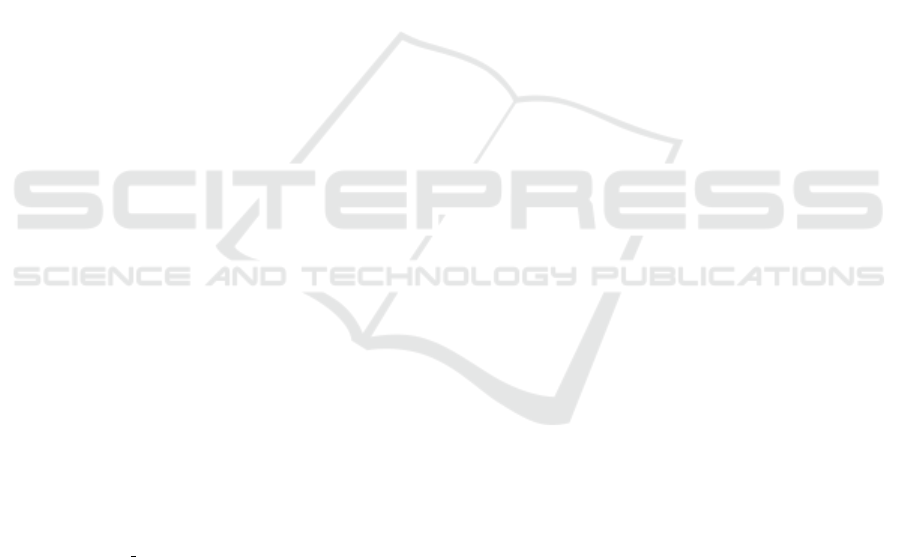
served. This is achieved by implementing the sen-
sor sampling and filtering as well as parts of the force
closed-loop control as dedicated IP Core. Especially,
the latter removes any significant jitter from the con-
trol execution.
It has been validated experimentally that the exe-
cution characteristics of the software components im-
plemented within the robotic framework are adequate.
Overall, the achieved sampling frequencies and deter-
minism match or even exceed the properties of com-
parable systems. Similarly, the achieved frequency of
the FinEmbP communication bus with 1.36 kHz com-
pares well to other walking machines.
A potential next step would be the implementa-
tion of the commutation and the current control of
the BLDC within the FPGA fabric as a dedicated
co-processor. Thereby, the Elmo Gold Twitter servo
drive can be substituted by a bare output-stage that
features three half bridges and the appropriate facili-
ties for the current measurement. Subsequently, the
modular electronics can be composed to a highly-
integrated physically small single PCB. It could be
beneficial to integrate the electronics into the actua-
tor.
If the jitter of the communication bus proofs to be
critical, firstly a real-time operating system (OS) at
the master side poses a potential improvement. Fur-
thermore, the OS’s stack could be partially bypassed
using, e.g., by using libpcap.
ACKNOWLEDGEMENTS
This work was partly funded by the European Com-
mission 7th Framework Program under the project
H2R (no.60069).
REFERENCES
Gerkey, B. (2017). Why ROS 2.0? http://design.ros2.org/
articles/why ros2.html. Accessed: 2019-04-16.
Hutter, M. (2013). StarlETH & co-design and control of
legged robots with compliant actuation. PhD thesis,
Diss., Eidgen"ossische Technische Hochschule
ETH Z"urich, Nr. 21073, 2013.
Knabe, C., Griffin, R., Burton, J., Cantor-Cooke, G., Danta-
narayana, L., Day, G., Ebeling-Koning, O., Hahn, E.,
Hopkins, M., Neal, J., and others (2015). Designing
for Compliance: ESCHER, Team VALOR’s Compli-
ant Biped. Technical report, Terrestrial Robotics En-
gineering & Controls (TREC) Lab, Virginia Tech.
Ott, C., Baumg
¨
artner, C., Mayr, J., Fuchs, M., Burge, R.,
Lee, D., Eiberger, O., Albu-Sch
¨
affer, A., Grebenstein,
M., and Hirzinger, G. (2010). Development of a biped
robot with torque controlled joints. In Humanoid
Robots (Humanoids), 2010 10th IEEE-RAS Interna-
tional Conference on, pages 167–173. IEEE.
Radford, N. A., Strawser, P., Hambuchen, K., Mehling,
J. S., Verdeyen, W. K., Donnan, A. S., Holley, J.,
Sanchez, J., Nguyen, V., Bridgwater, L., et al. (2015).
Valkyrie: Nasa’s first bipedal humanoid robot. Jour-
nal of Field Robotics, 32(3):397–419.
Reichardt, M., Sch
¨
utz, S., and Berns, K. (2017). One
fits more - on highly modular quality-driven design
of robotic frameworks and middleware. Journal
of Software Engineering for Robotics (JOSER):
Special Issue on Robotic Computing, 8(1):141–
153. ISSN: 2035-3928; this publication is available at
http://joser.unibg.it/index.php?journal=joser&page=is
sue&op=view&path[]=9.
Scholz, D. (2016). On the Design and Development of Mus-
culoskeletal Bipedal Robots. PhD thesis, Technische
Universit
¨
at Darmstadt.
Sch
¨
utz, S., Mianowski, K., K
¨
otting, C., Nejadfard, A., Re-
ichardt, M., and Berns, K. (2016). RRLAB SEA – A
highly integrated compliant actuator with minimised
reflected inertia. In IEEE International Conference
on Advanced Intelligent Mechatronics (AIM).
Sch
¨
utz, S., Nejadfard, A., Mianowski, K., Vonwirth, P., and
Berns, K. (2017). CARL – A compliant robotic leg
featuring mono- and biarticular actuation. In IEEE-
RAS International Conference on Humanoid Robots,
pages 289–296.
Sch
¨
utz, S., Reichardt, M., Arndt, M., and Berns, K. (2014).
Seamless extension of a robot control framework to
bare metal embedded nodes. In Informatik 2014, Lec-
ture Notes in Informatics (LNI), pages 1307–1318,
Stuttgart, Germany.
Shirai, T., Osawa, K., Chishiro, H., Yamasaki, N., and
Inaba, M. (2016). Design and Implementation of
a High Power Robot Distributed Control System on
Dependable Responsive Multithreaded Processor (D-
RMTP). In IEEE 4th International Conference on
Cyber-Physical Systems, Networks, and Applications
(CPSNA), pages 19–24.
Tsagarakis, N. G., Caldwell, D. G., Negrello, F., Choi,
W., Baccelliere, L., Loc, V., Noorden, J., Muratore,
L., Margan, A., Cardellino, A., Natale, L., Hoffman,
E. M., Dallali, H., Kashiri, N., Malzahn, J., Lee, J.,
Kryczka, P., Kanoulas, D., Garabini, M., Catalano,
M., Ferrati, M., Varricchio, V., Pallottino, L., Pavan,
C., Bicchi, A., Settimi, A., Rocchi, A., and Ajoudani,
A. (2017). Walk-man: A high-performance humanoid
platform for realistic environments. Journal of Field
Robotics, 34(7):1225–1259.
Whitney, D. (1977). Force feedback control of manipulator
fine motions. Trans. ASME J. of Dynam. Syst., Mea-
sur. and Control, 99(2):91–97.
Zhao, Y., Paine, N., Kim, K. S., and Sentis, L. (2015). Sta-
bility and Performance Limits of Latency-Prone Dis-
tributed Feedback Controllers. IEEE Transactions on
Industrial Electronics, 62(11):7151–7162.
FPGA-based Embedded System Designed for the Deployment in the Compliant Robotic Leg CARL
543