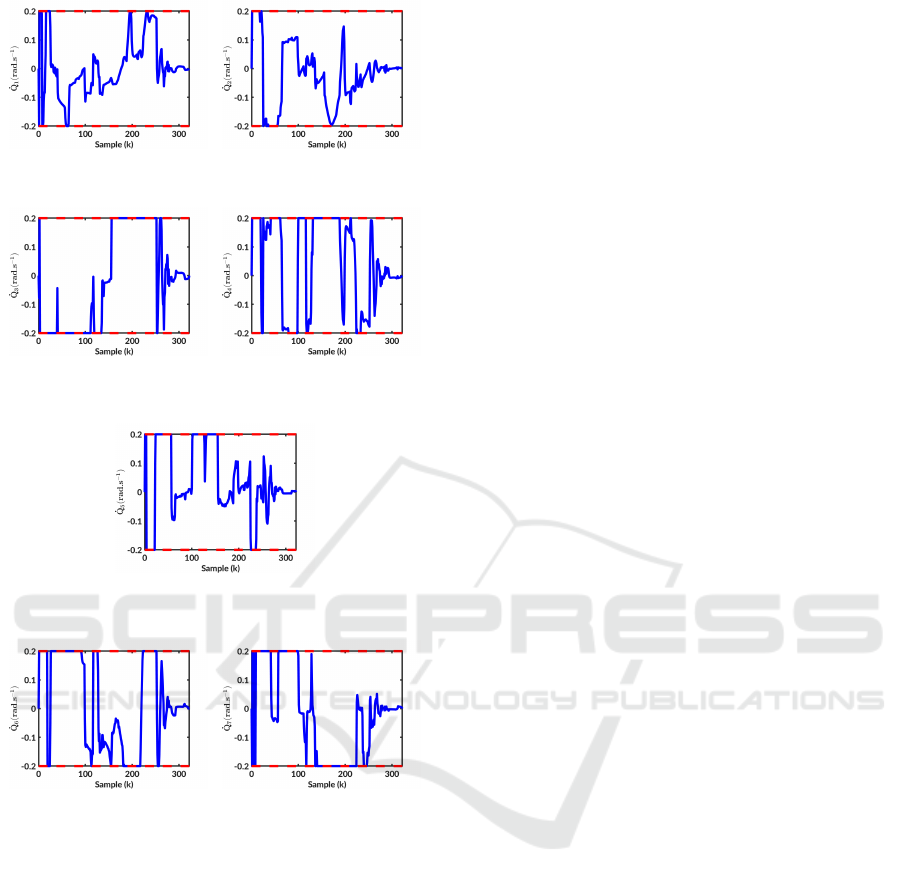
(a) ˙q
11
joints angular veloc-
ity
(b) ˙q
12
joints angular veloc-
ity
(c) ˙q
13
joints angular veloc-
ity
(d) ˙q
14
joints angular veloc-
ity
(e) ˙q
15
joints angular veloc-
ity
(f) ˙q
16
joints angular veloc-
ity
(g) ˙q
17
joints angular veloc-
ity
Figure 11: Right arm joints velocities - Blue solid: Joint
velocity value - Red dashed: Maximum velocities.
REFERENCES
Allibert, G., Courtial, E., and Chaumette, F. (2010). Pre-
dictive Control for Constrained Image-Based Visual
Servoing. IEEE Transactions on Robotics, 26(5):933–
939.
Chaumette, F. and Hutchinson, S. (2006). Visual servo con-
trol. i. basic approaches. IEEE Robotics & Automation
Magazine, 13(4):82–90.
Diehl, M. and Mombaur, K., editors (2006). Fast motions
in biomechanics and robotics: optimization and feed-
back control. Number 340 in Lecture notes in con-
trol and information sciences. Springer, Berlin ; New
York. OCLC: ocm71814232.
Durand-Petiteville, A., Le Flecher, E., Cadenat, V., Sen-
tenac, T., and Vougioukas, S. (2017). Design of a
sensor-based controller performing u-turn to navigate
in orchards. In Proc. Int. Conf. Inform. Control, Au-
tomat. Robot., volume 2, pages 172–181.
Foley, J. A., Ramankutty, N., Brauman, K. A., Cassidy,
E. S., Gerber, J. S., Johnston, M., Mueller, N. D.,
O’Connell, C., Ray, D. K., West, P. C., Balzer, C.,
Bennett, E. M., Carpenter, S. R., Hill, J., Monfreda,
C., Polasky, S., Rockstr
¨
om, J., Sheehan, J., Siebert,
S., Tilman, D., and Zaks, D. P. M. (2011). Solutions
for a cultivated planet. Nature, 478:337–342.
Garage, W. (2012). Pr2 user manual.
Grift, T., Zhang, Q., Kondo, N., and Ting, K. C. (2008). A
review of automation and robotics for the bio- indus-
try. Journal of Biomechatronics Engineering, 1(1):19.
Hajiloo, A., Keshmiri, M., Xie, W.-F., and Wang, T.-T.
(2015). Robust On-Line Model Predictive Control for
a Constrained Image Based Visual Servoing. IEEE
Transactions on Industrial Electronics, pages 1–1.
Lars, G. and Pannek, J. (2016). Nonlinear model predictive
control. Springer Berlin Heidelberg, New York, NY.
Le Flecher, E., Durand-Petiteville, A., Cadenat, V., Sen-
tenac, T., and Vougioukas, S. (2017). Implementa-
tion on a harvesting robot of a sensor-based controller
performing a u-turn. In 2017 IEEE International
Workshop of Electronics, Control, Measurement, Sig-
nals and their Application to Mechatronics (ECMSM),
pages 1–6. IEEE.
Sauvee, M., Poignet, P., Dombre, E., and Courtial, E.
(2006). Image Based Visual Servoing through Non-
linear Model Predictive Control. In Proceedings of
the 45th IEEE Conference on Decision and Control,
pages 1776–1781, San Diego, CA, USA. IEEE.
Van Henten, E., Hemming, J., Van Tuijl, B., Kornet, J., and
Bontsema, J. (2003). Collision-free Motion Planning
for a Cucumber Picking Robot. Biosystems Engineer-
ing, 86(2):135–144.
Vougioukas, S. G., Arikapudi, R., and Munic, J.
(2016). A Study of Fruit Reachability in Orchard
Trees by Linear-Only Motion. IFAC-PapersOnLine,
49(16):277–280.
Zhao, Y., Gong, L., Huang, Y., and Liu, C. (2016a). A
review of key techniques of vision-based control for
harvesting robot. Computers and Electronics in Agri-
culture, 127:311–323.
Zhao, Y., Gong, L., Liu, C., and Huang, Y. (2016b). Dual-
arm Robot Design and Testing for Harvesting Tomato
in Greenhouse. IFAC-PapersOnLine, 49(16):161–
165.
Visual Predictive Control of Robotic Arms with Overlapping Workspace
137