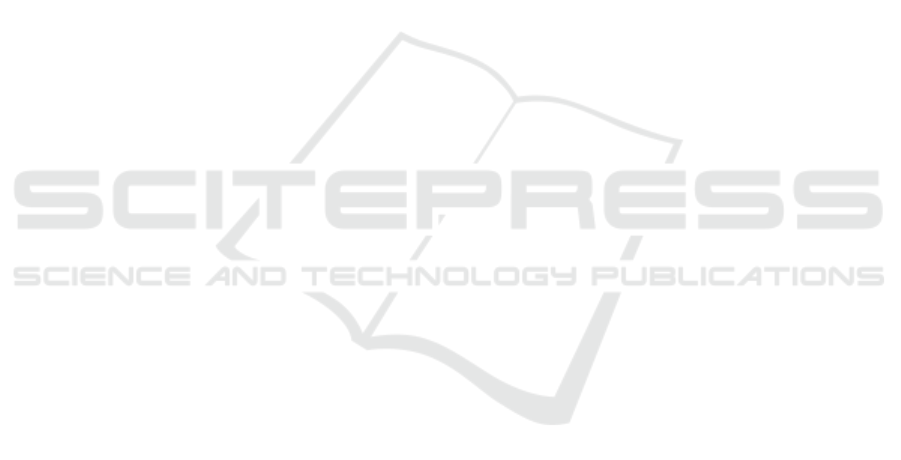
7 CONCLUSIONS AND
OUTLOOK
We investigated a non-circular trajectory for robot-
based X-ray CT and its application for the reconsti-
tution of a multi-material object using numerical sim-
ulations. Within the study we calculated a set of fea-
sible robot positions to obtain a set of X-ray projec-
tion images to reconstruct a voxel dataset. Further, we
simulated a standard circular CT and visually com-
pared the results of the two reconstructions qualita-
tively. We have shown that when using additional
information from different non-circular directions, a
much higher image quality can be expected in contrast
to a standard circular scan. Future work will focus
on optimization methods for robot CT path planning,
taking trajectory and accuracy limitations of robots,
material and geometrical properties of various speci-
mens as well as object and scan-specific X-ray inter-
action effects into account. Furthermore, experiments
using a real robot-based CT system will be performed
in the near future.
REFERENCES
De Chiffre, L., Carmignato, S., Kruth, J.-P., Schmitt, R., and
Weckenmann, A. (2014). Industrial applications of
computed tomography. CIRP Annals - Manufacturing
Technology, 63(2):655–677.
Fieselmann, A., Steinbrener, J., Jerebko, A. K., Voigt, J. M.,
Scholz, R., Ritschl, L., and Mertelmeier, T. (2016).
Twin robotic x-ray system for 2d radiographic and 3d
cone-beam ct imaging. In Kontos, D., Flohr, T. G.,
and Lo, J. Y., editors, Medical Imaging 2016: Physics
of Medical Imaging, SPIE Proceedings, page 97830G.
SPIE.
Herl, G., Hiller, J., and Sauer, T. (2019). Artifact reduc-
tion in x-ray computed tomography by multipositional
data fusion using local image quality measures. In
9th Conference on Industrial Computed Tomography,
(iCT 2019) Padua-Italy.
Katsevich, A. (2005). Image reconstruction for the circle-
and-arc trajectory. Physics in medicine and biology,
50(10):2249–2265.
Noo, F., Clack, R., White, T. A., and Roney, T. J. (1998).
The dual-ellipse cross vertex path for exact recon-
struction of long objects in cone-beam tomography.
Physics in medicine and biology, 43(4):797–810.
Ouadah, S., Jacobson, M., Stayman, J. W., Ehtiati, T.,
Weiss, C., and Siewerdsen, J. H. (2017). Task-driven
orbit design and implementation on a robotic c-arm
system for cone-beam ct. Proceedings of SPIE–the
International Society for Optical Engineering, 10132.
Reisinger, S., Kasperl, S., Franz, M., Hiller, J., and Schmid,
U. (2011). Simulation-based planning of optimal con-
ditions for industrial computed tomography. In Inter-
national Symposium on Digital Industrial Radiology
and Computed Tomography, Berlin, Germany, vol-
ume 3.
Tuy, H. K. (1983). An inversion formula for cone-beam
reconstruction. In SIAM Journal on Applied Mathe-
matics 43.3 p. 456-552.
Zhao, C., Herbst, M., Vogt, S., Ritschl, L., Kappler, S.,
Siewerdsen, J. H., and Zbijewski, W. (2019). A
robotic x-ray cone-beam ct system: trajectory opti-
mization for 3d imaging of the weight-bearing spine.
In Bosmans, H., Chen, G.-H., and Gilat Schmidt, T.,
editors, Medical Imaging 2019: Physics of Medical
Imaging, page 56. SPIE.
ICINCO 2019 - 16th International Conference on Informatics in Control, Automation and Robotics
522