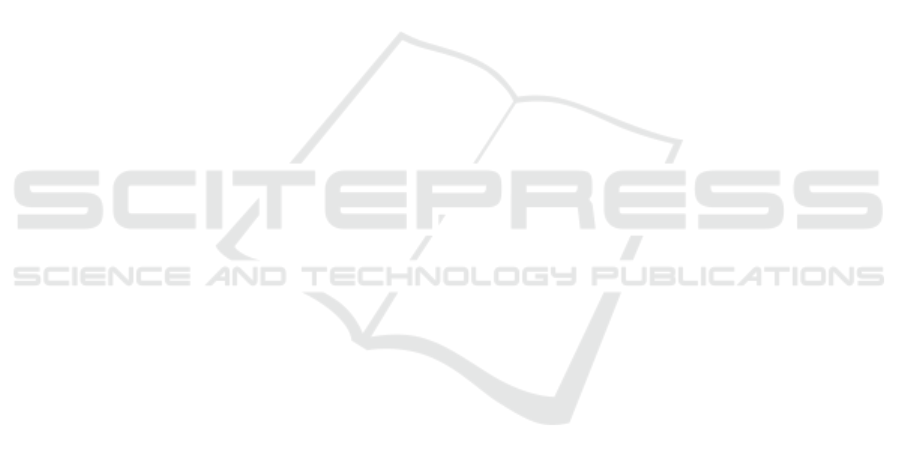
performed 10.54% slower than A*. Finally for dis-
tance traveled, RRT* performed 12.28% slower than
A*. For both scenarios regarding the standard devia-
tion, it is concluded that, as the complexity of the en-
vironment increases the standard deviation increases
for both algorithms. However, as RRT* has non-
deterministic behaviour, it increases by a higher order
of magnitude than A*. In addition, if the cell size for
A* was reduced, i.e, the map resolution increases, the
memory and processing time required would increase
exponentially.
For future work tests with both algorithms will be
implemented in a real scenario.
ACKNOWLEDGEMENTS
This work is financed by the ERDF – European
Regional Development Fund through the Opera-
tional Programme for Competitiveness and Interna-
tionalisation - COMPETE 2020 Programme within
project POCI-01-0145-FEDER-006961, and by Na-
tional Funds through the FCT – Fundac¸
˜
ao para
a Ci
ˆ
encia e a Tecnologia (Portuguese Foundation
for Science and Technology) as part of project
UID/EEA/50014/2013.
REFERENCES
Bohlin, R. and Kavraki, L. E. (2000). Path planning us-
ing lazy prm. In Proc. ICRA. Millennium Conf. IEEE
Inter. Conf. on Robotics and Automation. Symposia
Proc., volume 1, pages 521–528. IEEE.
Brito, T., Lima, J., Costa, P., and Piardi, L. (2017). Dy-
namic collision avoidance system for a manipulator
based on rgb-d data. In Iberian Robotics conference,
pages 643–654. Springer.
Cheng, Y. and Wang, G. Y. (2018). Mobile robot navigation
based on lidar. In 2018 Chinese Control And Decision
Conference (CCDC), pages 1243–1246. IEEE.
Choset, H. M., Hutchinson, S., Lynch, K. M., Kantor, G.,
Burgard, W., Kavraki, L. E., and Thrun, S. (2005).
Principles of robot motion: theory, algorithms, and
implementation. MIT press.
Ducho
ˇ
n, F., Babinec, A., Kajan, M., Be
ˇ
no, P., Florek, M.,
Fico, T., and Juri
ˇ
sica, L. (2014). Path planning with
modified a star algorithm for a mobile robot. Procedia
Engineering, 96:59–69.
He, D.-Q., Wang, H.-B., and Li, P.-F. (2018). Robot
path planning using improved rapidly-exploring ran-
dom tree algorithm. In 2018 IEEE Industrial Cyber-
Physical Systems (ICPS), pages 181–186. IEEE.
Kavraki, L., Svestka, P., and Overmars, M. H. (1994).
Probabilistic roadmaps for path planning in high-
dimensional configuration spaces, volume 1994. Un-
known Publisher.
Lima, J. and Costa, P. (2017). Ultra-wideband time of flight
based localization system and odometry fusion for a
scanning 3 dof magnetic field autonomous robot. In
Iberian Robotics conf., pages 879–890. Springer.
Lima, J., Gonc¸alves, J., and Costa, P. J. (2015). Modeling of
a low cost laser scanner sensor. In CONTROLO’2014–
Proceedings of the 11th Portuguese Conference on
Automatic Control, pages 697–705. Springer.
Loong, W. Y., Long, L. Z., and Hun, L. C. (2011). A star
path following mobile robot. In 2011 4th Inter. conf.
on mechatronics (ICOM), pages 1–7. IEEE.
Moon, C.-b. and Chung, W. (2015). Kinodynamic planner
dual-tree rrt (dt-rrt) for two-wheeled mobile robots us-
ing the rapidly exploring random tree. IEEE Trans. on
indust. electro., 62:1080–1090.
Noreen, I., Khan, A., and Habib, Z. (2016). A comparison
of rrt, rrt* and rrt*-smart path planning algorithms.
Inter. Jrnl. of Comp. Sci. and Net. Sec., 16(10):20.
Okubo, Y., Ye, C., and Borenstein, J. (2009). Characteriza-
tion of the hokuyo urg-04lx laser rangefinder for mo-
bile robot obstacle negotiation. In Unmanned Systems
Technology XI, volume 7332, page 733212. Inter. Soc.
for Opt. and Phot.
Piardi, L., Lima, J., and Costa, P. (2018). Development of
a ground truth localization system for wheeled mobile
robots in indoor environments based on laser range-
finder for low-cost systems. In Proc. of 15th In-
ter. Conf. on Informatics in Control, Automation and
Robotics-ICINCO’18, pages 341–348. SciTePress.
Plaku, E., Bekris, K. E., Chen, B. Y., Ladd, A. M., and
Kavraki, L. E. (2005). Sampling-based roadmap of
trees for parallel motion planning. IEEE Transactions
on Robotics, 21(4):597–608.
Schwartz, J. T. and Sharir, M. (1983). On the “piano
movers” problem. ii. general techniques for comput-
ing topological properties of real algebraic manifolds.
Adv. in applied Mathematics, 4:298–351.
Ye, C. and Borenstein, J. (2002). Characterization of a 2d
laser scanner for mobile robot obstacle negotiation. In
Proc. IEEE Inter. Conf. on Robotics and Automation,
volume 3, pages 2512–2518. IEEE.
A Comparison of A* and RRT* Algorithms with Dynamic and Real Time Constraint Scenarios for Mobile Robots
405