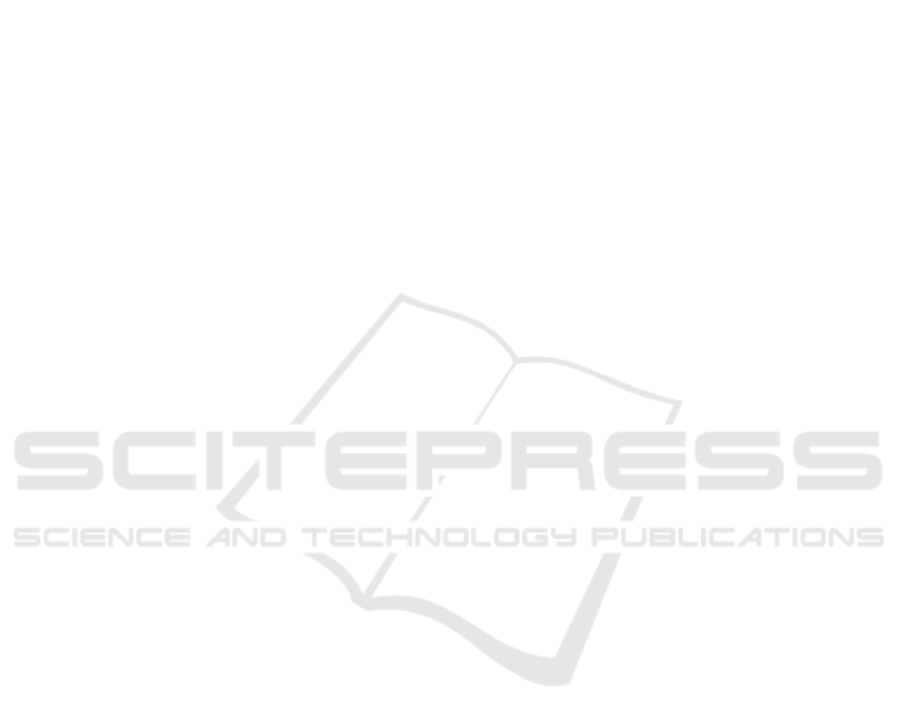
Autonomous Gripping and Carrying of Polyhedral Shaped Object based
on Plane Detection by a Quadruped Tracked Mobile Robot
Toyomi Fujita and Nobuatsu Aimi
Department of Electronics and Intelligent Systems, Tohoku Institute of Technology, Sendai 982-8577, Japan
Keywords:
Mobile Robot with Multiple Manipulation Arms, Autonomous Gripping, Depth Image, Plane Detection,
Observation Position Computation.
Abstract:
Recently, it is highly expected that robots work instead of human in a dangerous site such as disaster area.
Sufficient working ability is required for such robots as well as moving ability. Thus, we present a method for
autonomous gripping and carrying of a polyhedral shaped object by a mobile robot with multiple manipulation
arms based on plane detection. Using this method, the robot can calculate appropriate observation positions
for the detection of gripping planes and positions of the object. We apply the method to a quadruped tracked
robot and verify its effectiveness in experiments for autonomous gripping and carrying of a box shaped object.
1 INTRODUCTION
In recent years, a robot is expected to perform some
actions related to rescue activity in a disaster area.
The robot should perform not only an exploration but
also a working task by itself in the area. For such
a task, the robot that has manipulation arms is use-
ful. Therefore, we have developed several tracked
mobile robots that were equipped with multiple legs
which can be used as manipulation arms (Fujita and
Tsuchiya, 2014) (Fujita and Tsuchiya, 2015) (Fujita
and Sasaki, 2017). These robots can operate some
handling tasks such as a transportation of target ob-
ject using two legs by a remote control. However, it is
basically difficult to control properly for such tasks.
In order to solve this problem, this study consid-
ers that such robots perform transportation tasks au-
tonomously by detecting gripping positions of a poly-
hedral shaped object. Proposed method is based on
the detection of gripped planes by two manipulation
arms. In the method, the robot detects gripping planes
and positions using a depth sensor by observing the
object at several positions. We consider how to de-
termine proper observation positions to detect them
efficiently.
The following sections describe the overall
method for detecting information to grip and carry a
polyhedral shaped object in Section 3, how to deter-
mine the observation positions in Section 4, imple-
mented robot system in Section 5, and experiments
for proposed methods in Section 6.
2 RELATED WORKS
Recently, some autonomous planning for robot grip-
ping have been considered.
Yamazaki et al. presented a method for object
grasping by modeling based on voxel representation
(Yamazaki et al., 2007). In this method, a robot ob-
serves an object from multiple views and generates a
3-D model consisting of voxel. The gripping position
is determined by the area of voxel and posture of the
hand. It may be difficult for our aim to apply because
the robot needs to move the area surrounding object
to capture multi-viewpoint images.
Masuda and Lim presented a method for plane de-
tection utilizing 3-D Hough transform and a structure
of retina (Masuda and Lim, 2014). However, gripping
planning is not considered after the plane detection.
We present a method based on plane detection of
a polyhedral object and obtain planes on which the
robotic arms can grip and manipulate by their hands.
Gu et al. presented a grip planning method to gener-
ate optimal collision-free grip sequences for a biped
climbing robot based on a pole detection and grasp-
ing pose computation using depth and image data(Gu
et al., 2017)(Gu et al., 2018). This method mainly
considers point and line information as geometric in-
formation. This study, on the other hand, mainly con-
sider plane information of a polyhedral object.
In the method presented by Harada et al., the
shape of object was obtained as a cluster of triangle
planes using a map of normal vectors, then gripping
552
Fujita, T. and Aimi, N.
Autonomous Gripping and Carrying of Polyhedral Shaped Object based on Plane Detection by a Quadruped Tracked Mobile Robot.
DOI: 10.5220/0007980905520558
In Proceedings of the 16th International Conference on Informatics in Control, Automation and Robotics (ICINCO 2019), pages 552-558
ISBN: 978-989-758-380-3
Copyright
c
2019 by SCITEPRESS – Science and Technology Publications, Lda. All rights reserved