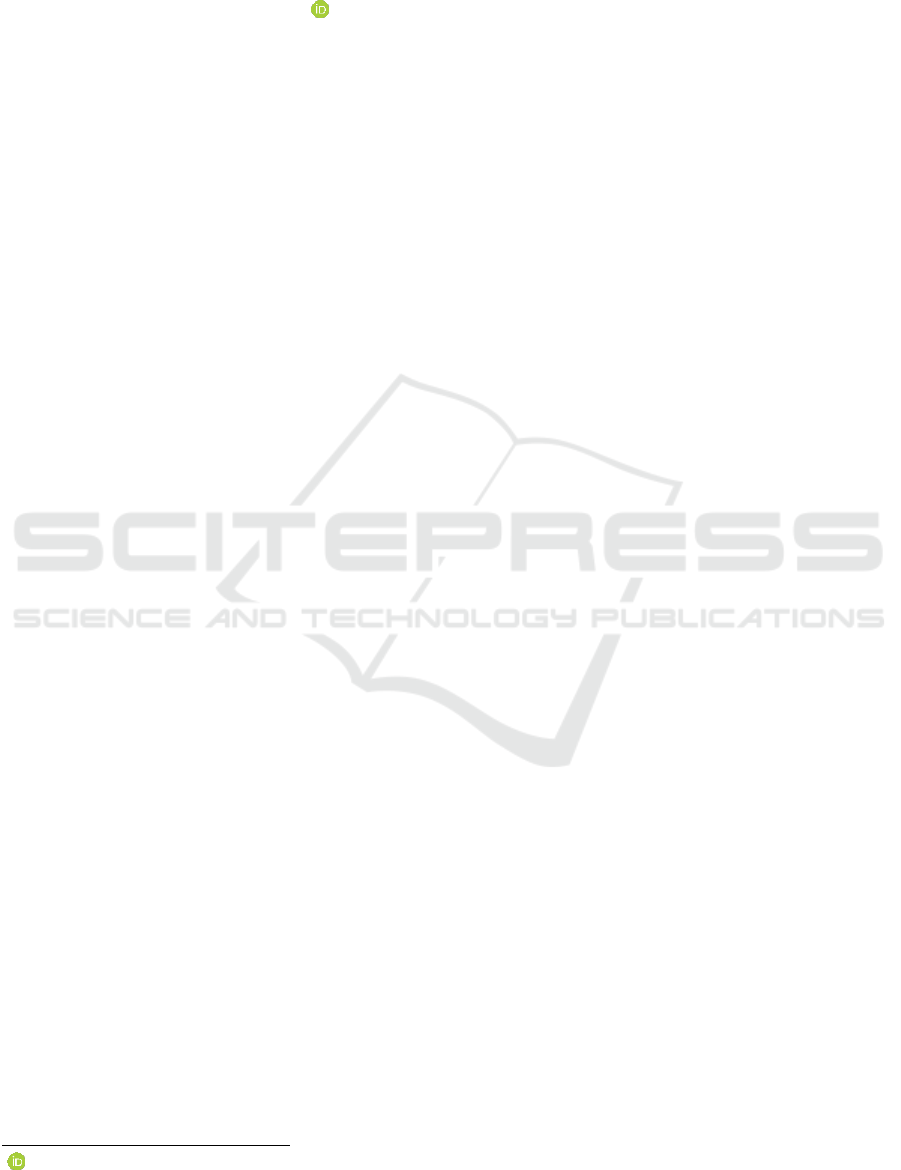
Automated Shoe Last Customization using MATLAB Algorithm
T. Y. Pang
1 a
, K. H. Soh
1
, S. Ryan
2
and P. Dabnichki
1
1
School of Engineering, RMIT University, Bundoora Campus East, Bundoora VIC 3083, Australia
2
Glenrowan Enterprises T/A GoodFit Feet Sizing, 9 De Laeter Way, Technology Park, Bantley, WA 6073, Australia
Keywords: Shoe Last, Customization, Cycling, Automated, Algorithm, CAD.
Abstract: Footwear plays an essential role in human daily life as properly fitting and comfortable footwear will
significantly improve human lives and productivity. Footwear customisation techniques aim to manufacture
footwear that fits an individual’s foot geometric. Footwear that exactly fits a person’s foot geometric will
provide more support and reduce impact when walking or when doing other activities. A customised shoe last
is an important tool used by shoemakers in manufacturing customised shoes. Currently, most customised shoe
lasts are made from the moulds of clients’ feet and all the measurements are done manually, which is a tedious
and time-consuming process. This project aims to develop a novel MATLAB (2017) algorithm that will
shorten the shoe last customization process and do so with higher accuracy. This MATLAB algorithm can
reconstruct the foot model to smooth the surface texture and rearrange the three-dimensional (3D) model
vertices for easier dimension calculations. It can also locate makers on first and fifth metatarsophalangeal
joint automatically for more accurate shoe last design. The shoe last developed using the novel algorithm was
used to create its equivalent negative moulds for the manufacturing of carbon fibre cycling shoes. The negative
moulds were 3D printed and used to produce a prototype of cycling shoes. Future research needs to consider
developing an automated algorithm to create negative moulds to speed up the cycling shoe manufacturing
process.
1 INTRODUCTION
Footwear is necessary in human daily life, as it is
designed to protect the foot from external pressure
and improve walking and sports performance. Well-
fitting footwear is important to provide support and
enhance user comfort. Ill-fitting footwear can cause
injuries and foot shape deformation, which will
reduce gait quality (Terrier et al., 2009). Finding the
right pair of shoes with the correct fit is important for
athletes, particularly with the emergence of
competitive sports. Therefore, footwear must not only
be designed to fit the users properly and to improve
comfort, but also maximize athletic performance and
minimize injury (Luximon et al., 2009, Werd et al.,
2010).
Footwear customization is an essential aspect of
manufacturing footwear that fits an individual’s feet
geometrics and dimensions to improve fit and user
comfort (Davia et al., 2013). The shoe last is an
important tool that determines the design, shape, size
and, more importantly, the fit of the final product
a
https://orcid.org/0000-0002-4766-3042
during the footwear manufacturing process. The
production speed of shoe last is very important in
shoemaking industry, in order to decrease the overall
shoe production budget in terms of time and money
(Zhang et al., 2012).
There are two main methods in manufacturing
customised shoe lasts: (i) the traditional method; and
(ii) a computer-based method (Telfer et al., 2010). In
the traditional footwear manufacturing method, shoe
makers use plaster to form a client’s foot geometric
in a mould. Then, footwear will be made according to
the mould (Figure 1), normally known as shoe last.
The manufacturing of a shoe last through the
traditional method is done manually and through a
trial-and-error approach that is a purely artisanal and
based on the shoemaker’s experience to fit specific
feet dimensions. It is an arduous and complex process
that takes a lot of time to manufacture due to
constraints imposed by the manual measuring of
several feet’s dimensions (Leng et al., 2006).
Nowadays, with an increasing cost of labour even
in developing countries, there is great interest in
Pang, T., Soh, K., Ryan, S. and Dabnichki, P.
Automated Shoe Last Customization using MATLAB Algorithm.
DOI: 10.5220/0007949301170122
In Proceedings of the 7th International Conference on Sport Sciences Research and Technology Support (icSPORTS 2019), pages 117-122
ISBN: 978-989-758-383-4
Copyright
c
2019 by SCITEPRESS – Science and Technology Publications, Lda. All rights reserved
117