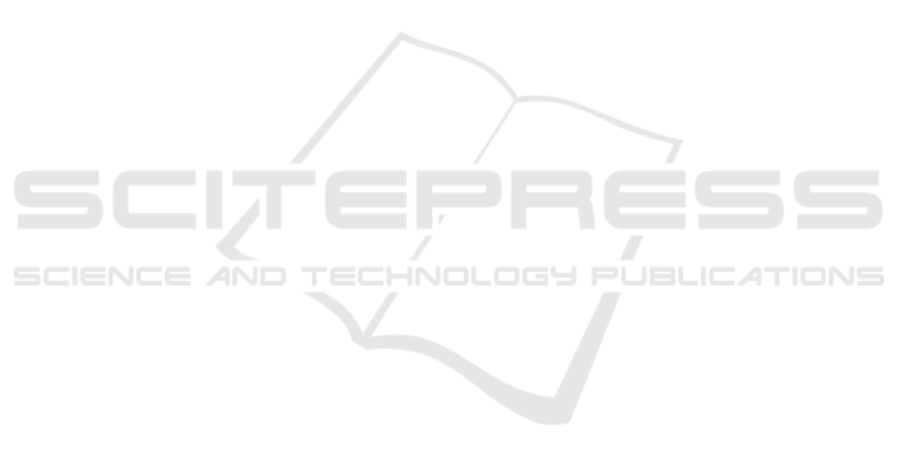
ergy Consumption. Progress in Electromagnetics Re-
search, 12:259–295.
Kansal, A., Hsu, J., Zahedi, S., and Srivastava, M. B.
(2007). Power Management in Energy Harvesting
Sensor Networks. ACM Trans. Embed. Comput. Syst.,
6(4).
Kansal, A. and Srivastava, M. (2003). An Environmental
Energy Harvesting Framework for Sensor Networks.
In Proceedings of the 2003 International Symposium
on Low Power Electronics and Design, 2003. ISLPED
2003. ACM.
Kim, H. S., Abdelzaher, T. F., and Kwon, W. H. (2003).
Minimum-Energy Asynchronous Dissemination to
Mobile Sinks in Wireless Sensor Networks. In Pro-
ceedings of the first international conference on Em-
bedded networked sensor systems - SenSys 2003.
ACM Press.
Marta, M. and Cardei, M. (2009). Improved sensor network
lifetime with multiple mobile sinks. Pervasive and
Mobile Computing, 5(5):542–555.
Pieber, T. W., Ulz, T., and Steger, C. (2017a). SystemC Test
Case Generation with the Gazebo Simulator. In Pro-
ceedings of the 7th International Conference on Sim-
ulation and Modeling Methodologies, Technologies
and Applications - Volume 1: SIMULTECH,, pages
65–72. INSTICC, SciTePress.
Pieber, T. W., Ulz, T., and Steger, C. (2017b). Using Gazebo
to Generate Use Case Based Stimuli for SystemC. In
International Conference on Simulation and Modeling
Methodologies, Technologies and Applications, pages
241–256. Springer.
Pieber, T. W., Ulz, T., Steger, C., and Matischek, R.
(2017c). Hardware Secured, Password-based Authen-
tication for Smart Sensors for the Industrial Internet of
Things. In International Conference on Network and
System Security, pages 632–642. Springer.
Pinuela, M., Mitcheson, P. D., and Lucyszyn, S. (2013).
Ambient RF energy harvesting in urban and semi-
urban environments. IEEE Transactions on Mi-
crowave Theory and Techniques, 61(7):2715–2726.
Rahimi, M., Shah, H., Sukhatme, G., Heideman, J., and
Estrin, D. (2003). Studying the Feasibility of En-
ergy Harvesting in a Mobile Sensor Network. In 2003
IEEE International Conference on Robotics and Au-
tomation (Cat. No.03CH37422). IEEE.
Shah, R. C., Roy, S., Jain, S., and Brunette, W. (2003). Data
MULEs: Modeling and Analysis of a Three-tier Ar-
chitecture for Sparse Sensor Networks. Ad Hoc Net-
works, 1(2-3):215–233.
Tan, Y. K. and Panda, S. K. (2011). Energy Harvesting
From Hybrid Indoor Ambient Light and Thermal En-
ergy Sources for Enhanced Performance of Wireless
Sensor Nodes. IEEE Transactions on Industrial Elec-
tronics, 58(9):4424–4435.
TI (2014). MSP430FR5969 LaunchPad (TM) Devel-
opment Kit User’s Guide. http://www.ti.com/lit/
ug/slau535b/slau535b.pdf.
Ulz, T., Haas, S., Pieber, T., Steger, C., and Matischek, R.
(2017a). Sneakernet on Wheels: Trustworthy NFC-
based Robot to Machine Communication. In 2017
IEEE International Conference on RFID Technology
& Application (RFID-TA), pages 260–265. IEEE.
Ulz, T., Pieber, T., Steger, C., Matischek, R., and Bock, H.
(2017b). Towards trustworthy data in networked con-
trol systems: A hardware-based approach. In Emerg-
ing Technologies and Factory Automation (ETFA),
2017 22nd IEEE International Conference on, pages
1–8. IEEE.
Yan, R., Sun, H., and Qian, Y. (2013). Energy-aware sen-
sor node design with its application in wireless sensor
networks. IEEE Transactions on Instrumentation and
Measurement, 62(5):1183–1191.
Ye, F., Luo, H., Cheng, J., Lu, S., and Zhang, L. (2002). A
Two-Tier Data Dissemination Model for Large-scale
Wireless Sensor Networks. In Proceedings of the 8th
annual international conference on Mobile computing
and networking - MobiCom 2002. ACM Press.
Zhang, F., Zhang, T., Yang, X., Zhang, L., Leng, K.,
Huang, Y., and Chen, Y. (2013). A high-performance
supercapacitor-battery hybrid energy storage device
based on graphene-enhanced electrode materials with
ultrahigh energy density. Energy & Environmental
Science, 6(5):1623.
PECCS 2019 - 9th International Conference on Pervasive and Embedded Computing and Communication Systems
64