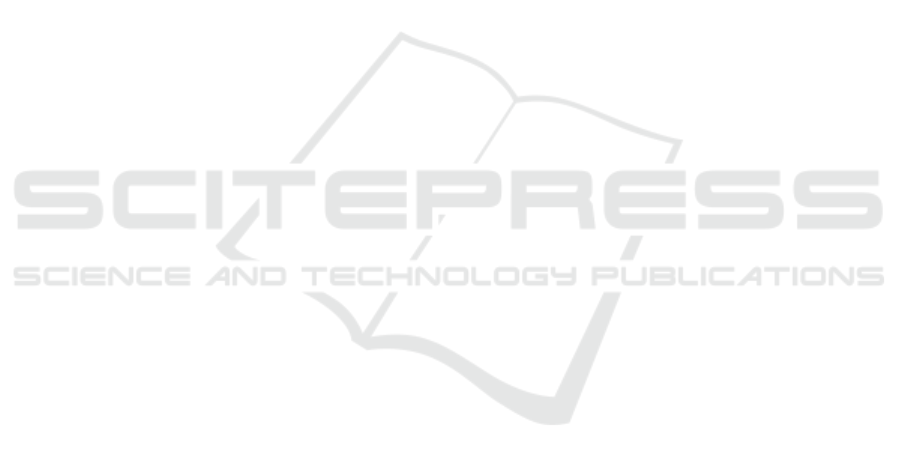
els in Automation and Robotics (MMAR), pages 1200–
1205. IEEE.
Heng, M. and Erkorkmaz, K. (2010). Design of a nurbs in-
terpolator with minimal feed fluctuation and continu-
ous feed modulation capability. International Journal
of Machine Tools and Manufacture, 50(3):281–293.
Horne, B. G. and Giles, C. L. (1995). An experimental
comparison of recurrent neural networks. In Advances
in neural information processing systems, pages 697–
704.
Huo, F., Xi, X.-C., and Poo, A.-N. (2012). Generalized
taylor series expansion for free-form two-dimensional
contour error compensation. International Journal of
Machine Tools and Manufacture, 53(1):91–99.
Jansen, D. and Buttner, H. (2004). Real-time ethernet: the
ethercat solution. Computing and Control Engineer-
ing, 15(1):16–21.
Jia, Z.-y., Song, D.-n., Ma, J.-w., Hu, G.-q., and Su, W.-
w. (2017). A nurbs interpolator with constant speed
at feedrate-sensitive regions under drive and contour-
error constraints. International Journal of Machine
Tools and Manufacture, 116:1–17.
Liu, H., Liu, Q., Zhou, S., Li, C., and Yuan, S. (2015).
A nurbs interpolation method with minimal feedrate
fluctuation for cnc machine tools. The Interna-
tional Journal of Advanced Manufacturing Technol-
ogy, 78(5-8):1241–1250.
Ni, H., Hu, T., Zhang, C., Ji, S., and Chen, Q. (2018).
An optimized feedrate scheduling method for cnc ma-
chining with round-off error compensation. The In-
ternational Journal of Advanced Manufacturing Tech-
nology, 97(5-8):2369–2381.
Paprocki, M., Wawrzak, A., Erwinski, K., and Klosowiak,
M. (2018). Flexible pc-based cnc machine control sys-
tem. Mechanik, 91(4):299–303.
Piegl, L. and Tiller, W. (2012). The NURBS book. Springer
Science & Business Media.
Ramesh, R., Mannan, M., and Poo, A. (2005). Tracking
and contour error control in cnc servo systems. Inter-
national Journal of Machine Tools and Manufacture,
45(3):301–326.
Sencer, B., Altintas, Y., and Croft, E. (2009). Modeling
and control of contouring errors for five-axis machine
tools. part i: Modeling. Journal of manufacturing sci-
ence and engineering, 131(3).
Szczepanski, R., Erwinski, K., and Paprocki, M. (2017).
Accelerating pso based feedrate optimization for
nurbs toolpaths using parallel computation with
openmp. In 2017 22nd International Conference
on Methods and Models in Automation and Robotics
(MMAR), pages 431–436. IEEE.
Tang, L. and Landers, R. G. (2013). Multiaxis contour con-
trol—the state of the art. IEEE Transactions on Con-
trol Systems Technology, 21(6):1997–2010.
Uchiyama, N. et al. (2011). Contouring controller design
based on iterative contour error estimation for three-
dimensional machining. Robotics and Computer-
Integrated Manufacturing, 27(4):802–807.
Xie, H., Tang, H., and Liao, Y.-H. (2009). Time series
prediction based on narx neural networks: An ad-
vanced approach. In 2009 International conference
on machine learning and cybernetics, volume 3, pages
1275–1279. IEEE.
Xu, G., Chen, J., Zhou, H., Yang, J., Hu, P., and Dai, W.
(2018). Multi-objective feedrate optimization method
of end milling using the internal data of the cnc sys-
tem. The International Journal of Advanced Manu-
facturing Technology, pages 1–17.
Yeh, S. and Hsu, P. (2002). Estimation of the contour-
ing error vector for the cross-coupled control design.
IEEE/ASME Transactions on Mechatronics, 7(1):44–
51.
Zhang, Y., Ye, P., Zhao, M., and Zhang, H. (2019). Dy-
namic feedrate optimization for parametric toolpath
with data-based tracking error prediction. Mechani-
cal Systems and Signal Processing, 120:221–233.
Zhu, L., Zhao, H., and Ding, H. (2013). Real-time con-
touring error estimation for multi-axis motion systems
using the second-order approximation. International
Journal of Machine Tools and Manufacture, 68(5):75–
80.
Neural Network Contour Error Prediction of a Bi-axial Linear Motor Positioning System
809