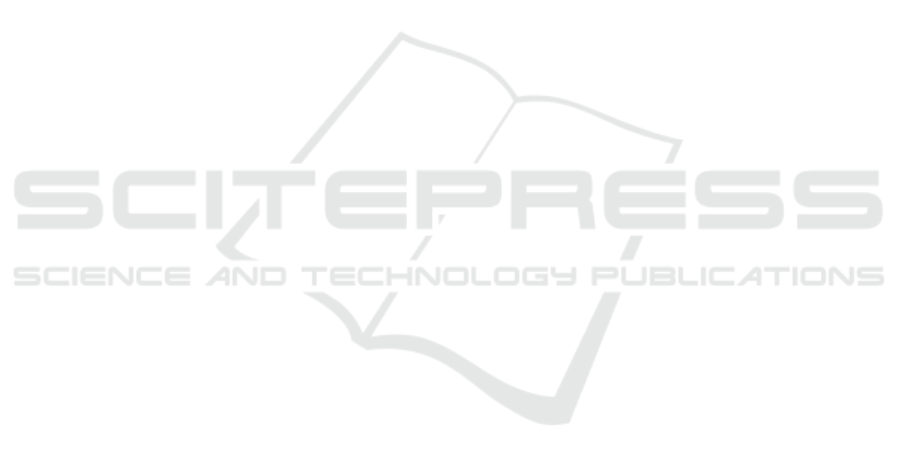
applied to both, and the results are evaluated statis-
tically and compared to the results of a classical A
∗
implementation. MRPA performs well with the mod-
ular concepts and finds good solutions without run-
ning into huge state-space explosions. However, it is
not yet capable of global optimization, which will be
addressed in ongoing work. Besides, also improved
handling of robot cooperation based on independent
skills is planned to be investigated in future research.
ACKNOWLEDGEMENTS
This work is partly funded by the German Research
Foundation (DFG) under the TeamBotS grant.
REFERENCES
Albu-Sch
¨
affer, A., Ott, C., and Hirzinger, G. (2007). A uni-
fied passivity-based control framework for position,
torque and impedance control of flexible joint robots.
Intl. J. Rob. Research, 26(1):23–39.
Andersen, R. H., Dalgaard, L., Beck, A. B., and Hallam, J.
(2015). An architecture for efficient reuse in flexible
production scenarios. In 2015 IEEE Conf. on Autom.
Science and Engineering, pages 151–157.
Angerer, A., Vistein, M., Hoffmann, A., Reif, W., Krebs, F.,
and Sch
¨
onheits, M. (2015). Towards multi-functional
robot-based automation systems. In 12th Intl. Conf. on
Inform. in Control, Autom. & Robot., pages 438–443.
Fikes, R. and Nilsson, N. J. (1971). STRIPS: A new ap-
proach to the application of theorem proving to prob-
lem solving. Artif. Intell., 2(3/4):189–208.
Finkemeyer, B., Kr
¨
oger, T., and Wahl, F. (2010). The adap-
tive selection matrix - a key component for sensor-
based control of robotic manipulators. In 2010 IEEE
Intl. Conf. on Robotics and Autom., pages 3855–3862.
Giunchiglia, F. (1999). Using abstrips abstractions –
where do we stand? Artificial Intelligence Review,
13(3):201–213.
Gl
¨
uck, R., Hoffmann, A., N
¨
agele, L., Schierl, A., Reif,
W., and Voggenreiter, H. (2018). Towards a tool-
based methodology for developing software for dy-
namic robot teams. In 15th Intl. Conf. on Inform. in
Control, Autom. & Robot., pages 615–622.
Hart, P. E., Nilsson, N. J., and Raphael, B. (1968). A formal
basis for the heuristic determination of minimum cost
paths. IEEE Trans. on Systems Science and Cybernet-
ics, 4(2):100–107.
Kagermann, H., Wahlster, W., and Helbig, J., editors
(2013). Umsetzungsempfehlungen f
¨
ur das Zukunft-
sprojekt Industrie 4.0. acatech.
Knepper, R. A., Layton, T., Romanishin, J., and Rus, D.
(2013). Ikeabot: An autonomous multi-robot coordi-
nated furniture assembly system. In 2013 IEEE Intl.
Conf. on Robot. & Autom., pages 855–862.
Knoblock, C. A. (1990). Learning abstraction hierarchies
for problem solving. In 8
th
Nat. Conf. on Artificial
Intelligence, pages 923–928. AAAI Press.
Koga, Y. and Latombe, J. . (1994). On multi-arm manipu-
lation planning. In 1994 IEEE Intl. Conf. on Robot. &
Autom., pages 945–952.
Macho, M., N
¨
agele, L., Hoffmann, A., Angerer, A., and
Reif, W. (2016). A flexible architecture for automat-
ically generating robot applications based on expert
knowledge. In 47
th
Intl. Symp. on Robotics.
Malec, J., Nilsson, A., Nilsson, K., and Nowaczyk, S.
(2007). Knowledge-based reconfiguration of automa-
tion systems. In 2007 IEEE Intl. Conf. on Autom. Sci-
ence and Engineering, pages 170–175.
McDermott, D., Ghallab, M., Howe, A., Knoblock, C.,
Ram, A., Veloso, M., Weld, D., and Wilkins, D.
(1998). PDDL — the planning domain definition lan-
guage. Technical Report TR 98 003/DCS TR 1165,
Yale Center for Computational Vision and Control.
N
¨
agele, L., Macho, M., Angerer, A., Hoffmann, A., Vistein,
M., Sch
¨
onheits, M., and Reif, W. (2015). A backward-
oriented approach for offline programming of com-
plex manufacturing tasks. In 6
th
Intl. Conf. on Autom.,
Robotics & Applications, pages 124–130. IEEE.
N
¨
agele, L., Schierl, A., Hoffmann, A., and Reif, W. (2018).
Automatic planning of manufacturing processes us-
ing spatial construction plan analysis and extensible
heuristic search. In 15
th
Intl. Conf. on Inform. in Con-
trol, Autom. and Robot., pages 576–583.
Nau, D., Au, T.-C., Ilghami, O., Kuter, U., Murdock, J. W.,
Wu, D., and Yaman, F. (2003). Shop2: An htn plan-
ning system. J. Artif. Int. Res., 20(1):379–404.
Pfrommer, J., Schleipen, M., and Beyerer, J. (2013). PPRS:
production skills and their relation to product, process,
and resource. In 18
th
IEEE Conf. on Emerging Techn.
& Factory Autom. IEEE.
Schoen, T. R. and Rus, D. (2013). Decentralized robotic as-
sembly with physical ordering and timing constraints.
In 2013 IEEE/RSJ Intl. Conf. on Intell. Robots and
Systems, pages 5764–5771.
Stein, D., Schoen, T. R., and Rus, D. (2011). Constraint-
aware coordinated construction of generic structures.
In 2011 IEEE/RSJ Intl. Conf. on Intell. Robots and
Systems, pages 4803–4810.
Thomas, U. and Wahl, F. M. (2001). A system for auto-
matic planning, evaluation and execution of assembly
sequences for industrial robots. In 2001 IEEE/RSJ
IEEE/RSJ Intl. Conf. on Intell. Robots and Systems,
pages 1458–1464.
Wilkins, D. E. (1984). Domain-independent planning repre-
sentation and plan generation. Artificial Intelligence,
22(3):269–301.
Wolfe, J., Marthi, B., and Russell, S. (2010). Combined
task and motion planning for mobile manipulation. In
20
th
Intl. Conf. on Automated Planning and Schedul-
ing, pages 254–257. AAAI Press.
Yan, Z., Jouandeau, N., and Cherif, A. A. (2013). A survey
and analysis of multi-robot coordination. Intl. J. of
Advanced Robotic Systems, 10(12):399.
ICINCO 2019 - 16th International Conference on Informatics in Control, Automation and Robotics
604