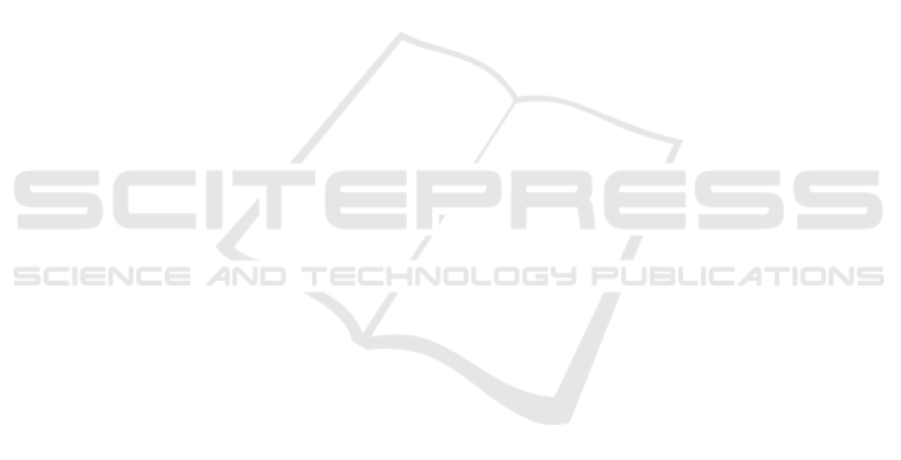
Bouzgou, K., Amar, R. H. E., and Ahmed-Foitih, Z. (2015).
Virtual reality simulation and singularity analysis of
3-rrr translational parallel robot. In Innovative Com-
puting Technology (INTECH), 2015 Fifth Interna-
tional Conference on, pages 61–66. IEEE.
Cho, S. and Shim, D. H. (2017). Development of a vision-
enabled aerial manipulator using a parallel robot.
Transactions of the Japan Society for Aeronautical
and Space Sciences, Aerospace Technology Japan,
15(APISAT-2016):a27–a36.
Dai, S., Lee, T., and Bernstein, D. S. (2014). Adaptive con-
trol of a quadrotor uav transporting a cable-suspended
load with unknown mass. In Decision and Control
(CDC), 2014 IEEE 53rd Annual Conference on, pages
6149–6154. IEEE.
Danko, T. W., Chaney, K. P., and Oh, P. Y. (2015). A parallel
manipulator for mobile manipulating uavs. In Tech-
nologies for Practical Robot Applications (TePRA),
2015 IEEE International Conference on, pages 1–6.
IEEE.
Danko, T. W. and Oh, P. Y. (2014). Design and control of
a hyper-redundant manipulator for mobile manipulat-
ing unmanned aerial vehicles. Journal of Intelligent &
Robotic Systems, 73(1-4):709.
Escareno, J., Flores, G., Rakotondrabe, M., Romero, H.,
Lozano, R., and Rubio, E. (2014). Task-based con-
trol of a multirotor miniature aerial vehicle having an
onboard manipulator. In Unmanned Aircraft Systems
(ICUAS), 2014 International Conference on, pages
857–863. IEEE.
Fumagalli, M., Naldi, R., Macchelli, A., Forte, F., Keemink,
A. Q., Stramigioli, S., Carloni, R., and Marconi,
L. (2014). Developing an aerial manipulator proto-
type: Physical interaction with the environment. IEEE
robotics & automation magazine, 21(3):41–50.
Huber, F., Kondak, K., Krieger, K., Sommer, D.,
Schwarzbach, M., Laiacker, M., Kossyk, I., Parusel,
S., Haddadin, S., and Albu-Sch
¨
affer, A. (2013). First
analysis and experiments in aerial manipulation us-
ing fully actuated redundant robot arm. In Intelligent
Robots and Systems (IROS), 2013 IEEE/RSJ Interna-
tional Conference on, pages 3452–3457. IEEE.
Jimenez-Cano, A., Heredia, G., and Ollero, A. (2017).
Aerial manipulator with a compliant arm for bridge
inspection. In Unmanned Aircraft Systems (ICUAS),
2017 International Conference on, pages 1217–1222.
IEEE.
Kamel, B., Yasmina, B., Laredj, B., Benaoumeur, I., and
Zoubir, A.-F. (2017). Dynamic modeling, simulation
and pid controller of unmanned aerial vehicle uav. In
Innovative Computing Technology (INTECH), 2017
Seventh International Conference on, pages 64–69.
IEEE.
Kim, S., Choi, S., and Kim, H. J. (2013). Aerial ma-
nipulation using a quadrotor with a two dof robotic
arm. In Intelligent Robots and Systems (IROS), 2013
IEEE/RSJ International Conference on, pages 4990–
4995. IEEE.
Kondak, K., Krieger, K., Albu-Schaeffer, A., Schwarzbach,
M., Laiacker, M., Maza, I., Rodriguez-Castano, A.,
and Ollero, A. (2013). Closed-loop behavior of an
autonomous helicopter equipped with a robotic arm
for aerial manipulation tasks. International Journal of
Advanced Robotic Systems, 10(2):145.
Korpela, C., Orsag, M., Pekala, M., and Oh, P. (2013). Dy-
namic stability of a mobile manipulating unmanned
aerial vehicle. In germany 2013, I., editor, Robotics
and Automation (ICRA), 2013 IEEE International
Conference on, pages 4922–4927. IEEE.
Lipiello, V. and Ruggiero, F. (2012). Exploiting redundancy
in cartesian impedance control of uavs equipped with
a robotic arm. In RSJ International Conference on
Intelligent Robots and Systems, pages 3768–3773.
Lippiello, V. and Ruggiero, F. (2012). Cartesian impedance
control of a uav with a robotic arm. IFAC Proceedings
Volumes, 45(22):704–709.
Mello, L. S., Aldorno, B., and Raffo, G. V. (2015). Whole-
body modeling and control of an unmanned aerial ma-
nipulator. In the XII Brazilian Symposium of Intelli-
gent Automation (XII SBAI). Natal.
Mersha, A. Y., Stramigioli, S., and Carloni, R. (2014). Ex-
ploiting the dynamics of a robotic manipulator for
control of uavs. In Robotics and Automation (ICRA),
2014 IEEE International Conference on, pages 1741–
1746. IEEE.
Orsag, M., Korpela, C., and Oh, P. (2013). Modeling and
control of mm-uav: Mobile manipulating unmanned
aerial vehicle. Journal of Intelligent & Robotic Sys-
tems, pages 1–14.
Ruggiero, F., Trujillo, M. A., Cano, R., Ascorbe, H., Vig-
uria, A., Per
´
ez, C., Lippiello, V., Ollero, A., and Si-
ciliano, B. (2015). A multilayer control for multirotor
uavs equipped with a servo robot arm. In Robotics and
Automation (ICRA), 2015 IEEE International Confer-
ence on, pages 4014–4020. IEEE.
Siciliano, B., Sciavicco, L., Villani, L., and Oriolo, G.
(2010). Robotics: modelling, planning and control.
Springer Science & Business Media.
Srikanth, M. B., Soto, A., Annaswamy, A., Lavretsky, E.,
and Slotine, J.-J. (2011). Controlled manipulation
with multiple quadrotors. In AIAA Conf. on Guidance,
Navigation and Control.
Yeol, J. W., Toohey, D., and Hwang, Y.-W. (2017). Design
and analysis of a multiple tentacle system for mobile
manipulation in micro aerial vehicles. Procedia Com-
puter Science, 105:7–13.
ICINCO 2019 - 16th International Conference on Informatics in Control, Automation and Robotics
482