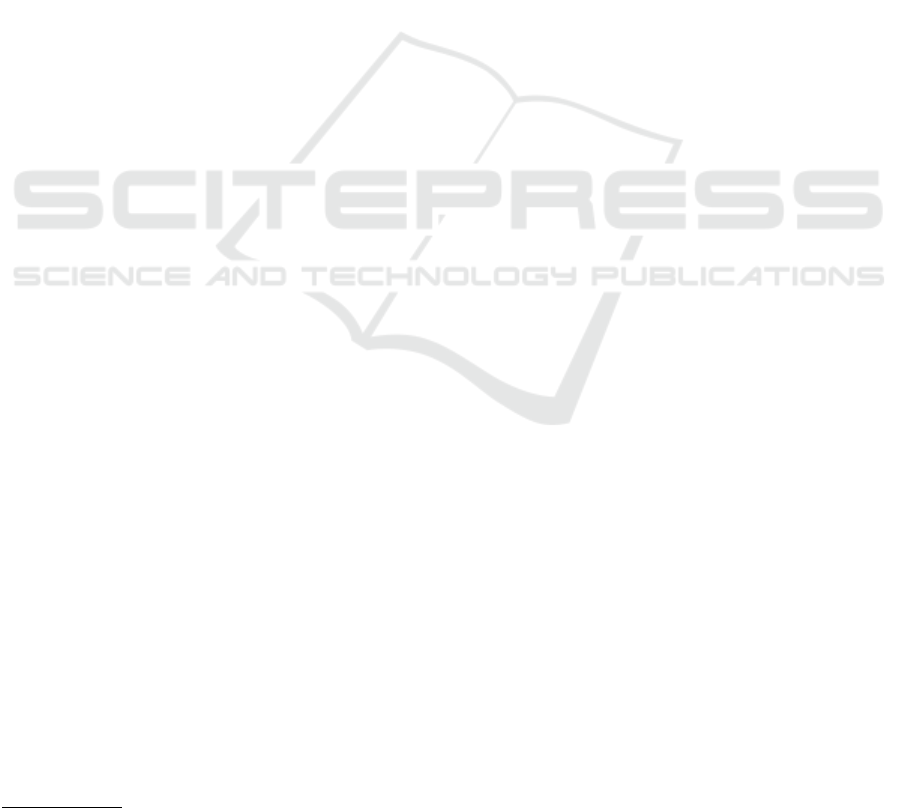
Direct Sound Shield: The shield built into the end-
effector is mounted in a fixed position. In some areas
of the part, a little gap between the surface and the part
could be observed, allowing sound directly travelling
from the transmitter to the receiver, influencing the
lamb wave amplitude detection.
Lamb Wave Propagation Length: Fixed lengths of
50 mm for the offsets on and from the surface were
used. While the distance from the surface could be re-
duced, the transducers cannot be moved more closely
together because of their size. This causes the flaws
to appear ”stretched” along the sweep direction.
Process Control Accuracy: So far, no in-depth tests
have been conducted how accurate the process con-
trol system works, i.e. how precise the transducers
follow the waypoints and how well their trajectories
are synchronized.
7 CONCLUSIONS AND FUTURE
WORK
In this paper, we have introduced an approach for air-
coupled ultrasonic inspection through adaptive lamb
wave control. A software toolchain to fully calcu-
late and determine the adaptive process was devel-
oped. An adaptive end-effector was designed for ex-
perimental evaluation. For this purpose, a specimen
part was manufactured.
It was possible to verify the principle and the
toolchain as well as the adaptive end-effector were
successfully tested. While the process was found to
be working generally, still a lot of room for improve-
ment exists. Future work could include improving the
hardware such as the direct sound shield. Further-
more, diffent combinations of ultrasonic heads and
other specimens could be examined. Also, a sophisti-
cated analysis of the process control system could be
revealing.
ACKNOWLEDGEMENTS
We would like to thank HEBI Robotics
9
for provid-
ing us a set of X-Series Actuators for the experimental
evaluation.
REFERENCES
Castaings, M. and Cawley, P. (1996). The generation, prop-
agation, and detection of Lamb waves in plates us-
9
https://www.hebirobotics.com/
ing air-coupled ultrasonic transducers. J. Acoust. Soc.
Am., 100(5):3070–3077.
Castaings, M., Cawley, P., Farlow, R., and Hayward, G.
(1998). Single sided inspection of composite mate-
rials using air coupled ultrasound. J. Nondestr. Eval.,
17(1):37–45.
Castaings, M. and Hosten, B. (2001). Lamb and SH
waves generated and detected by air-coupled ul-
trasonic transducers in composite material plates.
NDT&E Int., 34:249–258.
Castaings, M. and Hosten, B. (2008). Ultrasonic guided
waves for health monitoring of high-pressure compos-
ite tanks. NDT&E Int., 41:648–655.
Cunfu, H., Hongye, L., Zenghua, L., and Bin, W. (2013).
The propagation of coupled Lamb waves in multi-
layered arbitrary anisotropic composite laminates. J.
Sound Vib., 332:7243–7256.
Diamanti, K. and Soutis, C. (2010). Structural health mon-
itoring techniques for aircraft composite structures.
Prog. Aeronaut. Sci., 46:342–352.
Huber, A. M. A. and Sause, G. R. (2018). Classification
of solutions for guided waves in anisotropic compos-
ites with large numbers of layers. J. Acoust. Soc. Am.,
144(6):3236–3251.
Kessler, S. S., Spearing, S. M., and Soutis, C. (2002).
Damage detection in composite materials using Lamb
wave methods. Smart Mater. Struct., 11:269–278.
Kundu, T., Maji, A., Gosh, T., and Maslov, K. (1998). De-
tection of kissing bonds by Lamb waves. Ultrasonics,
35:573–580.
Lowe, M. J. S., Alleyne, D. N., and Cawley, P. (1998). De-
fect detection in pipes using guided waves. Ultrason-
ics, 36:147–154.
Lowe, M. J. S. and Cawley, P. (1994). The applicability
of plate wave techniques for the inspection of adhe-
sive and diffusion bonded joints. J. Nondestr. Eval.,
13(4):185–200.
Luukkala, M., Heikkila, P., and Surakka, J. (1971). Plate
wave resonance - A contactless test method. Ultra-
sonics, 9(4):201–208.
Luukkala, M. and Meril
¨
ainen, P. (1973). Metal plate testing
using airborne ultrasound. Ultrasonics, 11(5):218–
221.
Maslov, K. and Kundu, T. (1997). Selection of Lamb modes
for detecting internal defects in composite laminates.
Ultrasonics, 35:141–150.
Purekar, A. S. and Pines, D. J. (2010). Damage detection in
thin composite laminates using piezoelectric phased
sensor arrays and guided Lamb wave interrogation. J.
Intell. Mater. Syst. Struct., 21:995–1010.
Ramadas, C., Balasubramaniam, K., Joshi, M., and Krish-
namurthy, C. V. (2011). Sizing of interface delami-
nation in a composite T-joint using time-of-flight of
Lamb waves. J. Intell. Mater. Syst. Struct., 22:757–
768.
Solodov, I., Pfleiderer, K., Gerhard, H., and Busse, G.
(2004a). Nonlinear acoustic approach to material
characterisation of polymers and composites in tensile
tests. Ultrasonics, 42:1011–1015.
Air-coupled Ultrasonic Inspection with Adaptive Lamb Wave Control
437